Common failures of petrochemical centrifugal pumps
1. Mechanical seal failure
In the actual operation of petrochemical centrifugal pumps, one of the common failures is the failure of mechanical seals, and the causes of such problems are the failure of dynamic and static rings and sealing rings. Sealing the spindle, the need to play the role of centrifugal pump auxiliary system, once the actual operation of the unit has a fault problem, it is necessary to carry out comprehensive and effective sealing treatment from the external performance and nature characteristics of the fault, and control the pressure and temperature after sealing. However, in actual operation, the failure of the sealing pipeline system will directly affect the normal use of the centrifugal pump.
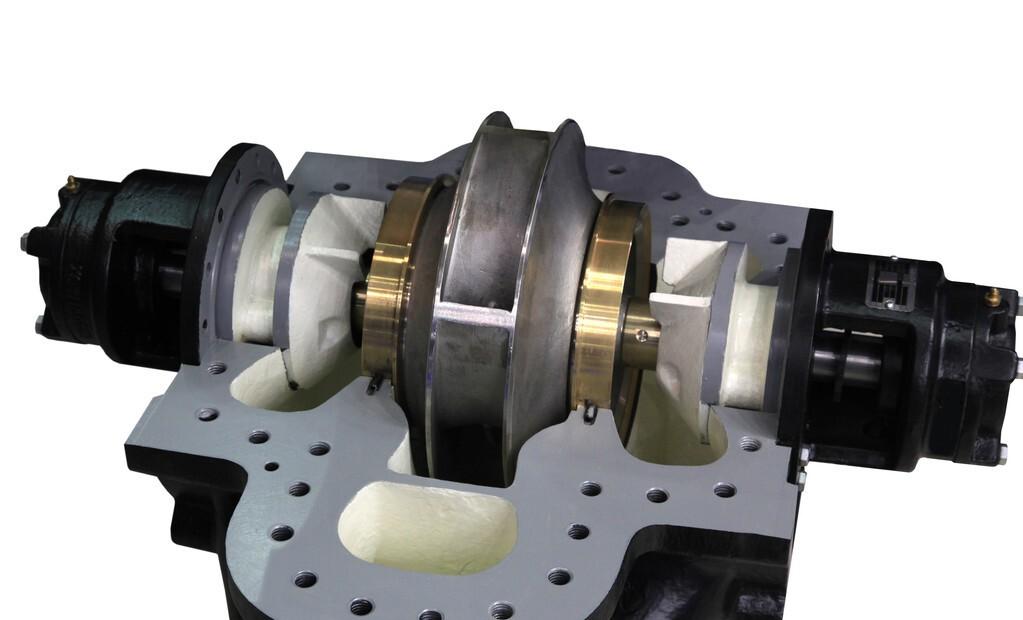
Centrifugal pump (image from the network)
2. Abnormal sound or severe vibration
Centrifugal pumps are mostly operating in a state of changing working conditions, and the phenomenon of small flow conditions is more obvious, and this situation will lead to more unstable flow conditions within it, which is generally manifested as reflux, flow separation and rotational stall. Correspondingly, in the small flow condition, it will also lead to increased dynamic and static interference in the application of centrifugal pumps, and eventually vibration and hydraulic noise will occur, which is not conducive to the safety and stability of the entire pump system operation.
The overall overhaul and maintenance of the petrochemical centrifugal pump
1. Maintenance of centrifugal pump
1.1 Preventive and predictive maintenance
In the development process of the petrochemical industry, the use of centrifugal pumps as an important production support requires full awareness of the overall operation of centrifugal pumps and a full range of maintenance and maintenance work. First, preventive maintenance work. Starting from the predetermined time node, carrying out meticulous on-site maintenance work, full maintenance and overhaul for various operating equipment, and timely repair and replacement of centrifugal pumps will effectively reduce the probability of major safety accidents. The use of preventive maintenance and maintenance work methods requires the need to rely on personnel with strong professionalism and rich maintenance experience. Second, carry out predictive maintenance and maintenance work. This kind of maintenance work requires the actual operation of the centrifugal pump as the most basic consideration, and the subsequent maintenance and maintenance are carried out according to the specific test results. Predictive maintenance work, mainly for the centrifugal pump bearing parts of the detailed inspection, including temperature, abnormal sound, lubrication and severe vibration and other aspects of abnormal situations, the specific maintenance of the data obtained and the original centrifugal pump set by the technical parameters for a detailed comparison, timely discover the existence of the abnormal situation, so as to carry out the processing work. Maintenance personnel in the process of performing predictive maintenance work tasks, need to choose a certain time node parameters, to see whether it reaches or exceeds the predetermined critical value, if there is such a phenomenon, the need to stop maintenance, reduce the occurrence of unnecessary losses.
1.2 Proactive maintenance and maintenance work
Starting from the foundation of preventive and predictive maintenance work, we actively carry out all-round maintenance work to reduce the occurrence of some undesirable situations. It is not only necessary to observe the occurrence of fault problems, but also to actively find the root cause of such problems, so as to carry out in-depth and thorough maintenance and maintenance work, which is the content and goal of active maintenance and maintenance. In the application of this maintenance method, it is necessary to be able to accurately find the cause of the failure, and use this as an important basis to carry out the treatment work to solve the various risk factors for the occurrence of the fault, so as to promote the centrifugal pump to maintain normal operation. In the process of maintenance and maintenance, it is also necessary to actively rectify some defects of the centrifugal pump, and if necessary, it can be redesigned.
2 Centrifugal pump specific fault maintenance work
2.1 Overhaul of mechanical seal failure
The problem of seal failure of machinery will directly affect the normal operation of centrifugal pumps to a large extent, resulting in its inability to provide support for the smooth development of petrochemical production. Effective analysis and maintenance of mechanical seal failures requires attention to combining the causes of their failures. First of all, if the maintenance result is that the sealing ring fails, it is necessary to replace the sealing ring in the medium and high temperature medium in time, and the use of materials with high heat resistance such as fluoroelastomer will be able to play a good effect; Seals in low temperature environments can also be replaced with materials with higher cold resistance. Second, the problem of elastic element failure. The scaling problem inside the elastic element requires a full range of flushing work, and the effect of using the oil sealing treatment method is more obvious. If the component failure is caused by soldering treatment, it needs to be replaced in time, using some more corrosion-resistant and high-temperature resistant materials. In addition, the treatment of dynamic and static ring failure problems can be effectively improved by using sealant inorganic adhesive, and it is also enough to improve the material of the ring seat and effectively control the interference amount, so as to carry out troubleshooting work and improve its overall application effect [1].
Othello mechanical seals
2.2 Maintenance of abnormal sound and severe vibration problems
Centrifugal pumps usually maintain normal operating conditions, if there is an abnormal vibration situation during the maintenance process, or there is a noise phenomenon, it indicates that there is an operational failure, and it is necessary to use scientific and reasonable ways and means to deal with and deal with it in time. Stop the operation of the centrifugal pump in time, check the balance of the impeller, and observe whether the pump shaft and motor shaft of the centrifugal pump are in the specified unified state. Check the causes of abnormal problems in centrifugal pumps one by one, and then replace and adjust the operating components of centrifugal pumps to ensure their stable operation.
Conclusion
In the actual operation of the petrochemical centrifugal pump, it will be affected by a variety of factors, some faults and problems, the need for comprehensive and meticulous analysis and research on these failures, to find a practical and effective way to deal with and respond, timely improvement and replacement of some components and even centrifugal pumps, to ensure that it is always in a safe and reliable operating state. Carrying out a full range of maintenance and maintenance work can provide an important premise for strengthening the operation effect of centrifugal pumps.
bibliography
[1] Fu Shuxia, Sun Tie, Yi Huiqin, et al. Research and Application of Rotor Dynamic Balancing Technology for Centrifugal Pumps in Petrochemical Plants[J]. Chemical Machinery, 2014, 41(01): 110-113
The above content comes from the Internet, such as invasion and deletion!
Related Reading:
Centrifugal pump shaft end seals in several forms and their characteristics
Centrifugal pump mechanical seal design problems and solutions
Cantilever centrifugal pump shaft end seal modification
OTHELLO mechanical seals are suitable for dynamic sealing of rotating shafts, and the performance is relatively reliable, with little leakage and low power consumption under normal circumstances. Widely used in high and low temperature, high pressure, high speed of clean water, corrosive media, particle-containing media and other working conditions. Visit the official website: Industrial sealing import brand - Othello Sealing Materials (China) Co., Ltd