文 |李浩賢
提升電動車續航主要有兩種辦法,一種是圍繞三電以及周邊技術做文章,例如800V高壓平台、提升電機效率、降低車身風阻系數、應用SiC等等。另一種是圍繞電池能量密度做文章,例如被稱為“下一代電池”的固态電池,其能量密度是三元锂電池的兩倍以上,續航輕松破千不是夢。
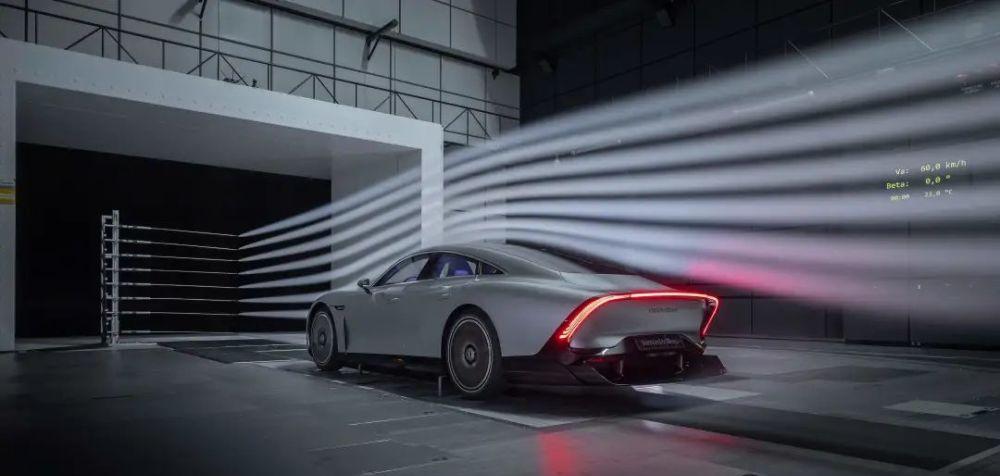
除此以外,電池組的內建形式也會大幅影響系統能量密度。其實這很好了解,就像一個行李箱,衣服折疊好合理擺放,肯定比亂扔亂放要裝得下更多。而電池就像行李箱裡的行李,隻要合理安排好空間就能放下更多,能量密度自然就提升了。
其實說白了就是如何提升電池艙的空間使用率。
發展過程
從電動車誕生開始,研發人員就一直絞盡腦汁提升電池包的空間使用率,我們不妨先來回顧一下電池內建技術的發展過程。
從上圖可以看到,電池內建技術目前一共分為三個階段,模組化、CTP、CTC,簡單來講這是一個從繁至簡的發展過程。
在第一階段即模組化階段,一個個電芯和相關零部件組成電池模組,而大家常見的電池包,就是由若幹個電池模組,加上BMS、配電子產品、冷卻系統等部件組合而成。從下圖可以看到,該電池包含十個電池模組(橙色蓋),目前在售新能源車大多采用類似的模組化技術。
通過這種模組工藝,可大大降低裝配複雜程度,生産效率得以提升。此外,子產品化設計可單獨更換損壞的模組,有利于動力電池維修保養,降低維護成本。但所帶來的問題是模組的應用會增加許多其他零部件,緻使電池包的品質和成本增加,空間使用率也留下很大優化空間。
是以,CTP技術逐漸走上舞台。CTP全稱為Cell To Pack,字面意思是去除模組,直接把電芯安裝在電池包内。但目前CTP有兩種技術路線,一種是以大模組替代小模組的方式,另一種才是完全無模組的方案。
第一種路線很好了解,無非就是采用大電芯和大模組,核心是減少模組數量。以特斯拉Model 3為例,它由4個長度約2米的大模組組成,而之前特斯拉 Model S則由16個小模組組成,這樣做能大大減少殼體的占比,提升空間使用率。相較于小模組電池包,大模組可以使體積使用率提升15%-20%,零件數量減少40%,生産效率提升50%并降低動力電池的制造成本。
上圖為Model 3大模組,下圖為早期Model S的小模組
而真正的CTP無模組方案,就是大家所熟悉的比亞迪“刀片電池”。具體是如何實作的,我想一張圖勝過千言萬語。
不知道大家有沒有察覺,哪怕是比亞迪無模組CTP,厚重的電池包殼體依然是存在的,這意味着電池的空間使用率仍沒有達到極緻的狀态,那究竟有沒有辦法把電池殼體也消滅掉呢?
有!它就是第三階段的CTC(Cell to Chassis)
CTC的好處
如果說CTP是消滅了電池模組,那麼CTC就是消滅了電池包,是CTP的進一步演化。
以特斯拉的CTC為例,它直接将電芯內建在汽車地闆架構内部,相當于車架變成了一個電池托盤,電芯就填充在托盤裡,電池上蓋肩負密封電池與車身地闆兩項功能,座椅則直接裝在上蓋。
沒有了電池包作為載體,帶來的好處和風險同樣都是顯而易見的。
1,資料顯示,在特斯拉車身一體壓鑄技術以及CTC技術的使用下,新車有望減重10%,續航有望增加14%,制造成本和流程也得到大幅優化。
2,電池直接填充在底盤内,意味着電池成為了車身結構的一部分,白車身扭轉剛性更強。
3,由于地闆與上蓋闆合二為一,乘員艙空間得到進一步釋放,後排座小闆凳的感覺能得以優化。
但有得就必有失,電池埋在車身内也意味着,對于單個電芯是無法進行維修和更換的,碰撞導緻底盤結構受損時,CTC方案可能需要整體更換車架+電池。
又因為少了傳統的電池包上蓋,改由車身+下蓋負責密封,對乘員艙防熱失控設計提出了新挑戰,也就是安全性上如何得到保障成為了難題。是以,特斯拉、甯德時代、比亞迪等頭部企業均未實作CTC的量産。
甯德時代預計2025年才推出高度內建化的CTC電池系統,可想而知工程難度有多大。
零跑版CTC
然而就在本周一,中國電動新勢力零跑汽車,宣布實作CTC電池底盤一體化技術量産,搭載該技術的零跑C01,将成為全球首款無獨立電池包的電動車。消息一出瞬間引起了汽車圈的一片嘩然。
根據官方的說法:零跑智能動力CTC技術應用車身結構作為電池包外部結構,通過取消電池上部結構(上蓋),減少備援的結構設計,使整車垂直空間增加10mm,電池布置空間增加14.5%,綜合提升整車續航裡程10%,車身扭轉剛度提升25%至33897Nm/rad,減重15kg,車身輕量化系數提升20%。
看完這段話和結構圖,相信已經有讀者發現零跑CTC技術的“巧妙”之處了。
零跑是将承載式車身結構重新做了分布,将車輛底部電池包高度提升,從原先外挂電池布局進而整合至底盤内部,讓電池骨架結構和底盤骨架結構合二為一,借用底盤基本結構,利用車身縱梁、橫梁形成完整的結構。
相比特斯拉追求極緻的方案,零跑的CTC方案更為妥協。其本質在于将電池包的上蓋去掉,但電池包其他部分是基本不變的,依然保留下蓋。這是一種折中的思路,好處是整車的裝配線,工藝等不需要做大的調整,更容易實作量産。
此外,特斯拉是将電芯直接埋在底盤裡,而零跑則是将模組挂在底盤上,并沒有省略電芯模組這一過程,由于模組這個中間形态依然存在,是以零跑的CTC方案在空間釋放效率、內建度、成本優勢、配件備援等方面都不如特斯拉極緻,是以零跑CTC更像是階段一 + 階段三的組合體。
這樣做除了在工程上更容易實作以外,好處就是維修性好,畢竟下蓋是可以打開的,壞了直接開蓋維修就是了,這可能是零跑重點考慮的。
必須要指出的是,無論是特斯拉的方案還是零跑的方案,兩者都屬于CTC技術路線的分支,相當于CTP裡大模組和無模組兩種技術路線。
雖然零跑的CTC并不是真正的電芯到底盤的CTC,但最終仍然實作了提高效率的目的,而且勝在容易實作,就好像追不到的女神,永遠隻能是女神,盲目挑戰高難度沒有意義。
零跑表示搭載該技術的旗艦轎車車C01将于近期開啟首秀及亮相,毫無疑問,零跑這次搶盡了先機和足夠多的目光,手握這張王牌無疑能讓零跑踏上更高的市場地位。
老實說,零跑這次釋出CTC屬實一鳴驚人,作為國内為數不多軟硬體一體化全域自研的車企,我開始有點期待零跑在軟體上(智能駕駛)會打出什麼樣的王炸了。