In the context of the global coronavirus, masks have become a part of people's lives. Since medical masks are disposable, they inevitably place a significant burden on the environment. Recently, a new research by scientists has linked masks to batteries, while bringing new ideas to the two major problems of waste mask recycling and battery supply shortage.
Researchers at the Russian State University of Science and Technology (NUST MISIS) and colleagues from the United States and Mexico have developed a new technology that can use mask waste to produce cost-effective supercapacitor batteries, the battery housing is made of pharmaceutical blister packaging. The study was published in the February 2022 issue of the Journal of Energy Storage.
It is understood that the supercapacitor refers to a new type of energy storage device between the traditional capacitor and the rechargeable battery, which has the characteristics of rapid charging and discharging of the capacitor and the energy storage characteristics of the battery.
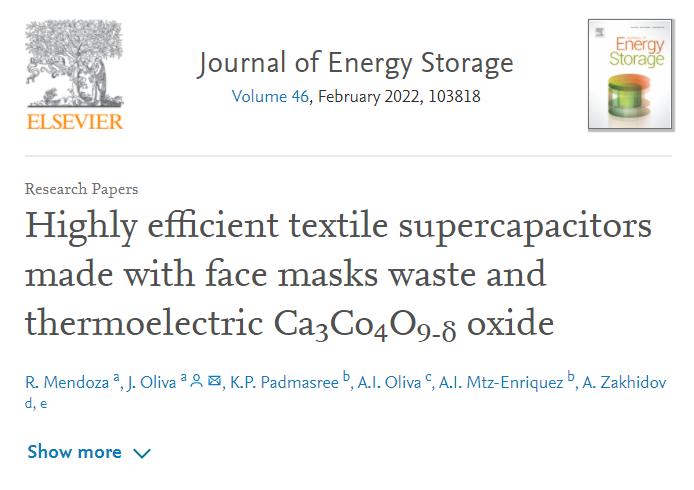
According to a 2020 study, as many as 130 billion masks were used every month on Earth after the coronavirus epidemic began. These masks turn into hundreds of tons of polymer waste that enter landfills, the oceans and other environments, or release toxic gases when burned. How to effectively recycle waste masks has become an urgent problem for scientists to solve.
Nowadays, through this new technology, only the purchase of graphene can transform medical waste such as masks and pharmaceutical packaging into thin, flexible and low-cost new batteries, and to a certain extent, the recycling of resources can be realized. The team's researchers say that using scrap as a raw material drastically reduces the cost of batteries, and can even be manufactured into disposable batteries if needed.
Compared with traditional similar products, this new battery has a high density of stored energy and capacity, lighter weight and lower cost. Previously, batteries manufactured using similar techniques had an energy density of about 10 watt-hours per kilogram (Wh/kg), and the capacity of this new type of battery has been increased to 98 watt-hours per kilogram. This means that the energy density of this battery is already close to the most common lithium-ion battery today, which has an energy density of about 100 watt-hours to 265 watt-hours per kilogram.
The manufacturing steps of the new battery are as follows: First, the mask material is sterilized using ultrasonic waves, immersed in the "ink" made of graphene, and then the material is pressed under pressure and heated to 140 ° C to form a conductive "particle" as the electrode of the battery. Then, between the two electrodes made of the new material, an insulating compartment, also made of mask material, is placed and then soaked in a special electrolyte. Finally, it is covered with a protective case made of pharmaceutical blister packaging material.
According to Professor Anvar Zakhidov of the university, traditional supercapacitor batteries require temperatures of up to 1000-1300 ° C for pyrolysis and carbonation, while the new technology reduces energy consumption by 10 times.
In addition, the researchers further improved the battery by adding CaCo oxide-type inorganic perovskite nanoparticles to the electrodes. This doubled the battery energy density to 208 Wh per kilogram, achieving a high capacitance of 1706 farads per gram, significantly higher than the capacitance of the optimal carbonization electrode without graphene added (1000 farads per gram).
Among them, the best performance of the first version of the supercapacitor battery after 1500 charge and discharge cycles and more than 10 hours of long-term discharge, still maintain 82% of the capacitance.
Previously, researchers have tried to use a variety of porous natural materials and waste products to make electrodes for supercapacitors, including coconut shells, rice husks, newspaper waste, car tire waste, and so on. However, the use of these materials often requires high temperature annealing (carbonization) in special furnaces. Due to the unique properties given to them by graphene saturation, masks proved to be a cheaper and easier material to process.
At present, the new battery developed by the team can be used for home appliances such as clocks and lamps. In the future, the researchers plan to apply this new technology to electric vehicles, solar power stations and other types of battery production.