Hang Xiaobei's daily popular science/literature
Some friends who are familiar with military equipment must know that there is a phenomenon called "rotor-to-rotor" in the aircraft engine, which means that in the design, the aircraft engine will make the high-pressure rotor and the low-pressure rotor rotate in opposite directions. In the first tweet on February 7th, we also discussed it specifically, and interested friends can flip through it. In the article, Xiaobian pointed out that the rotor is not to cancel the turbine front import guide. However, due to space limitations, Xiaobian did not explain two issues:
What are the benefits of high and low pressure rotor pair rotation in addition to weight loss?
Since the high and low pressure rotor pairing makes it possible to eliminate the front import guide of the turbine, why are so few people doing it?
Today, let's talk about them one by one.
Benefits of high and low pressure rotors
In addition to the ability to eliminate low-pressure turbo head guides to reduce weight, high- and low-pressure rotor contraversions in general have two significant benefits.
Benefit 1: Controls the gyro moment effect of the rotor
The so-called gyroscopic torque effect is that when the object rotates at high speed, it will have an inertia in the direction of pointing, and if you want to change the spatial direction of the object, you will definitely be subjected to the reaction force from the rotating object.
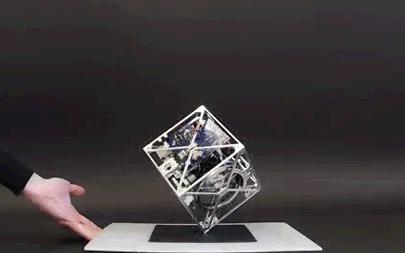
↑The direction of objects moving at high speeds in space will remain the same ↑
That is to say, when the aircraft does maneuvering flight, it will force the rapidly rotating rotors in the engine to change the direction in space, so that the aircraft is subjected to a certain reaction torque. On the one hand, this torque affects the maneuverability of the aircraft, but more importantly, these additional torques are very unfavorable to the strength of such parts as the engine-aircraft connection. So when you see the plane doing maneuvering flight, you can imagine the engine stubbornly resisting the turn of the plane and causing adverse effects.
↑Airplanes are doing maneuver flight ↑
Through the opposite rotation of the two rotors, the gyroscopic torque generated by the rotor can cancel each other out, thereby reducing the adverse effect of the gyro torque effect on the engine and the aircraft to a certain extent, which is the first benefit of the rotor contraversion.
Benefit 2: Optimizes the vibration of the rotor
What really makes aero engines more and more inclined to use rotor-to-rotor design is actually this second benefit: that is, from the dynamic point of view, the vibration problem of the rotor is alleviated as much as possible.
The so-called rotor vibration, that is, when the rotor speed is close to some specific speed, a phenomenon called "resonance" will occur, so that the engine must stop working, otherwise it will cause irreversible damage and damage to the engine.
↑Resonance of the engine rotor ↑
If there is only one rotor, then the vibration problem of the rotor is relatively easy to solve, but when the high and low pressure rotors work together in the small space of the engine, they are mutually influential, which means that the vibration of the two rotors is definitely not as simple as 1 + 1 = 2, but far more complex than the vibration of one rotor.
Compared with the same direction of rotation, when the two rotors rotate in reverse, the working point of the rotor can be further away from the resonance point. The principle of influence is very complex, but you can show you an intuitive result.
In the following figure, the horizontal coordinate is the low-pressure rotor speed, and the ordinate is the high-pressure rotor speed, so the left half is the case where the speed of the high and low pressure rotors is opposite (relative rotation), and the right half is the case where the speed of the high and low pressure rotors is the same (same direction rotation). In the normal working state of the rotor, the corresponding high and low pressure speed point is in the gray area, and those colored lines are lines that must not be touched. Obviously, when the high and low pressure rotors rotate, the safety area is larger, which also means that the engine is more stable.
↑Effect of rotor-to-rotation on resonant speed distribution↑
Therefore, the above two reasons are the benefits of the relative rotation of the high and low pressure rotors, far from the benefit of "the low-pressure turbine import guide can be cancelled".
What is the cost of eliminating low-pressure turbine import guides?
Although the cancellation of the low-pressure turbine import guide is not the only benefit of the high and low pressure rotor rotation, it is also a benefit after all, why not cancel it? In fact, the reason for this is also very simple: because it is too difficult to cancel the low-pressure turbine import guide!
High-pressure turbine blades are not long
We know that in the compressor, the air flow is compressed to less and less volume, and in the turbine, the air flow is more and more expanding and larger, which is why we generally see the aircraft engine is "small waist", because the air flow volume in front of the combustion chamber is getting smaller and smaller, and after the combustion chamber, the air flow volume is getting larger and larger. This trend is reflected in the length of the blades, which means that the later in the turbine, the larger the length of the blades.
↑Turbine part blades will get longer and longer↑
When there were originally imported guide blades, there could also be a first-stage static blade transition, so the length of the high-pressure turbine blades could be designed to be shorter, but if you want to cancel the imported guide blades, the first big problem is that the high-pressure turbine blades have to be done very long.
Let's take the F136 engine and the F110 engine as an example, of which the F136 engine does not have a low-pressure turbine import guide blade, while the F110 still retains this structure, the ratio of the low-pressure turbine blade length and the high-pressure turbine blade length of the F136 engine is 2.1, and the F110 is 1.25.
You know, the high-pressure turbine speed is extremely high, the temperature is extremely high, it can be said that the entire engine load is the worst position, if the high-pressure turbine blade is lengthened, it is undoubtedly very unfavorable to the strength life of the blade, and more advanced materials and design technology are needed to be able to hold this design. So, even if it is as powerful as the United States, it has not completely solved this problem so far.
What about inter-turbine cooling and sealing?
In addition, the low-pressure turbine import guide blades do more than just adjust the direction of the air flow. In fact, there is also a large lump structure under this part, which is mainly used for cooling and sealing, on the one hand, to ensure that the temperature of the turbine disk is not too high, on the other hand, to prevent the high-pressure gas from running between the high and low pressure turbines.
↑Cooling and sealing structure under the inlet guide of the low-pressure turbine of the F119 engine↑
If the import guide is removed, where are these cooling and sealing structures placed? Is it possible to let these weights rotate at high speed with the rotor? So if you don't solve this problem, just ignore the three seven twenty-one, don't do low-pressure turbine import guide, can not achieve the function of the engine at all, which is also one of the reasons why not cancel the turbine front import guide.
To sum up
The main benefit of the high and low pressure rotor to rotor is to significantly improve the rotor gyro torque effect and rotor vibration characteristics, and without canceling the low-pressure turbine import guide, the original high and low pressure rotor that rotates in the same direction is changed to relative rotation, which is actually not difficult.
If you want to cancel the guide between the high and low pressure rotors, you will face the two serious problems of too long high pressure turbine blades and no place to place cooling/sealing between turbine stages, there is not enough materials, design technology, it is difficult to solve, even the United States today can not do to remove these adverse effects.
That's why there are a lot of aero engines that rotate in rotors right now, but the number of aero engines that remove the turbine front import guide blades is almost zero.