1. Judgment on the position, length and depth of the weld seam of the hot blast furnace shell:
First through ultrasonic testing, determine the location, length and depth of each weld crack source, and punch a stop hole of about Φ10 mm at the end of the crack source at 10 to 20 mm, if the crack length is long, the crack can be treated in segments.
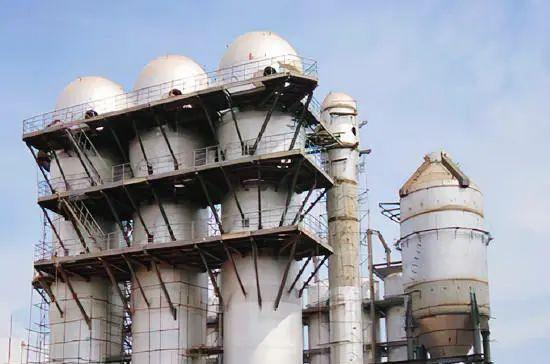
Blast furnace hot blast furnace shell surface crack repair treatment process measures
2. Use the hot blast furnace air stop time for repair operation:
The specific construction time is negotiated with the hot blast furnace operation unit of the blast furnace company, and the construction time is fully utilized to ensure that each weld is treated properly.
3. Section the roots with carbon arc gouging:
Cracks must be cleared, if the micro-crack is found to develop in the direction of thickness, the micro-crack can be melted by using the depth of penetration of the welding rod first, and then the root is cleared, otherwise even if there is no crack during welding, the crack may continue to develop later.
4. Clean the grooves on the surface of the groove with carbon arc gouging:
Clean the end of the stop hole, the groove is smooth transition, no obvious grooves, and then grind with a polishing machine, the surface is colored or ultrasonic flaw detection, and the next step can be carried out after checking for no crack defects.
5. Crack cracking to the root of the base metal for treatment:
Considering that welding can only be carried out on the outside of the hot blast furnace, the base material at the weld can be cleaned to the root with carbon arc gas planer or gas welding tool, and the welding pad with a thickness of 3mm or a round steel with a diameter of 12mm is added to the root before welding (the two steels must match the base material), so as to facilitate the construction of welding and ensure the quality of the welding seam.
6. Preheat before welding the shell weld:
The welding is first preheated by gas welding, and the preheating temperature is in the range of 100 ~ 150 °C.
7. Welding rod drying treatment:
Dry at 350°C~400°C for 1~2 hours before use, reduce to 100°C~150°C for insulation. When welding, use a thermos cylinder to pack, take as you go.
8. Crack welding process of hot blast furnace shell:
The first three layers are welded using manual arc welding, which requires narrow weld beads, thin welding layers, small weld bead width, and welding layer thickness of not more than 5mm. The remaining layers can be welded using carbon dioxide gas bracing welding, using a multi-layer multi-channel welding process.
9. Precautions for crack welding of hot blast furnace shell:
(1) When welding, use cloth strips around to ensure the quality of welding.
(2) In addition to the bottom weld, each layer of welds should be hammered to eliminate stress and then carry out the next layer of construction.
(3) The interlayer temperature during the entire welding process shall not be lower than the preheating temperature and shall not be higher than 400 °C.
10. Hot blast furnace weld surface heat treatment:
After the weld surface is colored or ultrasonically tested, the local flame heat treatment is started, and the local flame baking is carried out with two plates of cutting guns, the recommended temperature is 600 ~ 640 ° C, and the heat preservation is kept for 2 hours after cooling.
After local heat treatment, the weld is 100% ultrasonic flaw detection, reaching gb11345-89I. qualified, the weld surface is 100% colored inspection, crack defects are not allowed, and heat treatment is carried out within 12 hours.