(報告出品方/作者:浙商證券,邱世梁,劉欣暢)
1. 布局新能源,壓鑄全覆寫
1.1. 鋁壓鑄行業領軍企業
掌握高壓、低壓和重力鑄造三大鋁壓鑄工藝,深耕汽車鋁壓鑄件。公司主營汽車鋁壓鑄精密件和車身件制造,實作高壓、低壓和重力鑄造三大鋁壓鑄工藝全覆寫,高壓壓鑄工藝主要應用于傳統燃油車和新能源汽車的動力總成系統和車身結構件等,低壓壓鑄工藝主要應用于新能源車大三電系統和底盤系統等,重力壓鑄工藝主要應用于底盤系統等。公司客戶包括大衆、奔馳、特斯拉、蔚來、小鵬、理想等國内外知名車企以及采埃孚、麥格納等國際 tier1。
公司發展可以分為四大階段:1)1998-2014 年,公司實作了從小型家電壓鑄到汽車零部件壓鑄到高端鋁壓鑄車身件供應商的轉型;2)2014-2017 年率先切入新能源領域;3)2018-2020 年,國内産能全面擴産;4)2020 年之後,收購法國百煉從專注高壓壓鑄實作高壓、低壓、重力鑄造全覆寫,且在高壓基礎上發展一體化壓鑄。
第一階段:1998-2014 年,實作家電-傳統汽車鋁壓鑄件-鋁壓鑄車身件的兩次次跳躍。1998 年公司前身南海文燦成立,以家電和日用生活類壓鑄件起家,後逐漸轉型至汽車鋁壓鑄行業,成為格特拉克、博世、麥格納、采埃孚、法雷奧等諸多國際tier1 的供應商。2011 年公司開始布局鋁壓鑄車身件領域,首個訂單為奔馳國産化車型車身件,成為奔馳鋁壓鑄車身件國産唯一供應商。
第二階段:2014-2017 年,汽車高壓鑄件精耕細作,車身件率先切入新能源領域。2014年公司整體變更為股份公司,并獲得特斯拉 model S/X 車身件訂單,于2015 年開始進入特斯拉供應體系批量生産。2016 年公司車身件再獲蔚來汽車定點。公司搶先布局新車身件和新能源,積累了新能源車車身結構件的先發優勢。
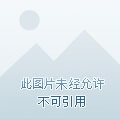
第三階段:2018-2020 年,融資上市并完成國内産能擴張。2018 年4月,公司正式在上交所 A 股上市,募資 8.39 億元;2019 年,公司發行可轉債,募資8 億元。公司募集資金主要用于投入天津雄邦、南通雄邦、江蘇文燦三個公司,擴充産能以比對未來發展。
第四階段:2020 年以來,公司通過并購法國百煉集團,實作技術、業務的協同和延伸,并前瞻布局一體化壓鑄,産品線全面擁抱新能源。2018 年之前公司專注于高壓壓鑄領域,2020 年 8 月公司收購法國百煉集團,實作了高壓、低壓、重力壓鑄工藝全覆寫,公司産品品類得以擴充。公司圍繞車身、底盤、大三電、電池托盤/儲能箱體四類産品線,全面擁抱新能源,在手新能源訂單充沛。
公司為家族控股,唐氏家族控制公司 57.2%的股權。公司實際控制人為唐傑雄、唐傑邦,兩人為堂兄弟,合計直接或間接控制公司 34.33%的股份。唐怡漢、唐怡燦分别為唐傑雄、唐傑邦之父,唐氏家族合計控制公司 57.2%的股份,行動一緻。公司股權上雖為家族控股,但實際上僅唐傑雄先生參與公司實際經營,為公司董事長和總經理。
國内長、珠三角、環渤海三地區布局,全球實作亞、歐、北美三大洲覆寫。公司在文燦股份(佛山)、南通雄邦、江蘇文燦、天津雄邦設定生産基地,實作了珠三角、長三角、環渤海地區的布局。2020 年收購法國百煉集團,法國百煉在全球擁有10 個生産基地,分布在墨西哥、中國(武漢、大連)、法國、匈牙利、塞爾維亞等國家,完成了全球生産基地的布局。
文燦股份壓鑄技術行業領先,是國内鋁壓鑄龍頭企業。公司的優勢在于1)率先布局新能源,2014 年開始公司逐漸拓展特斯拉等新能源客戶,2019年國内四大生産基地均形成以新能源汽車用零部件為核心的産品生産體系;2)生産技術完備,公司深耕高壓鑄造,掌握重力鑄造及低壓鑄造技術,率先布局一體化壓鑄技術;3)受到客戶認可,公司下遊客戶包括采埃孚、博世、大陸、麥格納、法雷奧、本特勒等全球Tier 1 以及大衆、奔馳、寶馬、奧迪、雷諾等傳統車主機廠也包括特斯拉、蔚來、小鵬、理想等新能源主機廠。
1.2. 2021 年是公司經營拐點
12-19 年公司營收和歸母淨利穩健增長,收購法國百煉後收入體量進一步擴張。2012年-2019年公司營收和歸母淨利 CAGR 分别為 10.3%和 12.6%,2020 年8 月并表法國百煉,百煉 2020 年 8-12 月并表收入 10 億元,使公司收入規模進一步擴張。
18-19年行業下行和新産能投放共振導緻公司産能使用率較低、業績波動較大,20-21年疫情、缺芯、鋁價上漲等外部沖擊共振下導緻公司業績觸底,2021 年是公司經營拐點。2018-2019年公司營收同比增速分别為 4.05%、-5.09%,歸母淨利潤同比增速分别為-19.4%、-43.3%,利潤增速顯著低于收入增速主要是行業下行背景下新産能投産,2018年公司IPO募投項目天津雄邦建成開始投産,但是一般一個新産能建設完成後,還要進行産品試制、量産稽核、量産爬坡等階段,通常需要 2-3 年才能實作 100%達産,而18 年下半年開始國内乘用車開始負增長,并且 19 年國六切換影響公司主要客戶大衆的訂單,導緻公司新産能沒有得到很好的消化,産能使用率下降以及新工廠建成帶來的固定成本增加導緻公司歸母淨利潤下滑較多。
2020 年公司實作營收 26 億元,其中百煉并表貢獻收入10 億元(8 月百煉并表),文燦本身營收 16 億元,同比+4.1%,2020年公司實作歸母淨利潤0.84 億元,若剔除并購費用/利息以及百煉利潤,則文燦本身利潤體量約 1.55 億元,同比+119.3%,淨利率9.43%,同比+4.81pct,逆市大幅增長,主要原因為高附加值、高毛利率的車身結構件産品放量優化了公司盈利能力。
2021 年由于缺芯、鋁價大幅上漲、海外疫情反複、運費等外部多重沖擊,公司業績承壓。2021年前三季度公司收入 29.7 億元,同比+103.6%,主要是百煉貢獻了約16.6億元的收入,前三季度公司歸母淨利潤 0.69 億元,同比下滑7.2%。我們認為21年是公司經營拐點,2022 年開始随着車身(含一體化壓鑄)、底盤、大三電、電池托盤/儲能箱體四大類新能源業務放量,以及行業外部因素的消散,公司業績将釋放較大彈性。(報告來源:未來智庫)
2. 新能源催生一體化壓鑄浪潮
2.1. 從高壓壓鑄更新一體化壓鑄
鋁合金鑄造按照是否有外力作用分為壓力鑄造和重力鑄造。壓力鑄造又分為低壓鑄造和高壓鑄造,其中高壓鑄造是将金屬液倒入壓室,然後壓射杆将壓室中的金屬液高速推入澆道和型腔,并使其在高壓下凝固形成鑄件,填充時金屬液的流動速度在10-80m/s甚至更高,金屬液凝固時承受的壓力高達 40-120MPa,其産品具有表面光潔度好、尺寸穩定、可直接成型薄壁結構、生産效率高等優點。基于高壓壓鑄的基礎,真空高壓鑄造工藝增加了抽真空操作,可将型腔中的氣體抽出,金屬液體在真空狀态下充填型腔,減少了卷入的氣體,鑄件可進行熱處理,力學性能優于普通高壓鑄件。低壓鑄造是使金屬液從在較低壓力(0.01-0.05MPa)下,在密閉容器中沿着升液管自下而上流經升液通道、鑄型澆口,平穩填充型腔,随後增壓凝固的工藝,充型能力強但生産率較低。
一體化壓鑄本質上屬于高壓鑄造工藝。2019 年以前壓鑄機鎖模力通常在400-5000噸不等,汽車高壓鑄造工藝主要應用于發動機系統、變速箱系統、離合器等精密件,以及橫梁、縱梁、減震塔等車身結構件。一體化壓鑄指的是車身件的一體化,即原本設計中多個單獨、分散的小件經過重新設計高度內建,再利用壓鑄機進行一次成型,省略焊接的過程直接得到一個完整大零件,一體化車身件尺寸大、材料特殊、模具複雜、制造技術難度較高,需要大噸位壓鑄機進行生産。
高壓壓鑄工藝包括合模、射料、回錘、冷卻、充氮氣(惰性氣體)、離嘴開模、頂出、頂回等步驟。當壓鑄生産時,先将熔融的液态鋁合金倒入壓鑄機的壓射機構内,壓射機構将鋁液快速推入模具内并加壓成型,通過模具内的冷卻系統将鋁合金零件快速冷卻至固态,最後模具打開由機器手取出零件、清理噴塗脫模劑再進行下一循環生産,整個生産過程溫度極高、煙氣多、噪音大,業内通常使用自動化生産。
高真空壓鑄工藝加入高真空控制系統,需要高精度傳感器控制。工藝流程為模具關閉、倒料、真空開啟、型腔真空排氣、壓射、開模到位、取件、噴塗、再次關模到位等環節。在過程中,有高精度真空傳感器控制真空罐、熔杯排氣閥和型腔排氣閥,并通過參數設定來觸發四個接觸點:即熔杯真空開始、熔杯真空結束、型腔真空開始和型腔真空結束。
一體化壓鑄單個生産周期主要由抽真空-鋁液填充-成型-機加工環節組成。在鑄造型腔内會塗覆約 35ml 的潤滑油,壓鑄機關閉型腔抽出内部氣體,熔融狀态的金屬材料被高速壓入,模具與型腔接觸,溫度下降到 400 度時型腔打開,模具運送到逐冷卻槽,再經過剪裁,多餘的部分和不良産品會再次加工,特斯拉 Model Y 的一次一體化壓鑄周期完畢。
特斯拉一體化壓鑄工藝有兩大核心:一體化設計與一體化制造。在一體化設計上,特斯拉于 2019 年 7 月釋出專利“汽車車架的多向車身一體成型鑄造機和相關鑄造方法”,将一整套固定的模具放置在中心,四套可以移動的模具放置在四個不同方向。通過液态裝置,四個可移動模具與中心固定模具貼合,共同形成了一個封閉的空腔。熔融狀态的鋁合金會受壓力從四個移動模具上的澆築口壓入模具空腔,最終在空腔内彙合并凝固形成了大型的一體式壓鑄結構整件。
在一體化制造上,特斯拉向 IDRA 采購壓鑄機,實作一體化生産。零件一體化尺寸增大,對裝置的性能需求大幅提升。IDRA(力勁科技控股)專注于壓鑄機76年,其開發的 OL6200CS 裝置,可以提供最大 6218 噸的鎖模力(傳統高壓壓鑄的鎖模力通常在5000噸以下)。根據 IDRA 在 2011 年申請專利,其能夠将鑄造半模之間形成空腔,向空腔中注入帶有保護的熔融金屬,經由抽真空裝置在模空腔中産生負壓,能夠有效消除鑄造湍流産生的氣泡,有助于增強壓鑄材料的一緻性和提升壓鑄速度。
2.2. 特斯拉引領一體化壓鑄産業趨勢
特斯拉車身一體化上的程序可以分為三個階段:
1)第一階段,采用全鋁車身拼接。Model S、Model X 問世,采用了全鋁車身,但是仍然按照傳統的沖壓-焊接工藝路線進行整車開發。
2)第二階段,6000 噸壓鑄機用于生産 Model Y 後座闆。2020 年馬斯克在特斯拉batteryday 上宣布,Model Y 将采用一體式壓鑄後地闆總成,零件數量比Model3 減少79個,焊點大約由 700-800 個減少到 50 個,可将下車體總成重量降低30%,制造成本下降40%,制造時間由傳統工藝的 1-2 小時縮減至 3-5 分鐘。在特斯拉全球四大超級工廠中,均已部署 6000 噸以上的壓鑄機,其中弗裡蒙特工廠布局了 2 台、上海工廠布局了3台、柏林工廠将布局 8 台、奧斯汀工廠将布局 4 台以上。
3)第三階段,一體化下車體即将量産。2021 年特斯拉在柏林工廠開放日上展示了特斯拉一體化壓鑄底盤,計劃将用 2-3 個大型壓鑄件替換由370 個零件組成的整個下車體總成,重量将進一步降低 10%,對應續航裡程可增加 14%。未來特斯拉将向前車身一體化+後車身一體化+底盤電池包一體化內建的方向發展。
2.3. 一體化壓鑄優勢
一體化壓鑄工藝的優勢集中在降本、輕量化、提高生産效率上,有望颠覆沖壓焊接工藝。
成本降低
一體化壓鑄主要是取代傳統沖壓焊接工藝,零件數量和焊接工序大幅減少,沖壓零件、沖壓模具、沖壓裝置、焊接夾具、焊槍、檢具等所有傳統沖焊供應鍊環節均取消,對應的整個供應鍊投入大幅下降。
1. 裝置投入成本:過去數十個小件需要分别投入相應的産線、裝置、模具等費,一體化壓鑄後內建度大幅提升生産工序大幅精簡,帶來裝置産線等總投入的下降。
2. 焊接/塗膠成本:塗膠身為傳統焊接白車身一個重要步驟,用來解決因點焊産生的鋼闆間存在的縫隙。一體壓鑄車體使得零件面積大幅增加,不需彌補焊接钣金件間的縫隙,減少了塗膠工藝的成本。
3. 人工成本:一體化壓鑄的生産效率大幅提升,自動化率提升,國内主流焊接工廠往往配備 200-300 名生産線勞工,采用一體化壓鑄技術後,所需的技術員工有望縮減至原先的十分之一。
輕量化效果更優
一體化全鋁壓鑄白車身的重量将在200-250kg,而同級别鋼制車身的重量在350-450kg。重量降低約 150-200kg,在車身輕量化方面具有巨大優勢。例如Model Y的一體壓鑄後車身僅重 66 公斤,比尺寸更小的 Model 3 同樣部位輕了10-20 公斤。
生産效率大幅提升、供應鍊管理周期将被壓縮到極緻
Model Y 将 79 個零部壓縮成兩個零件,零件大幅減少,焊接點由原來的700-800個減少到 50 個,制造時間可從原先的 1-2 小時縮減至 3-5 分鐘。供應鍊環節縮短,供應商的審查、沖壓零件的采購定點、沖壓模具的制造、沖壓裝置的使用。焊接夾具的制造、焊接的使用、檢具的開發、零部件的物流運輸等環節将被縮減。管理周期壓縮,傳統汽車制造周期長、工作量大、重複性高,例如針對一些專業的外觀類零件,需要經過MB1、MB2、MB3 三輪比對,耗時近 6 個月,一體化後 MB 比對中車身所需要的周期将會縮短至 1~2 輪,有望節省 3~4 個月。
提高焊接處零件強度
傳統沖壓+焊接工藝在焊接處強度降低,一體化壓鑄一次成型,從根源上避免了焊接問題,同時在設計零件時可省略考慮安裝孔大小、安裝位置等問題,進而促成更優化的工程學結構。
2.4. 産業變革加速,多家主機廠積極推進車身一體化工藝
一體化壓鑄具備經濟性和高效性,電動化時代一體化程序将提速。相比于傳統車,在電動車時代我們認為主機廠将會加碼一體化壓鑄,主要有四點原因:1)一體化壓鑄的經濟性明顯,降低成本;2)一體化壓鑄的節拍更快,相比于傳統車電動車疊代周期更短,一旦推出爆品需要快速生産推向市場;3)電動車輕量化需求,與傳統車相比,由于續航焦慮電動車的輕量化需求增加;4)新勢力車企的入局增強了一體化壓鑄的可能性,電動車尚沒有完全平台化生産,尤其是新進入的新勢力車企沒有沖壓、焊接産能,轉型包袱小,更有動力和意願去推廣一體化壓鑄工藝。
主機廠、壓鑄機裝置廠、鋁壓鑄企業均大力布局一體化壓鑄。蔚來、理想、小鵬、華為/賽力斯、廣汽、福特、大衆、智己、小米都在談判/評估/定點/規劃一體化壓鑄鑄件,一體化壓鑄成為行業趨勢。
蔚來:2021 年 10 月,蔚來宣布成功驗證制造大型壓鑄件的免熱處理強韌化壓鑄鋁合金新材料,該材料是蔚來與帥翼馳聯合開發,将會應用在蔚來第二代平台車型上。2021年 12 月蔚來釋出新車 ET5,該車後座闆使用一體壓鑄工藝。
小鵬:購入 2 台 7300 噸壓鑄機,小鵬武漢工廠在正常的沖壓、焊接、塗裝工廠中的房間基礎上,增加一體化壓鑄工藝工廠中的房間,武漢工廠将引進一套以上超大型壓鑄島及自動化生産線。
高合:和上海交大輕合金國家工程中心達成戰略合作,全球首發TechCastTM超大鑄件用低碳鋁合金免熱處理材料,該材料有望應用于一體式大型壓鑄車身薄壁結構件、門蓋内闆、電池包殼體等超大鑄件上,并在高合汽車後續車型上大批量采用。
大衆:據德國《商報》,大衆将于 2026 年生産新一代電動汽車Trinity 項目,并将建立一座全新的工廠,大衆計劃在 Trinity 項目中引入一體化壓鑄技術。
沃爾沃:2021 年 10 月沃爾沃在瑞典挂牌上市,70%的募集資金将用于電動化轉型,包括在工廠中添置大型壓鑄機,以生産一體成型的車身以及新增電驅動和内置電池的生産線等
壓鑄機裝置廠:力勁集團、布勒、伊之密、海天金屬等裝置廠紛紛加碼大噸位壓鑄機制造。力勁,在全球壓鑄機市場的占有率超過 40%,率先開發出6000 噸壓鑄機,目前已開發出 12000 噸壓鑄機,是大噸位壓鑄機龍頭。布勒,2020 年釋出Carat 超大型兩模闆壓鑄機,2021 年布勒稱将發售 6100T 兩模闆壓鑄機,并宣布啟動Carat 840(8400T兩闆壓鑄機)項目,2021 年 7 月上海國際壓鑄展布勒釋出世界目前最大的9200噸超大型兩模闆壓鑄機。海天金屬,2019 年開始設計,2021 年 4 月在重慶美利信全球首發HDC8800噸壓鑄機,可實作包括新能源汽車在内的車身、底盤等大型結構件一體化。伊之密,公司 7000T 壓鑄機即将總裝。
鋁壓鑄企業:文燦股份、瑞立集團、美利信、拓普集團、泉峰汽車、廣東鴻圖愛柯迪等汽車零部件壓鑄企業也紛紛提前布局,但文燦股份走在最前列。文燦股份2021年上半年已向力勁集團采購 3 台(2 台 6000 噸和 1 台 9000 噸)超大型智能壓鑄單元;瑞立集團向力勁集團采購 3 台(6800 噸、8000 噸和 9000 噸)超大型智能壓鑄單元;重慶美利信與海天金屬簽約購買一套 HDC8800 噸超大型壓鑄機,聚焦“5G 通信”和“新能源+智能網聯汽車”兩大前瞻領域;拓普集團 2021 年 9 月向力勁科技訂購21 台套壓鑄單元,其中包括 6 台 7200 噸、10 台 4500 噸和 5 台 2000 噸的壓鑄裝置;泉峰汽車2021年啟動安徽馬鞍山汽車零部件智能制造項目建設,馬鞍山基地将增設2700 噸兩台,3000噸、4200噸、4400 噸、6000 噸、8000 噸各一台大型壓鑄裝置。愛柯迪的智能制造科技園項目拟購入 45 台壓鑄機,包括 1000 噸以上壓鑄機 35 台,包括了4 台4400 噸、2 台6100噸和2台 8400 噸,新能源汽車車身部件規格為 40 千克,産品方案顯示汽車電池系統單元産品規格為 10 千克,較現有産品規格提升;華朔科技訂購了力勁6800 噸、8000 噸超大型智能壓鑄單元各一台套,2000 噸大型智能壓鑄單元六台套,共計8 台套大型智能壓鑄裝備;廣東鴻圖購置了一台 6800 噸壓鑄機并于 1 月 22 日舉行6800T 底盤一體化結構件下線暨12000T 超級智能壓鑄單元合作簽約儀式,未來将結合客戶的發展方向在一體化前艙總成、一體化後地闆總成和一體化電池托盤等關鍵核心輕量化部件方面布局和發力。甯波海威在 2021 年 12 月 6600T 壓鑄單元結構件下線,且規劃在紹興基地安裝6 台6600T和9000T的大型壓鑄裝置,用于生産前機艙、後車體及電池箱體等産品。
2.5. 一體化壓鑄行業空間測算
2021-2025 年,一體化壓鑄 4 年 CAGR 達到 134.5%。汽車後座闆的單車價值約2200元,2021 年隻有特斯拉 model Y 應用,對應市場空間約9 億元。在單車價值上,随着一體化壓鑄的技術更新,車身一體化可應用範圍将從目前的後座闆擴充至前車身、底盤電池托盤、車門,對應單車 ASP 有望從 2200 元提升至 14400 元;在普及率上,根據目前主機廠的一體化意願,越來越多的車企将逐漸采用一體化壓鑄進行生産,2025 年搭載一體化壓鑄車型銷量有望快速提升至 303 萬輛。根據我們測算,對應2021-2025 年一體化壓鑄的市場空間将從 9 億元左右提升至 273 億元左右,CAGR 為134.5%。(報告來源:未來智庫)
3. 一體化壓鑄門檻較高
一體化壓鑄工藝壁壘為系統性壁壘,展現在材料+模具+壓鑄過程控制上。
技術難點一:材料壁壘
由于一體化鑄件規格更大,考慮形變問題無法進行熱處理,需要材料創新,研發出特殊的免熱處理鋁合金。傳統的鋁壓鑄車身件如減震塔為滿足高延伸率保證鉚接性能,通常需要進行 T7(固溶+時效熱處理),但是一體化鑄件尺寸更大(後座闆投影面積有1.5mX1.5m),進行熱處理容易發行形變,是以需要特殊的免熱處理鋁合金,在不需要進行熱處理的同時也能保證産品組織和力學性能。另外,使用免熱處理材料因為節省了熱處理工序,一定程度上也能提升良品率。
應用于一體化壓鑄的免熱處理鋁合金材料要具備以下幾個特點:1)有較好的塑型體流變性能,即在壓力作用下,鋁合金仍具備良好的流動性,便于填充複雜的結構體,減少逐漸内收縮空洞;2)線收縮率更小,且有一定的高溫強度,以免鑄件産生裂紋和變形,提高鑄件尺寸精度;3)結晶溫度範圍小,可以減少鑄件中收縮孔洞産生的可能性;4)具備更好的高溫固态強度,防止模具開模時推出鑄件産生變形或破裂;5)在常溫下應具有一定的強度,提高壓鑄件的機械強度和表面硬度;6)與壓鑄型不發生化學反應,親和力小,防止粘型和鑄件、鑄型互相合金化;7)在高溫熔融狀态下不易吸氣、氧化,以便能滿足壓鑄時需長期保溫的要求。
免熱處理鋁合金需要兼備韌性與強度。一體化壓鑄的材料具有一緻性,車身在不同部位對受力的不同要求以及不同部位對強度和韌性的要求均要滿足,而一體化車身件具有尺寸大、壁薄、結構複雜等特征,力學性能要求更高。韌性相關的結構件的抗拉強度通常≥180mpa,伸長率≥10%;強度相關的結構件,抗拉強度通常≥210mpa,伸長率≥7%。根據《壓鑄周刊》,首選免熱處理的高強高韌鋁合金的延伸率最低要求為10%,在此基礎上追求高強度,以滿足碰撞鉚接的要求。
壓鑄鋁合金材料發展現狀:國内情況,國内壓鑄鋁合金絕大多數以A1-Si 合金為主,這類合金存在強度較低、切削性能不夠好、螺紋加工困難等現象,是以近年來大陸正在開發高強度合金。全球情況,壓鑄鋁合金如 EZCastTM 合金(C611, C60K, C448), Aural-2,Aural-4, A365 和 Mercalloy 目前被廣泛應用于車身結構件以減輕汽車重量。
免熱處理材料取得突破。其中 EZCASTTM 系列鋁合金由美國鋁業供應在上世紀九十年代開發乘用并應用于奧迪 A8 的全鋁車身上,其典型核心C611 被廣泛應用壓鑄的減震塔,EZCASTTM 免熱處理系列是帥翼馳與蔚來合作材料的選擇方向。國内外均有企業涉足免熱處理材料的開發,如立中集團、帥翼馳集團、華人運通與上海交大、特斯拉、美國美鋁、德國萊茵菲爾德等。
特斯拉解決方案:自研。2015 年特斯拉從蘋果挖來鋁合金專家Charles Kuehmann,其主要負責 Space X 和特斯拉的材料工程,特斯拉聲稱其新的鋁合金材料強度可以調整至90MPa 到 150Mpa,導電性可以達到 40% IACS 到 60% IACS。
技術難點二:模具壁壘
模具涉及到模具的設計、模具的耐用程度等方面,1)模具的耐用性會直接影響到成本,一體化壓鑄對模具的沖擊更大,對模具材料的選擇要求更高,在滿足鑄件要求的同時要考慮到模具的耐用性;2)模具設計更複雜,材料的配方也需配合模具使用,模具在壓鑄模具中複雜的充型、凝固過程是壓鑄的關鍵要素之一。
1)模具的耐用性:
一體化壓鑄的鎖模力更強,殘餘的應力會對模具造成損傷,壓鑄模的使用條件較為惡劣,在壓鑄過程中,金屬液進入模具型腔,受型腔内的空間限制,在型腔凹角處産生拉伸力;模具溫度受金屬液溫度的影響逐漸升高,模具受熱膨脹,模具表面産生壓應力;鑄件脫模後對模具進行冷處理,模具收縮,産生切向拉應力;壓鑄模承受模具内外各方互動應力的影響,可能會導緻模具出現裂紋,同時離型劑或者其他雜質依附在模具上等會産生積碳作用,影響後續産品的良品率,同時材料中的鋅積附在模具表面會産生粘模效用,對模具的使用壽命均會産生影響。
2)模具的形狀設計:
模具形狀設計有壁壘原因主要有三點:影響産品品質,鑄件斜度值設計不合理會引起抽芯,開模後進行取件時容易造成擦傷,且轉角處的圓滑程度等均會導緻氣孔的産生,壓鑄件還會因排氣不良産生、壓鑄參數不當造成卷氣、鋁合金的縮氣孔、産品壁厚差過大等原因産生氣孔;影響模具壽命,設計的不良會導緻鑄件壁厚不均勻,還會導緻模具中存在細薄的截面,還會反向導緻早期模具裂痕。一體化壓鑄的模具設計更難,更不易被填充,壓鑄件距離更遠,封閉的鳍片或凸起等形狀更不規則,更不容易被填充、模具的圓角不适宜或者合模時長不得當時等均會産生裂痕。
技術難點三:壓鑄過程控制
在整個壓鑄操作過程中的數十個參數控制,涉及到如加熱的溫度,模具的溫度,脫模劑的使用等環節,每個過程均與産品性能和良率息息相關。而由于一體化車身件大,鋁液填充模具時間長,時間越長壓鑄過程中的控制難度越大。
1)壓鑄機的駕馭能力。壓鑄的結構越複雜,對于拔模角、插破角、排氣孔、出模方式、收縮方向等結構參數的要求越高;對于液态金屬充填型腔速度、流态、壓射比壓、壓射速度等工藝參數的控制越嚴格。同時裝置的使用要與材料和模具等配合,壓鑄材料的充填速度也對良品率有影響,需根據壓鑄合金和鑄件結構特性确定。
2)模溫控制。分析模具的熱平衡,合理設計冷卻/加熱管道,是生産中對模具溫度進行有效控制的前提條件,模具的表面溫控對一體化壓鑄件的影響極大,如熔湯前段溫度低時,壓鑄件會産生冷紋;
3)員工經驗。随着震動和交變應力沖擊,壓鑄過程中産生裂紋的潛在可能性較大。同時,壓鑄過程中因為高速鋁液射流對模具的反向破壞很大,壓鑄之後的零件尺寸表面會呈現出極其複雜的形狀,對員工經驗、技術的要求上升。
此外,在裝置采購方面有資金壁壘及時間成本。一體化壓鑄的大型裝置的固定成本較高,在采購上有資金進入壁壘,且适用于規模效應的産品。一體化壓鑄對裝置鎖模力要求顯著提升,6000 噸以上大型壓鑄機供應偏緊,從裝置訂購到安裝調試完成時間至少需要 1 年時間,壓鑄廠商需要率先布局一體化。
4. 國産大型鋁壓鑄車身件龍頭,把握一體化産業趨勢
4.1. 大型鋁壓鑄車身件 10 年積澱,奠定更新基礎
一體化壓鑄是更大、內建度更高的車身件。車身件是一般為成再見或受力件,通常尺寸大、壁薄、具備良好的延伸率、既有較高的屈服強度和抗拉強度等特性,主要包括橫縱梁、A(B)柱、減震塔、保險杠、車門架構、車架連接配接件等。2011 年公司領先國内同行率先布局鋁壓鑄車身件,10 年車身件積澱使公司在鋁壓鑄車身件的模具、材料、壓鑄工藝上擁有雄厚的技術儲備和經驗積累,而一體化壓鑄是更大、內建度更高的車身件,是以 10 年大型車身件鋁壓鑄經驗奠定了公司更新一體化壓鑄基礎。
公司在鋁壓鑄車身件上擁有 10 年經驗,是公司做一體化壓鑄車身件的基礎。
鋁合金車身結構件由于對汽車起支撐、抗沖擊的作用,對強度、延伸率、可焊接性都有着極高要求,材料制備、壓鑄難度非常大,鋁車身此前主要應用于高端車型以上,國内幾乎沒有參與者,公司多年以來持續研發并提升高真空壓鑄技術、應用于高真空壓鑄的模具技術、特殊材料開發或制備技術及相關生産工藝技術,并且公司所開發和量産的鋁合金車身結構件系列是比較完整和全方位的,涉及的産品有車門架構、前後梁及側梁、前後減震塔、扭力架、A 柱、D 柱、電池盒殼體及支架等,先後為奔馳、特斯拉、蔚來、小鵬、廣汽 AION 等批量供應鋁合金車身結構件,在鋁壓鑄車身件上具有明顯的領先優勢。
公司真空高壓鑄造技術全球領先,且優于國内同行。
真空高壓鑄造生産的鋁合金結構件強度更高,品質更好,生産效率也更高,其技術難點在于對使用的壓鑄機噸位、及模具的複雜程度要求大幅提升。開發高真空壓鑄技術,生産高強度、高韌性的壓鑄件來取代鋼制結構是世界各國正向研發和推廣應用的技術路徑之一,國外企業在鋁車身結構件真空高壓壓鑄工藝上有超過二十年曆史,主要包括喬治費歇爾、皮爾博格、卡斯馬、尼瑪克四家鋁壓鑄廠。
國内目前有文燦股份、拓普集團、廣東鴻圖等企業生産鋁壓鑄車身件,文燦股份是國内最早研究及使用真空高壓鑄造工藝生産鋁合金的企業,是國内大規模量産鋁合金車身結構件的領先企業,産品基本覆寫全部鋁合金車身結構件。
公司至今已有 200 多個鋁合金車身結構件的量産項目經驗,公司的壓鑄件力學性能達到抗拉強度 315MPa,屈服強度 204MPa,斷後伸長率為8.5%,最小壁厚1.3mm,最大尺寸 1400mm×510mm×350mm,已實作大型、複雜、薄壁一體化與輕量化制造,在技術上公司領先國内同行 4-5 年的。
公司鋁壓鑄車身件主要配套傳統/新能源中高端車型。
奔馳:2014 年開始車身結構件量産供貨,公司給奔馳供應的鋁合金車身結構件主要是應用在燃油車上,包括奔馳 C、奔馳 E 以及 GLC 三款車型,2014 年開始供貨。
特斯拉:2014 年下半年獲得特斯拉定點,供貨特斯拉北美modelS/X兩款高端車型出口鋁壓鑄車身件,2015 年開始供貨。
蔚來:2016 年獲得蔚來汽車定點,給蔚來 ES8、ES6、EC6 供應16-18 件鋁壓鑄車身件,2018 年開始供貨。2022 年開始給蔚來 ET7、ES7、ET5 供應鋁壓鑄車身件。
小鵬 P7、廣汽 AION V:單車配套價值量相對較小,2020 年開始供貨。
4.2. 獲客進度超預期,一體化程序領先全行業
公司從 2020 年開始籌備一體化壓鑄,在材料、模具、壓鑄工藝、壓鑄裝置上均有優勢:
在模具上,公司設有模具公司,此前所有車身件的模具都是自主設計制造,是國内少數擁有大型和複雜模具自制能力的汽車鋁合金壓鑄企業。
在材料上,一體化壓鑄件件大(後座闆投影面積約1.5mX1.5m,重量約40kg),考慮形變問題無法進行熱處理,需要研發鋁合金免熱處理材料,材料涉及多個微量元素的配比,需要對大型鋁壓鑄車身件有較深的積澱和了解作為支撐,公司已和供應商共同研發出免熱處理鋁合金材料,公司掌握了全過程的配方和成分要求,材料具有排他性。
高真空壓鑄工藝上,公司采用高真空壓鑄技術生産車身結構件,該技術使型腔真空度可以做到 30 毫巴以下,更好地提升材料機械性能。
壓鑄裝置上,與力勁合作率先布局,2021 年 5 月公司與力勁科技簽約訂購7台套大型壓鑄單元,包括兩台 6000 噸、三台 4500 噸、一台3500 噸、一台2800噸,7 台壓鑄機均為力勁旗下意德拉 X-PRESS 系列兩闆式壓鑄機,其中1台6000噸壓鑄機已經交貨并安裝調試完畢,另外 1 台6000 噸壓鑄機将于22年2月傳遞。2021 年 8 公司又與力勁科技在宜興工廠舉行9000T 超級壓鑄單元簽約儀式,9000T 壓鑄機将于 22 年 2 月底完成傳遞,助力公司生産大型一體化車身結構件。
領先同行,斬獲訂單。國内新勢力車企紛紛布局一體化壓鑄工藝,考慮到一體化壓鑄前期投入較大、工藝壁壘較高,根據産業調研大部分主機廠選擇外放給專業的鋁壓鑄供應商來完成,而公司在鋁壓鑄車身件領域是國内絕對龍頭,已領先同行獲得新勢力一體化壓鑄訂單,我們認為公司憑借 10 年鋁壓鑄車身件積澱,在材料、模具和壓鑄工藝上均有領先優勢,在一體化壓鑄領域的獲客進度有望持續超預期。
4.3. 從車身到底盤、三電,全面擁抱新能源
除了一體化壓鑄之外,公司在三電、底盤領域也做了充分布局,斬獲多個新能源訂單。1)底盤件,獲得紅旗、比亞迪、吉利前後副車架訂單;2)電機殼體,獲得國産大衆 MEB 電機殼、蔚來電機殼訂單、比亞迪三合一訂單;3)電池盒/儲能箱體,獲得敏實集團電池盒結構件(終端供貨奔馳)、鋁壓鑄電池托盤和儲能箱體也獲得多個電池廠訂單。
三電:拓展電機殼體同時研發一體化電池殼/儲能箱體。
在電機殼體方面,2017 年公司通過收購方式獲得宜興工廠低壓資産,2020年并購百煉進一步延伸低壓工藝,根據客戶要求電機殼體可采用高壓、低壓工藝,公司實作電機殼體工藝全覆寫,2020 年公司對宜興工廠及生産裝置進行改擴建及更新,低壓鑄造及重力鑄造産能進一步提升,随着公司在手新能源電機殼體訂單放量,将逐漸釋放業績。
在電池托盤方面,電池托盤工藝或将從鋁型材擠壓焊接向壓鑄工藝轉型,公司已率先布局鋁壓鑄電池盒。擠壓工藝是目前電池托盤的主流路線,如寶馬、奧迪、沃爾沃、蔚來、小鵬等車企均采用擠壓技術,在加工工藝上,需要經過鋸切、杆件加工、闆件加工、攪拌摩擦、MIG 焊接、TIG 焊接、底盤加工、總成加工、氣密檢測等環節。與鋁型材擠壓焊接工藝相比,壓鑄工藝在成本、生産效率上均具有優勢,工藝路線有望轉型更新。受益儲能和新能源,在 2021 年公司獲得多個電池盒托盤/儲能箱體定點,根據客戶需求公司将采用高壓或低壓工藝來生産相關産品,同時公司也在布局一體化電池托盤。
底盤:鑄鋁副車架業務實作從無到有的突破
副車架可以阻隔振動和噪聲,鋁合金副車架提升操縱穩定性及懸挂系統連接配接剛度。汽車副車架用于連接配接懸架設定和車身,是底盤的結構件。在運動型轎車或高端車上,使用副車架可以減弱路面震動,同時減少路面噪音,提升NVH 水準。1)操縱感提升,使用普通沖壓鋼闆會增加額外重量,對于前驅車來說車頭增重會影響操控,造成堆頭現象;2)節約能耗,整車每減重 10%可降低油耗 10%-15%,單個鋼制副車架的重量為15~25kg,采用鋁合金材料制成的副車架,可以在原有基礎上減重40%,簧下品質每減輕1kg,帶來的效果等效于簧上品質減輕 5-10Kg,整車輕量化後,燃油經濟性和續航都能提升。
鋁合金副車架是汽車底盤輕量化的重要路徑。采用鋁副車架替代鋼制副車架可減重約 30-50%,有良好的輕量化效果,最早在歐洲市場應用于奔馳、奧迪、寶馬、英菲尼迪、讴歌等中高端品牌中。随着消費更新,鋁制副車架開始下探。根據鼎立産業研究網,2018年國内鋁副車架滲透率約為 2.2%,2018 年比亞迪唐、吉利博越GE 等車型搭載鋁副車架,實作了從合資到自主品牌的跨越,小鵬 P7、極氪 001(後副車架)、廣汽AionS/LX、蔚來 ES6/ES8 等新能源車型也使用了鋁合金副車架。随着新能源車的普及和輕量化的加速,鋁副車架的滲透率有望進一步提升。
公司鋁副車架業務拓展順利,新客戶訂單飽滿。2020 年公司将公司的産品類型從車身結構件擴充至底盤結構件領域,開發新客戶中信戴卡,研發生産兩款四個前、後副車架産品,終端客戶為一汽紅旗汽車兩款車。2021 年上半年,公司新獲得兩款後副車架項目,終端客戶為吉利和比亞迪,實作了向主流自主車企的突破。
5. 盈利預測
關鍵假設:
新能源三電帶來鋁壓鑄增量,同時底盤、車身鋁壓鑄滲透率提升共同拉動輕量化需求。按照《新能源汽車産業發展規劃(2021—2035 年)》,2025 年中國新能源汽車滲透率為 20%、2030 年 40%、2035 年 50%,汽車電動化帶來鋁壓鑄三電産品增量,公司在三電領域新增電機殼體、電池托盤(包含儲能箱體)、三合一殼體等産品,配套大衆MEB、比亞迪等多家新能源車企。另一方面,汽車電動化下輕量化需求較以前大幅提升,帶來底盤、車身鋁壓鑄滲透率的提升,公司鋁副車架、鋁壓鑄車身件訂單飽滿。
一體化壓鑄需求快速增長。特斯拉采用一體化壓鑄技術,起到降本、提效、擴産的作用,穩坐毛利率最高車企,引領了産業發展方向。各大車企紛紛加入一體化壓鑄大軍,小鵬、蔚來、大衆、沃爾沃、高合等車企紛紛展開一體化布局,行業正在掀起一體化壓鑄工藝革命,根據正文預測,2021~2025 年,一體化壓鑄的市場空間将快速提升至273億元,CAGR 達 134.5%。一體化壓鑄制造技術門檻較高,文燦股份此前在大型鋁壓鑄車身件上有 10 年積澱,是以具有絕對的領先優勢,且已獲得多個重大訂單,我們認為公司有望成為一體化壓鑄龍頭。
業績預測:
汽車壓鑄業務:是公司業務主體,占比超過 90%,2021 年增速較快主要是新增百煉集團并表,2020 年 8 月公司收購法國百煉集團并于 8 月開始納入合并報表。2022-2023年,百煉集團保持穩健增長,文燦本部貢獻主要增量,增量來源于:鋁壓鑄車身件,2022年開始蔚來新車型、理想、牛創等新項目投産;車身一體化,行業爆發初期,越來越多的車企會加速應用該工藝,公司一體化壓鑄訂單将從 2022 年下半年開始逐漸投産放量;底盤件、三電殼體、電池托盤/儲能箱體三大類産品在手新能源訂單飽滿。綜上,預計2021~2023 年公司汽車鋁壓鑄件營收為 39/53/67 億元,同比增長61%/35%/28%。在盈利性方面,2021 年由于缺芯、鋁價大幅上漲、海外疫情反複、運費等外部多重沖擊,公司盈利能力承壓,2022 年随着鋁價從高位回落、公司業務結構的優化(毛利率較高的新能源項目放量)以及規模效應的釋放,公司毛利率水準将得以明顯改善。
其他業務:公司模具業務主要用于自用,預計 2021~2023 年營收占比較為穩定,非汽車壓鑄件業務非公司業務主體,波動較小。
(本文僅供參考,不代表我們的任何投資建議。如需使用相關資訊,請參閱報告原文。)
精選報告來源:【未來智庫】。