Source: Content compiled by Semiconductor Industry Watch (ID: icbank) from protocol, thanks.
Intel's investment of up to $100 billion in a new set of chip factories outside Columbus, Ohio, will have a greater impact on the future of its manufacturing sector than any short-term political or supply chain problem it might solve.
Listen to President Joe Biden, U.S. Commerce Secretary Gina Raimondo, and Ohio Gov. Mike Dewan that the new plant — known in the world as a fab — will help address inflation, make America more competitive, reduce soaring car costs, ease chip supply chain shocks, and improve U.S. national security. $100 billion is also a big amount for Intel. It will be years before capacity goes live, and it's debatable whether the new chip factory in Ohio can actually solve any or all of these problems.
Politics aside; Intel's stakes in Buckeye's efforts could not be clearer.
The company has missed out on the opportunity to make billions of smartphone chips over the past decade, failing to build its own processors or win manufacturing contracts from other mobile giants. That has cost the company dearly — Intel hasn't benefited from its technology-building know-how, and chip manufacturing has even outpaced the output of its PC or server business. After a long period of chaos, chipmakers such as TSMC and Samsung seized on Intel's weaknesses and leapfrogged the Silicon Valley giant's once manufacturing leadership.
Led by Intel CEO Pat Gelsinger, the company has vowed to regain its former position, reverse the performance of its products in the short term, and regain manufacturing supremacy in the future. "Intel is committed to restoring end-to-end leadership, innovation, and manufacturing in the U.S.," Gelsinger said Friday. "We're doing our part, but we can't do it alone."
To achieve this, Intel is doubling down on its own fabless chipmaker foundry operations. It also uses extreme ultraviolet lithography technology that other companies such as TSMC have used to successfully manufacture advanced chips.
Ohio is an important part of that comeback plan. As part of the company's renewed manufacturing push, Intel has announced a $20 billion expansion of its sprawling plant in Arizona and a $3.5 billion expansion of its packaging facility in New Mexico. It also recently said it plans to announce two new sites in Europe in the coming months and could invest up to $95 billion over the next decade.
For its part, Intel's Ohio plan doesn't determine whether it can regain manufacturing leadership, but they're just the beginning.
Harvard Business School professor Willy Shih estimates that the first plant won't be operational until 2025 and could require a $20 billion investment to buy Intel enough capacity to start producing advanced manufacturing capabilities of 40,000 wafers per month. Currently, Shih estimates that Intel's highest-volume plant produces about 100,000 wafers per month.
But because Intel has invested in more advanced manufacturing technologies, mass production in Ohio will be very expensive. It's not the only chipmaker working hard to lead the industry.
Moore's Second Law
Intel's bets in Ohio, Arizona and elsewhere are a huge risk for the company. But under a little-known law enacted in 1995 by Intel co-founder Gordon Moore, today's hefty prices will almost certainly dwarf the costs you'll have to spend in the future to stay competitive.
His first "law" is well known and cited: Moore observed about 60 years ago that the number of transistors integrated into integrated circuits would double roughly every two years, and the machines they drove would become cheaper. This observation has been true for a long time, but today, its authenticity is a matter of debate among chip giants.
Moore published another important paper in 1995 that made a different but powerful look at semiconductor manufacturing. Moore began to worry about the cost of the tools needed to make the chips, and those costs had begun to grow at an exponential rate. He worries that this trend will continue until it is economically impossible to build new factories.
Moore wrote: "The rise in the cost of new technologies is very worrying. "The cost of capital is growing much faster than industry revenues." We can no longer compensate for the increasing costs by increasing production and equipment utilization. Just as the word 'smart' in device complexity disappears when there's no more room for smarter, there's not much room for manufacturing efficiency. ”
Moore's second most famous observation is not yet fully realized for Intel and other companies. But the list price of the latest generation of tools is staggering, and the cost is only getting higher.
'High-risk games'
Intel has been keeping a secret about its portfolio of chips it plans to make at its Ohio facility, but says it plans to deploy next-generation EUV technology there. Existing EUV machines are expensive, costing about $180 million each. The next generation, known as the high-value aperture EUV, costs about twice as much, and Intel has promised to buy the first tool made exclusively by Dutch ASML.
Lithography tools such as the High NA EUV machine have long been the most expensive bottlenecks in manufacturing output. But fabs also need hundreds of other tools, each of which could cost tens of millions of dollars.
"You think you'll surprise you with $150 million for a tool, but if you see how much Intel pays for a High NA [device], it's going to upend your imagination," Shih says. "In [the scale of Intel's Ohio fab], they're going to have about 1,000 different tools, and each tool costs between a few million and tens of millions."
But while these prices may seem exorbitant, the real risk is that Intel may not invest cash in manufacturing at the same rate as some of its competitors. Late last year, Intel said it would spend as much as $28 billion on its 2022 capital expenditure plans, which could include part of the cost of starting construction in Ohio. The other six Ohio fabs, the remaining portion of the $100 billion total cost, are dependent on Congress funding a $52 billion subsidy program that will help Intel pay the price.
"We think $20 billion is a lot of money," Shih said. "The easiest thing that comes to mind is that Intel will put all its money into it and catch up. But will it catch up, or will it keep up? ”
TSMC can already produce far more wafers than Intel — about $1 million a month — and has pledged to spend up to $44 billion in 2022. The tens of billions of dollars will expand its fabs in Taiwan and Chinese mainland, as well as part of a $12 billion plant outside Of Phoenix.
Samsung is one of the other companies that use EUV technology to make advanced chips and will spend $42 billion on capital equipment this year. Samsung also plans to build in the U.S. and has pledged to invest $17 billion in the construction of a new plant in Taylor, Texas, which is expected to begin operations in 2024.
"It's a high-stakes game that requires a lot of money because the equipment is too expensive and the technology is too hard," Shih said.
★ Click [Read the original] at the end of the article to view the link to the original article!
*Disclaimer: This article is original by the author. The content of the article is the author's personal opinion, semiconductor industry observation reprint is only to convey a different point of view, does not mean that semiconductor industry observation endorses or supports the view, if there is any objection, welcome to contact semiconductor industry observation.
Today is the 2933rd content shared by Semiconductor Industry Watch for you, welcome to follow.
Wafer | integrated circuit | devices | automotive chips | storage | TSMC | AI | packages
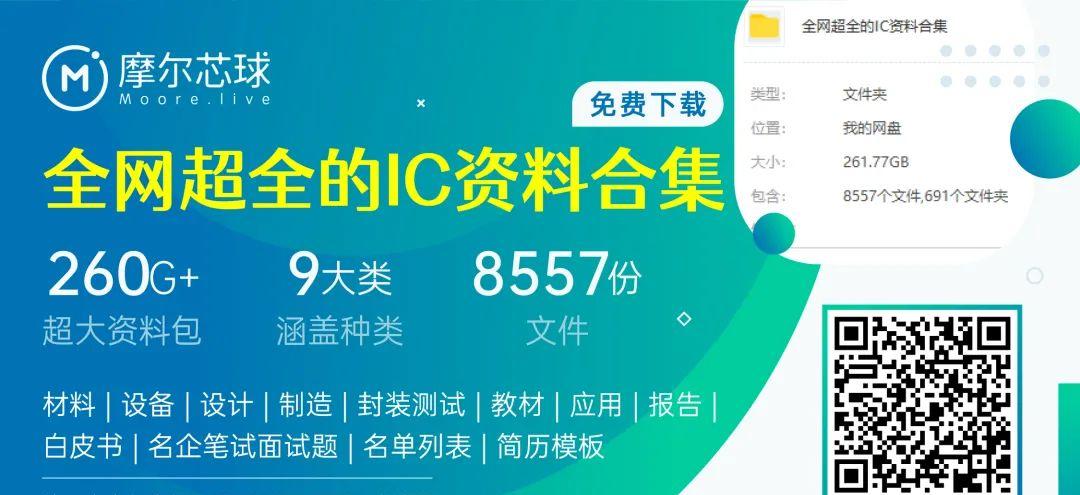
Link to the original article!