Positioning
Not long ago, when the president inspected huawei mobile phone factory in Songshan Lake in March, he delivered a speech entitled "Our purpose is to achieve high", which mentioned that "we must use all the world's most advanced production equipment, the most advanced tools and methods, and excellent people to aim for high quality"; obviously, Mr. Ren knows that the manufacturing capacity of mobile phone factories is one of the core competitiveness of Huawei's mobile phones to dominate the world, and high-quality manufacturing and delivery is the core of all specialized production activities, and there is no high-quality delivery of results. The design of Re-Niu B, the high-end brand, the large scale, the good equipment and technology... Will not be able to establish a high-strength stickiness with users, to catch up with Apple to dominate the world is even more so.
Vice versa, manufacturing quality management is not moving forward in isolation, but is also based on the specific development of manufacturability, replicability, and deliverability of supporting products.
Professional manufacturing plants roughly have three types of OEM, ODM, EMS, because the quality management of the R&D end and the supply chain side has a separate module description, the following is to discuss the OEM foundry as the scenario.
Objectives
After sharing the "" in the previous edition, an old leader of the technical department left a message asking: "What is the quantitative assessment index for quality management?" ", I feel that it is necessary to clarify the key objectives of manufacturing quality this time, so as not to be "inquired" again.
<col>
stage
index
Rating method (except for reasons that are not directly caused by production or uncontrollable in production)
After delivery
Customer complaint (from/quarter)
It can be divided into general customer complaints and major customer lawsuits
DOA (Dead On Arrival, Out of The Box Failure Rate)
DOA = (Number of unpacking failures in this batch at a project point / Total number of deliveries in this batch) * 100%
FFR (Field Failure Rate)
Also known as site failure efficiency, that is, the proportion of product failures in the warranty period to the insured amount
QFC (Quality Failure Cost)
(Total expenses incurred due to quality repairs, claims, penalties, etc.) *100%
The above is the customer-oriented, should measure the delivery quality performance of the assessment, but to achieve good indicators is not easy, it is necessary to break down the quality objectives item by item, stage by stage, department by department, according to the annual / quarterly / monthly measurement assessment, and the major / batch quality events that occur in the process in a timely manner to start the quality traceability mechanism, clear responsible person, take appropriate penalties, and promote the overall quality performance of the manufacturing system (including engineering, production, warehouse, procurement, planning, maintenance, etc.); and the measurement of quality objectives is established and implemented. Multi-department collaboration from finance, marketing, after-sales, HR is required.
Act
In the manufacturing plant, lean production is not only an important management tool, but also an important part of the factory culture, its core includes zero defects, zero inventory, zero waste, high efficiency, requiring support for multiple varieties, small batches. Manufacturing quality management should be promoted in synergy with lean production management, constituting a complementary and mutual promotion relationship, and improving the granularity of factory, standardized and flexible management.
The production process and quality control points of conventional factories mainly revolve around the following three stages:
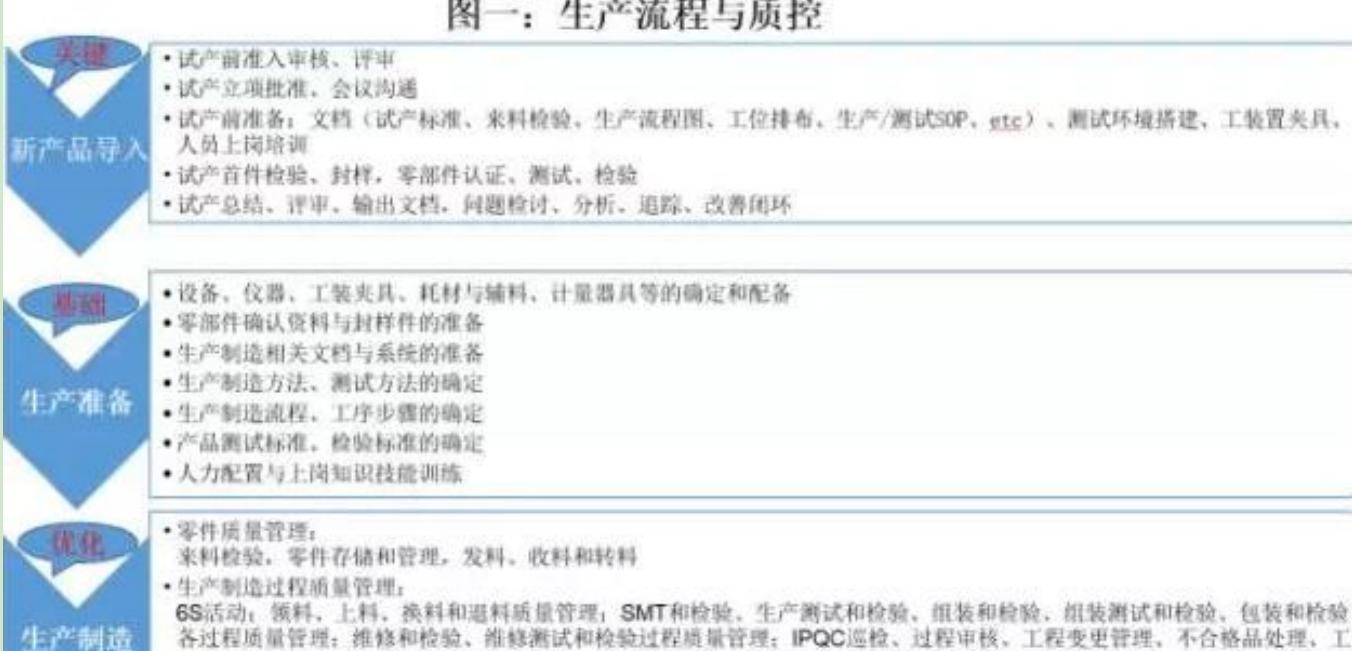
The key to the construction of the system framework of the manufacturing quality management system is to have a closed-loop effect, with reference as follows:
Preventive measures module expanded:
Process Control Module Expansion:
Continuous Improvement Module Expanded:
The internal organization and manpower setup to support the work of the manufacturing quality management system are roughly divided into the following three modules:
Typically, the main responsibilities of a manufacturing quality management team are briefly defined as follows:
1. Establish, integrate and implement the required systems
(ISO&ISO&TS&QC08000&&3C, etc.), and guide and audit to ensure that each element (including organization, specification, process, testing, etc.) operates effectively in the whole process of manufacturing.
2. Introduce and promote factory quality culture, advanced quality tools, compile factory quality training materials, and improve the quality awareness of all employees.
3. Quality planning, control, analysis and improvement in the process of product manufacturing, the implementation of on-site early warning control, while ensuring the quality of product production, improve the overall production plant work quality performance.
4. Through the collection, classification and analysis of quality data (poor inspection, abnormal production, landing maintenance, customer complaints), clarify the main or serious responsible party (raw materials & manufacturing process & design, etc.), take necessary quality improvement actions, avoid the continuous spread and recurrence of quality problems, and continuously improve the level of product design and manufacturing.
5. Maintain full communication with internal and external customers, enhance satisfaction, and quickly respond to customer complaints about quality problems with measures to solve and re-issue correction prevention.
In the process of exercising duties and obligations, the following considerations need to be adhered to are:
1. The spirit of craftsmanship and the spirit of quality are in the unremitting pursuit of product and process perfection, so quality personnel should take this as the source of faith in production site management, ensure that all details are rationalized and controlled, and make it standardized, process-oriented, templated, and then optimized in an orderly manner.
2. In the new product introduction stage, on the one hand, the quality should participate in the project feasibility review, on the other hand, it is also necessary to do a good job in the in-depth analysis of customer needs (product standards, process standards, delivery standards, after-sales standards); in the process of project initiation and trial production, the design of the customer or the design of the designated raw material manufacturers and other issues should be timely feedback, and promote the customer to make improvements or commitments; the adaptability of the internal process capabilities should be given an objective and sufficient review, and the existing deficiencies must be improved before the mass production is introduced. For those who for some reason cannot be completely closed at this stage, it is necessary to assess the risk and give a risk control mechanism.
3. In the QC process of quality inspection, whether it is full inspection, fixed point, tightening, sampling inspection, exemption from inspection, inspection, inspection, or resident inspection (only for suppliers), it can be flexibly set based on the maturity of the production process and product, allowing appropriate cutting, or at the appropriate time to transform its functions into the production department's independent management and implementation.
4. The system of the factory increases with the growth of product diversity and customer diversity, the introduction and implementation of various systems will increase the burden of enterprise operation, the emergence of unclear standards, and lengthen the decision-making process of enterprises, so the integration of diversity systems is crucial to ensure that the company's operating system is relatively smooth, concise, authoritative and efficient.
5. The quality management of materials and semi-finished products and finished products in the inventory or turnover link cannot be ignored, including storage control, validity period control, mixing risk, etc., it is necessary to agree with the asset ownership management department on inventory and use rules, take the initiative to send for inspection, and take timely measures to isolate and solve in abnormal cases to avoid flowing into the production process.
6. In on-site management, "man, machine, material, law, ring, measurement, time" are the possible factors affecting production, but people are the primary factors affecting most problems, and the analysis and improvement of the problem also depend on human behavior, so in addition to the necessary quality engineering knowledge, quality management personnel should also be good at communication and coordination, try to avoid tension and antagonism with production, engineering and other departments due to work differences, be good at unity and empathy, from the perspective of helping them improve and enhance the quality of work, For example, the lack of R & D design to overcome the trouble of production, the potential defects of raw materials to the product reliability and production interception of the trouble; only learn to stand in their point of view, work together to think and improve the results of work, will be respected and recognized, so that the concept of quality can be deeply rooted in the hearts of the people.
7. Change confirmation is an important control link of quality control, such as design changes, material changes, process changes, supplier changes, key personnel changes, test methods and environmental changes, etc., the initiation of changes is explicit, there are also invisible and unclear, as a professional quality personnel must adhere to the process and principles, the compliance of the change and the risks that may be brought by the full assessment, the unknown changes must be supported by objective test results, rather than based on experience to make decisions After the change is passed, all decision-making process documents are also retained for future customer calls or retrospectives.
8. In product manufacturing, the analysis and prediction of potential failure modes and the failure analysis ability of sudden failures are the capabilities that quality engineers need to have and strengthen, and the independent analysis level and ability training are the swords for the department to carry out in-depth product quality work.
9. Product or material test development, to customer demand as the starting and ending point, in addition to the technical components driven, to be good at customer needs as the end point, through the mind map, the customer needs structured, decomposed and refined to each device, each station, test cases to comprehensive customer demand changes, product maturity, production maturity for appropriate increase and decrease, continuous adaptation, self-matching, and finally simulated user experience test is also crucial.
10. In the management rules of special collection and change, there should be a quota mechanism, and include quality measurement, implement assessment of results, avoid random initiation of special collection and change, and advocate the work concept of doing things right at one time.
11. Quality management personnel should be good at identifying, identifying, retaining, classifying, sorting, sharing and promoting effective knowledge, and guide other relevant production, engineering, warehousing, procurement, planning and other departments in the factory to participate in the joint construction, in order to continuously improve the maturity of factory manufacturing management; knowledge management should be based on IT informatization.
12. Manufacturing quality managers should pay attention to building a good relationship of high-quality collaboration with customer quality managers, especially in design optimization and improvement of customer supply material problems, to maintain a high degree of collaboration and information sharing, and jointly promote and ensure product quality to achieve the expected goals.
13. The construction and improvement of quality culture in the implementation of many companies, easy to slogan, formal, to implement, to build effective value, in addition to the need for the senior managers of the factory to pay attention to and actively lead, but also need all quality managers to use wisdom, personal practice of long-term persistence to promote, with a positive attitude coaching through the use of quality tools and concepts to bring their own value satisfaction.
14. The above internal organizational structure, positioning, and responsibilities should not be used in general, and the use should be scenario-based (industry/development stage/management maturity...), the most important thing is to keep the principle and maintain a good cognitive and evolutionary posture for a long time.
Think
On May 19, 2015, the "Made in China 2025" development outline issued by Premier Li Keqiang heralded the opening of the era of intelligent manufacturing, compared with Germany's "Industry 4.0" and the United States' "Industrial Internet of Things", although everyone's goals are the same, but the stages and advantages and disadvantages of each of them and the entrance to the force are not the same, we in China are still in the concurrent stage of industry 2.0 ~ 3.0, and Germany has entered the tandem stage of 3.0 →4.0.
In the currently recognized intelligent manufacturing knowledge system, the path trend of its evolution and development is roughly as follows:
The basis of its integration of industrialization and informatization is manifested in three aspects:
Its characteristics may be mainly reflected in three aspects:
1. The hardware foundation is highly interconnected, including production equipment, industrial robots, production turnover support tools, production test fixtures, operators, materials, whole machine products, etc.
2. The manufacturing process data is real-time, the production data under the end-to-end system has a smooth beat and arrival flow, and the storage, analysis and calculation of the data are also real-time.
3. The development and application analysis of big data in the manufacturing industry, supplemented by machine self-learning functions and algorithms, feeds back to improve and optimize the manufacturing process flow, and enhances the end-to-end evolution ability.
In the iterative upgrading of intelligent manufacturing, how to maintain awareness and action of quality manager practitioners, keep up with the development and change of future enterprises and technologies, from followers to guides, is the need for continuous awakening and persistence to go further, the following points are based on personal cognition at this stage can imagine the entrance and possible actions:
· In the field of traditional industrial manufacturing, the focus of quality management is on-site management, the key object is people, and the follow-up should increase the attention to data and algorithm management in the field and people's attention, and gradually constitute an enhanced virtual reality intervention capability;
· Promote R&D and supply chain to inject ID into each material, module, semi-finished product and finished product, form digitalization and informatization, and improve the whole life cycle identification, traceability, supervision, maintenance, analysis and modeling of products.
· Data management platform construction: identification, storage, exploration, predictive modeling, visualization of all hot and cold data, especially the quality data related to process and product implementation, integrated into data quality management, pay attention to collaboration with engineering and software department personnel;
· Simulation testing: Mimicking the physical world based on enough real-time data, conducting augmented virtual reality testing, continuous testing and optimization of products and equipment debugging, especially in the new product introduction phase.
· Equipment and equipment, equipment and materials, materials and finished products, people and equipment, equipment and industrial software (ERP, MES, etc.) ... How to define the interface mode of the connection, business functions and process mechanisms, etc., are all defined and developed by the factory planner (similar to the role of product manager) and the software personnel, and the expected goals here are achieved? Is the logic reasonable? Quality personnel should proactively intervene in requirements analysis and process reviews and validate them through appropriate node testing to ensure availability, stability, reliability, and ultimately customer satisfaction improvements throughout the system.
· Manufacturing management business platform integration and construction: on the basis of quality materials, intelligent products, industrial robots, industrial software (ERP, SCM, MES, PDM, CRM...), industrial big data, industrial broadband, leveraging cloud storage (private cloud or hybrid cloud), cloud computing, data management platform, designed to enable end-to-end intelligent manufacturing business platform.
· Mobile user-side support: It can be a mobile phone & PAD APP, or wearable device interaction software and other tools to realize the timely interaction, response, execution, change and decision-making of the tasks of the intelligent manufacturing factory and the cloud platform and the working population.
· In the system architecture and operation and maintenance, the ISMS information security management system should also be established and improved to prevent the occurrence of risk problems that endanger the operation and reputation of enterprises such as virus damage, hacker attacks, loss of important information and data, and paralysis of information systems.
No matter what the future holds, dare to establish a cognitive system early, and then feel the stones to cross the river, will always be closer to the other shore, let our minds and behaviors walk on the road!
Remarks: The article originated from the Internet, please contact to delete.