記者 |
編輯 |
1
雖然電車已經發展成熟,但燃油車主還是會更傾向燃油車。如何在在盈利的同時生産出物美價廉并具有長續航的車型是電車制造商将面臨的挑戰。
海克斯康對416名全球汽車專業人士進行了調查,調查顯示,大多數受訪者認為,電動汽車會在2026-2028年才能與燃油汽車價格持平。在歐洲和美國,36%的受訪者認為直到2028年以後電動車價格才能與燃油車價格相比對,47%的人确信價格是消費者最大的顧慮,高昂的價格是電動車無法普及的一大障礙。
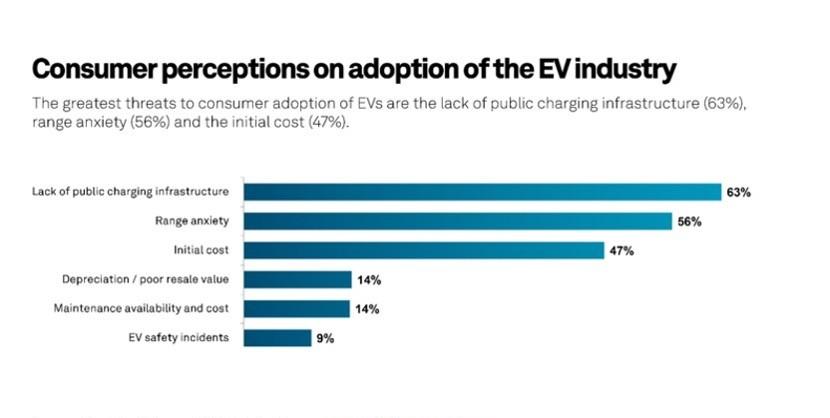
圖1
消費者對電動車的期待是提高續航能力(84%)和降低價格(60%),但制造商如何才能平衡這兩大需求?增強續航能力意味着投入更多的成本在電池上,同時還需要投入更多成本來減輕車體重量。
盡管疫情使得成本提升,産量變低,但制造商仍選擇降低價格來吸引消費者(見圖1)并證明了這一決策的正确性。調查還顯示,續航問題仍然是消費者的顧慮之一,隻有采用續航更長的電池才能解決這一問題,但是長續航電池意味着将大大增加生産車輛的成本。
受訪者認為價格是燃油車過渡到電車的最大挑戰之一,是以制造商需要考慮如何平衡售價與成本。分析師認為,由于開發成本較高,大多燃油車品牌現在才看到電動車潛在利潤。同時解決降低價格、增加利潤和延長續航裡程沖突需求的唯一方法是提高整個行業的效率。
制造業的悖論式困境是電車購買人數少,使得單價居高不下;研究結果顯示,由于電動汽車訂單量低,買家無法滿足規模經濟,供應商也無法實作規模經濟。
圖2
對于傳統制造業,提高效率意味着提高産量,提高産量是大型代工廠的根本。但現在的制造商想要縮短上市時間就必須提高效率,提高效率就必須提高零件生産數量,這意味着若使用智能,或資料制造,必須從生産零件開始。
許多代工廠已經使用成本計算功能很多年,包括在前期階段CAD軟體來輔助工廠中的房間生産。現在工廠的需要更加靈活、協作性強的團隊将前期開發和後期組裝結合起來同時進行,并驅動資料來快速解決問題。
現在成功的制造商通過使用仿真密集型方式成功地縮短從設計到生産的時間,并證明了虛拟樣機的價值,同時他們的創新周期正在縮減。這種生産模式有助于降低車輛成本,同時及時預測并解決潛在的缺陷,以避免不必要的支出和時間上的延誤。
法雷奧是此制造原則的一個成功例子,它與海克斯康合作開發了一種新的電力驅動裝置,法雷奧的工程師們利用軟體迅速得出了多種設計概念,使用現有的部件完成組裝,并獲得了PACE獎。這種方式采用了子產品化設計,開發時間縮短了7-9個月,适用于從電動機車和電動自行車到電動汽車的多種應用,有效的降低了制造成本,法雷奧使用此模式将雪鐵龍AMI One的上市時間從24個月縮短到18個月。
讓各部門一起合作最明顯的好處是系統的開發和生産更加一體化,但這樣做則需要增加供應鍊合作和垂直一體化的制造。
"智能制造 "一詞經常被用來描述各種利用資料的制造過程,利用資料驅動和機器人生産則需要使開發、生産群組裝之間互相連接配接。
以設計制造變速器為例。開發齒輪的時間可以通過使用品質資料來計算,在晶片開始制造之前就可以開始生産零件,實時計算出來的資料可以提前發現并預防問題的發生。當發現不可避免地問題時,資料便可找出問題所在并追溯到産生問題所在的材料、操作員、機床、工具等。比起原始手寫資料,以電子方式傳輸到機床和檢測裝置上大大降低了出現錯誤的機率。
使用資料來預測問題,并通過統計分析來與生産相協調,更加有助于縮小設計理念和産品制造品質之間的差距。
越來越多的制造商開始使用工程合作模式,這種模式大大提升了電動汽車産品的制造效率并提升了制造商的制造水準。例如,美國矽谷的純電豪華轎車品牌Lucid Motors通過合并各部門同時進行工作的方式,生産出了全新的驅動裝置。Lucid将電驅動裝置作為一個單一系統進行分析,并讓各部門的工程師共同協作,這一方式使公司創造出了市場上最小、最輕、最高效的驅動裝置。該73公斤,500千瓦驅動裝置由電機、變速器、差速器和反相器組成,此裝置具有市場領先的性能。
Arrival是一家英國電車初創公司,它正在開創垂直生産技術和機器人裝配,以實作高度自動化的微型工廠,這與傳統生産線截然相反。供應商需要實時調動人員,更新系統來滿足汽車制造業實時變化的需求,這種方式更像軟體公司生産方式。
過去,要想修複在生産過程中暴露出來的設計或軟體問題,需要多個部門協作才能定位問題、改進設計、獲得準許、進行驗證,最後再回到工廠繼續生産。這一過程可能持續幾周甚至幾個月的時間——這種情況現在仍時有發生——但最新的做法是利用更加動态且通常是自動化的方法來解決問題。
過去你絕不會聽到汽車公司說“我們在快速疊代“這樣的話,但當你考慮到當下電動車的發展速度時,這句話已經變得無比貼切。
汽車制造業想要成功必須擁有靈活性。通過疫情、供應鍊中斷等問題展現出了變化的常态性,現在供應商正在以多種方式解決這些變化。
靈活的制造流程可以滿足因産品設計變化而導緻的檢驗需求變化。這種全新模式及確定了産品品質又不會增加額外的勞動力,同時還使産品可以快速上市。
斯科達與海克斯康合作充分的展現了靈活性的好處,該公司使用新型機器人進行程式設計和控制軟體,将程式設計時間從數天縮短到僅四個小時。該公司為建立工廠配備HxGN機器人進行裝置自主檢測,同時對現有的生産線進行改造。該軟體以運用到車輛部件的設計、檢查中。目前,斯柯達汽車公司使用該軟體在生産線上更快地部署品質檢測環節,以便它們收集新車的生産資料。
電動車頻繁的改造要求是制造商最大的挑戰之一,由于電車是一個同時包含軟體和硬體的“産品”,是以生産電動車需要完善的制造流程。
是以,生産工廠中的房間和封閉物聯網必須進行改造,以建立協作并連接配接制造流程為目的,進而滿足快速組裝并及時發現缺少的零件。這樣做的前提是機器人和系統必須能夠互相聯絡,才能進行迅速檢測和及時糾正故障。
汽車制造商所面臨的挑戰是如何在電動車世界秩序中取得領先地位,這些挑戰既來自業内同時也來自是外界。在目前的訂單量下,如果想同時滿足價格優惠和更多車型的選擇,傳統的大批量制造生産線必須被更靈活的制造所取代,才可以加快上市速度。