Measures to prevent multi-dimensional agglomeration of livestock and poultry include: selecting a stable monomer dosage form, reducing the moisture of the carrier, optimizing the formulation process, controlling the processing and storage environment, improving the quality of product packaging, and avoiding long-term stacking and extrusion.
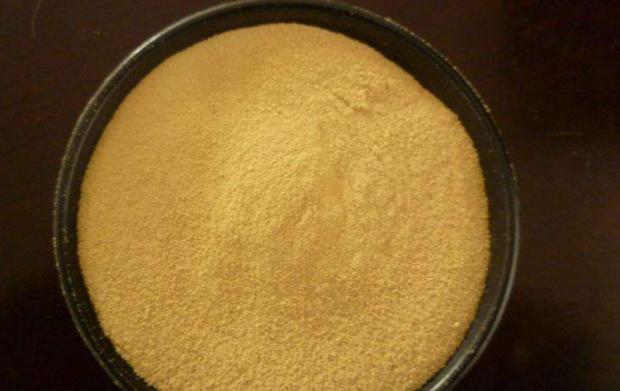
1. Select a stable monomer dosage form
Various vitamin monomer raw materials have different dosage forms, and commercial dosage forms with good stability should be selected when purchasing. In terms of stability alone, vitamin A palmitate> vitamin A acetate, nicotinamide menaquinone (MNB) > dimethylpyrimidinyl alcohol methanate (MPB) > sodium bisulfite menaquinone (MSB), thiamine nitrate stability > thiamine hydrochloride, 80% granular vitamin B2> 98% powder vitamin B2, niacin > niacinamide, calcium pantothenate> pantothenic acid> pantothenic acid, vitamin C phosphate> envelope vitamin C> common vitamin C.
2. Reduce the moisture of the carrier
More than a dozen vitamin monomers in livestock and poultry multidimensional products are active substances with different chemical properties, and the moisture content of the carrier directly affects the stability of the active components, because all chemical reactions are based on water as the medium. The moisture content of inorganic carriers is low, generally controlled below 3%, while organic carriers are relatively high, generally controlled below 7%. If the moisture is too large, it is very easy to make the product hygroscopic and agglomerate, and the active substance is greatly accelerated under the condition of water as a medium, and the chemical reaction speed is greatly accelerated, and it is very easy to agglomerate during production and processing. Carriers with high water content must be dried in advance to ensure that livestock and poultry multivitamin products do not appear to be tidal-absorbing and clumping during the production, processing and transportation and storage. The moisture of the organic carrier is easy to exceed the standard and drying is more difficult, the initial moisture of general grain and agricultural and sideline products is mostly between 12% and 14%, but when used as a multi-dimensional carrier for livestock and poultry, it needs to reach less than 7%. At present, there are two main ways of drying: hot air circulation drying and microwave heating drying. Because organic carriers such as defatted rice bran, corn flour, secondary flour, etc., small particle size, high dust content, baking must use low temperature drying process, otherwise it is very easy to cause coking, carbonization phenomenon, and even cause material combustion, dust explosion and other accidents, should be highly valued.
3. Optimize the formula process
The monomer concentration in the multi-dimensional formula should be moderate, not too high, and the basic carrier dosage must be guaranteed. The amount of carrier should generally be greater than 50%, and the minimum should not be less than 40%, otherwise it cannot play the role of carrying dilution and isolating vitamin monomers. Multi-dimensional products with high monomer content can add anti-caking agents silica and sodium aluminuminate in an appropriate amount, and increase the amount of antioxidants.
4. Control the ambient temperature and humidity
The production and processing workshop, raw material library, finished product library, should have air conditioning, dehumidifier and other environmental temperature and humidity control equipment, and strictly maintain the temperature and humidity of the space within the appropriate range. The impact of packaging temperature on agglomeration is also particularly significant, if the material temperature is too high during packaging, the dissolved part of the crystal after cooling will recrystallize to form a salt bridge, resulting in agglomeration. Therefore, after the multi-dimensional product is mixed, before packaging, it is best to fully cool the finished product, so that its temperature is close to the ambient temperature, and then pack and seal and pack.
5. Improve the quality of product packaging
Product packaging bags should be made of high-quality composite materials, strong and durable, and sealed against light. Vacuum packaging is tightly sealed and does not leak flatulence bags.
6. Avoid stacking and squeezing for a long time
Livestock and poultry multidimensional products should not be stacked for a long time. Especially when the high-rise palletizing is stacked, the underlying product is squeezed for a long time and is prone to agglomeration, it is best to use shelf layered storage, reduce the accumulation height of the product, reduce the pressure on the product during storage, thereby reducing the possibility of agglomeration. Purchase quantities appropriately to speed up inventory turnover.