Although the screw is small in size, and the role is not small, and the scope of application is also very extensive, but for the use of screws many manufacturers still pay more attention, of which surface treatment technology makes us the most common way to improve the performance and quality of screws, the following in order to let everyone better understand the surface treatment technology of screws made a summary.
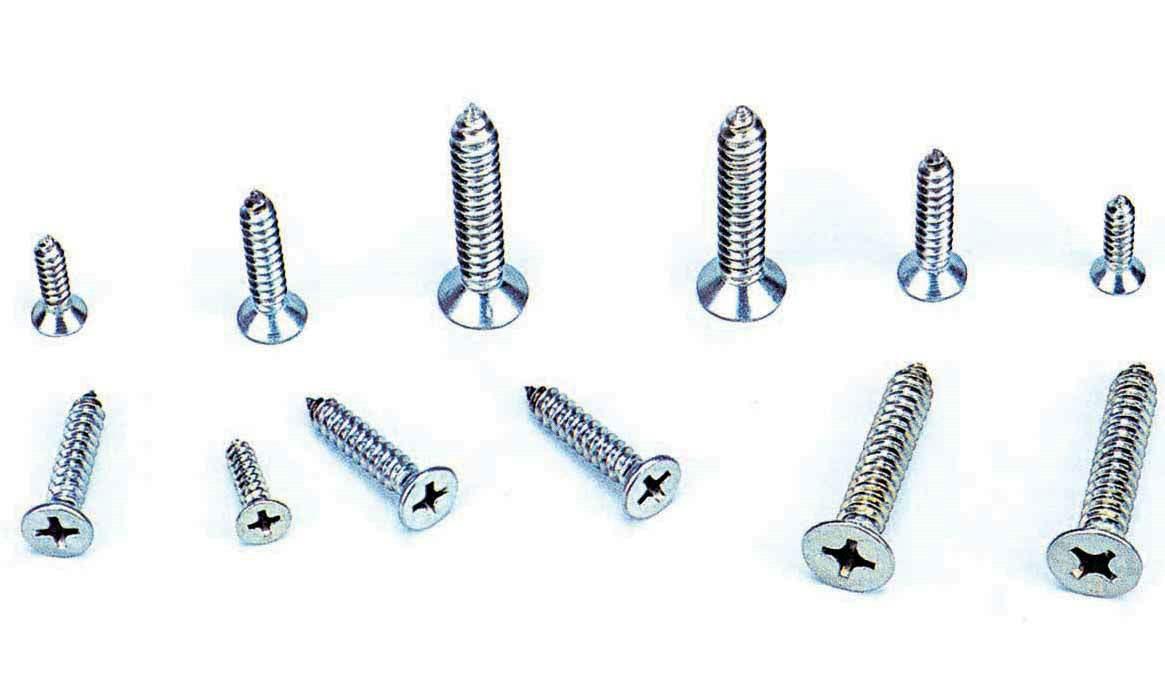
<h5>Source: China Standard Parts Network</h5>
1. Electroplating
The part receiving the plating is immersed in an aqueous solution containing the metal compound to be deposited, and an electric current is passed through the plating solution, so that the electroplated metal precipitates and deposits on the part. General electroplating has galvanizing, copper, nickel, chromium, copper-nickel alloys, etc., and sometimes boiled black (blue), phosphating, etc. are also included.
2. Mechanical galvanizing
Particles coated with metal are used to impact the surface of the product and the coating is cold welded to the surface of the product. Generally, the screws are mostly plated, but they are hot-dip galvanized for outdoor hexagonal wooden screws such as electricity and highways; The cost of electroplating is generally 0.6-0.8 yuan per kilogram, and the hot-dip zinc is generally 1.5-2 yuan / kg, which is a higher cost. The effect of electroplating: The quality of electroplating is mainly measured by its corrosion resistance, followed by appearance. Corrosion resistance is to imitate the working environment of the product, set as test conditions, and test it for corrosion testing.
3. Alloy catalysis
The product can be processed by heating to about 83 ° C at room temperature. During the processing, the metal is generally soaked for about 15-20 minutes, and after soaking, it is washed with clean water and dried naturally. Sealed at room temperature and pressure for up to 3-5 years without deterioration. In extreme environments such as high temperature and high pressure, the catalytic products still have high anti-corrosion, wear resistance and other characteristics.
It is understood that the electroplating treatment of screws is prone to hydrogen embrittlement problems. During processing and processing, especially in pickling and alkali washing before plating and during subsequent plating, hydrogen atoms are absorbed on the surface, and the deposited metal plating then captures hydrogen. When the fasteners are tightened, the hydrogen is turned toward the stress*-concentrated part, causing the pressure to increase to exceed the strength of the matrix metal and produce tiny surface cracks. Hydrogen is particularly active and quickly seeps into newly formed fissures. This pressure-rupture-infiltration cycle continues until the fastener breaks. On the contrary, the catalytic treatment of screws will not occur in the above undesirable phenomena. The alloy of the screw catalyzes the formation of a new alloy layer on the metal surface, which enhances the performance of the screw surface. It is worth mentioning that the alloy catalytic fluid is recycled and repeatedly added. Its green environmental protection characteristics are also unsurpassed and achieved by electroplating technology.