Application of lubricants in plastic extrusion products (2)
The lubricating effect of a single lubricant is often limited. When selecting lubricant varieties, we must give full play to the coordinated role of lubricants. Due to the use of paraffin or calcium stearate alone, increasing the dosage will increase the plasticization temperature or reduce the plasticization torque. The combination of the two is more obvious. When the total dosage is 2 mass parts, paraffin / calcium stearate is the strongest when the ratio of paraffin / calcium stearate is the strongest, and when the same amount is used, the extruder load can be reduced, and good mechanical properties of the product can be obtained. Calcium stearate (barium) has a similar effect, the total dosage is unchanged, and the proportion of calcium stearate (barium) increases, which will increase the plasticization speed and plasticization degree. Calcium stearate is a low-quality internal lubricant and a heat stabilizer in the middle and late stages. When the dosage is 1 part, it does not affect the lubrication balance of the beginning, middle and late stages, and lead stearate has participated in the heat stabilization effect when pvc is just heated and shear force, and begins to generate stearic acid, playing the role of internal lubricant.
Structurally, oxidized polyethylene wax contains a small number of polar groups and paraffin wax does not contain polar groups, so paraffin wax is less dispersible between pvc resins than oxidized polyethylene wax. This should be the main reason why the initial external lubrication effect of paraffin wax is stronger than that of oxidized polyethylene wax. The melting point of oxidized polyethylene wax is much higher than that of paraffin wax, so it has a stronger effect in the late extrusion stage and can give the product a higher brightness.
Will have a similar chemical structure of low melting point and high melting point lubricants, can play two roles, first of all, the melting point change, when the temperature rises, low melting point lubricant first melted, due to the similar structure, will penetrate or dissolve into the high melting point lubricant molecules is the so-called similar compatibility, weaken the intermolecular force, reduce the melting point, promote melting, and even form a multi-component confort, so that the boundary lubrication temperature zone is widened. For example, after combining 65 °C paraffin wax and calcium stearate, the melting point of calcium stearate can be reduced to 105 °C. In addition, low melting point lubricants generally have lower viscosity at higher temperatures, easy to generate interfacial lubrication film, but at higher melt pressure, the interfacial shear effect is enhanced, this low viscosity interfacial lubrication film is easy to be destroyed, high melting point lubrication has a tacking effect on low melting point lubricants, so that the interfacial lubrication film can still remain good under high shear action.
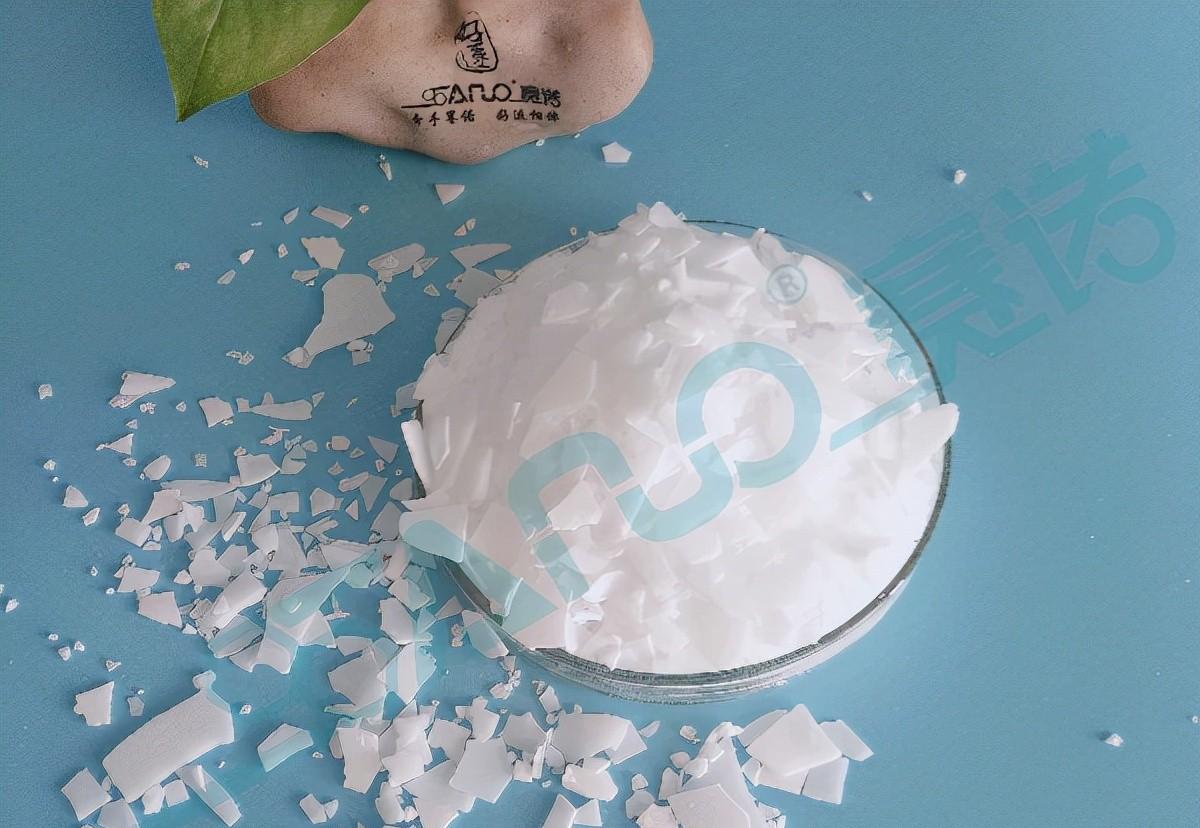
Polyethylene wax (Sainuo)
Because pvc is a polar polymer, the polar group in the lubricant molecule, such as hydroxyl, alkenin, ester group and other polarity and content determines its compatibility with PVC, the closer the polarity is to polyvinyl chloride, the better the compatibility with polyvinyl chloride, the stronger the internal lubrication effect, on the contrary, when the compatibility between the lubricant and pvc is poor, it will migrate to the surface and play the role of interface lubrication. There are two aspects to the difference in the compatibility of lubricants with pvc, on the one hand, the molecules are non-polar, such as hydroxyl, silicone oxygen, Androxy, Buddha-containing resin, the lower the polarity, the stronger the external lubrication, and some compounds can even be used as mold release agents. On the other hand, the molecule contains a polar group, and when such lubricants migrate to the surface, the polar group can have a better physical or chemical interaction with the metal. When polar and non-polar lubricants are used together, a multi-molecular layer interface lubrication film can be formed, and in this lubricating film, they each play a different role, the general polarity lubricant molecular polar group has a better role with the metal surface and PVC particles, and the non-polar lubricant molecules are between the polar lubricant non-polar groups, and a composite polylayer interface lubricating film is formed on the surface of the polyvinyl chloride particles and metals, which has a better and more reliable lubrication effect. Can give full play to their respective advantages, is conducive to the formation of interface lubrication state, improve the lubrication effect, reduce the amount of lubricant, reduce costs.
When changing the variety or dose of calcium carbonate in extrusion production, special attention should be paid to the activation treatment of calcium carbonate. General calcium carbonate is based on stearic acid, stearate or stearate monoglyceride as a surface treatment agent, the type of surface treatment agent, dosage, treatment quality is good, will directly affect the choice of extrusion product lubrication system. Stearic acid is more important than external slip, and monoglyceride stearate is biased over internal slip, so the basic situation of calcium carbonate should be mastered when determining the lubrication system, so as not to cause excessive or insufficient lubrication.
With the increase of cpE dose in the formula, the material plasticization time will be significantly shortened, and it is necessary to add an appropriate amount of external lubricant and minimize the dose of wax lubricant, because paraffin wax is easily soluble in CPE modifier, which will not only reduce the lubrication effect, but also affect the low temperature impact performance of the product. Add calcium stearate with balanced plasticization in an appropriate amount to ensure that the PVC resin is suitable for plasticization time.
In the selection of lubricants should pay special attention to pvc resin fluidity, different grades or different manufacturers of the same grade of resin due to different molecular weight, the fluidity varies greatly, the size of the fluidity will affect the material plasticization process, the amount of lubricant required for large fluidity resin is smaller than the fluidity of small resin.
Sainuo New Material, 15 years of accumulation, polyethylene wax brand manufacturer, Blue Ocean equity institution listed enterprises. Focus on the research and development and production of lubrication and dispersion systems, including polyethylene wax, oxidized polyethylene wax, polypropylene wax, EBS, zinc stearate and other additives research and development, production and application work. Hotline: 400-8788532.