This is the 14695th article published by Metalworking (mw1950PUB).
Editor's Note
Injection molding is a mature process, with the continuous segmentation of the market, customer quality requirements to improve, plastic types are also increasing, prompting injection molding technology to continue to innovate, injection molding workshop management, injection molding quality also put forward higher requirements.
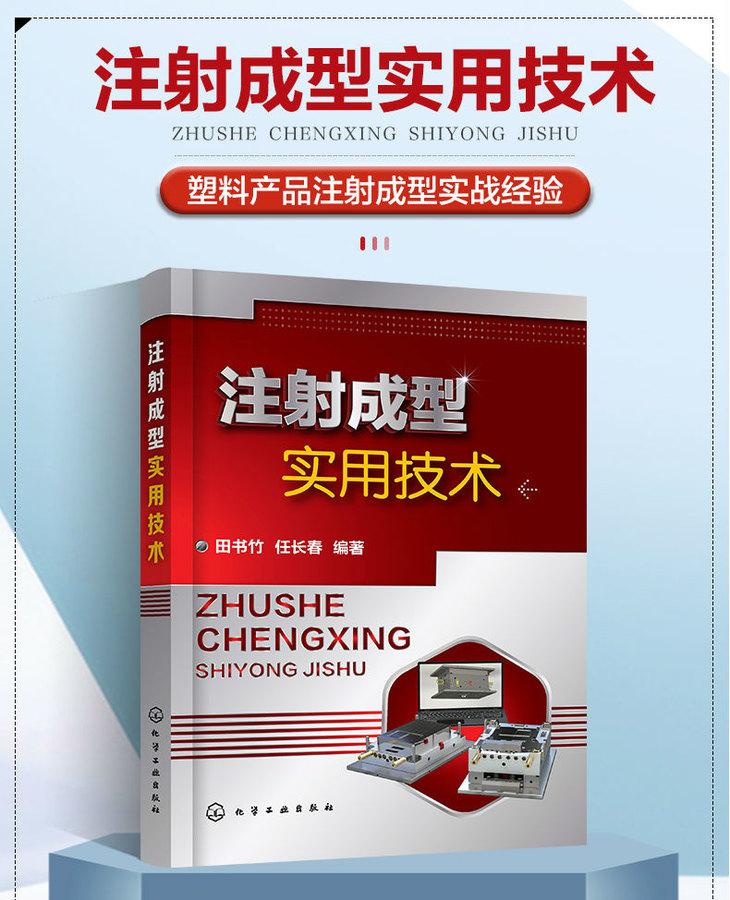
"Injection Molding Practical Technology" is mainly based on the author's many years of first-line production experience, the injection molding related technology and common and difficult problems encountered in the actual work are systematically summarized and elaborated, and the basic knowledge of injection molding materials and the problems that should be paid attention to in production are explained in detail, the structure of the injection molding machine, the setting of the process parameters of the injection molding machine, the trial mold operation and technical points, the conversion of different machine trial parameters, the common defects and improvements of plastic products, the post-process technology of plastic products, the analysis and prevention of injection mold failures, Maintenance and maintenance of injection molding machines and molds, injection workshop management, injection molded parts quality management, plastic product design and quotation.
This book is suitable for plastic product design, mold design, injection molding related design and production personnel reference, but also as a learning material for students of materials and molds related majors in colleges and universities.
Drag the scroll bar on the right to view the entire catalog
▼
directory
Chapter 1 Injection Molding Material Basics 001
1.1 Definition and classification of plastics 001
1.2 Basic properties of plastics 003
1.3 Advantages and disadvantages of plastics 007
1.4 Plastic additive 008
1.5 Plastic combustion difference method 011
1.6 Estimated time that plastics need to cool after injection 012
1.7 Plastic product self-tapping screw experience point 013
1.8 Plastic product tolerance class 013
1.9 plastic flame retardant grade 015
1.10 Plastic aging and anti-aging 015
1.11 Effect of internal stress on the properties of plastic products 016
1.12 Plastic product identification 016
1.13 Transparent plastic injection molding production should pay attention to the problem 017
Chapter 2 Injection Molding Mechanism Manufacturing and Selection 019
2.1 Classification of injection molding machine 021
2.2 The basic structure of the injection molding machine 022
2.2.1 Injection part 023
2.2.2 Clamping part 031
2.2.3 Hydraulic system 032
2.3 Select injection molding machine 034
2.3.1 Selection of injection volume of injection molding machine 035
2.3.2 Selection of clamping force of injection molding machine 037
2.3.3 Selection of mold size of injection molding machine 037
2.3.4 Selection of injection speed 038
2.3.5 Selection of mold opening stroke of injection molding machine 038
2.3.6 Selection of mold volume of injection molding machine 039
Chapter 3 Setting of Injection Molding Machine Process Parameters 040
3.1 Set the process parameters of the opening and closing mold 040
3.1.1 Setting of clamping process parameters 040
3.1.2 Setting of mold opening process parameters 042
3.2 The action parameters of the injection table are set to 043
3.3 Pressure setting 043
3.3.1 Setting of injection pressure 044
3.3.2 Setting of packing pressure 044
3.3.3 Setting of back pressure pressure 045
3.3.4 Setting of ejection pressure 045
3.4 Speed setting 046
3.4.1 Setting of injection speed 046
3.4.2 Setting of melting speed 047
3.4.3Set of ejection speed 047
3.4.4 Set the speed of the opening and closing die 047
3.5 Setting of position 048
3.5.1 Setting of the injection position 048
3.5.2 Setting of the packing position 049
3.5.3 Setting of the ejection position 049
3.5.4 Set 050 for the opening position
3.6 Time setting 050
3.6.1 Set the injection time 051
3.6.2 Cooldown period setting 051
3.6.3 Setting of the packing time 051
3.6.4 Set the opening and closing die time 051
3.6.5 Setting of melting time 052
3.6.6 Set of drying time 052
3.7 Setting of temperature 052
3.7.1 Setting of material temperature 053
3.7.2 Set the mold temperature 054
3.8 Setting of the injection cycle 054
3.8.1 Injection cycle component analysis and setting 054
3.8.2 Shortest injection cycle analysis 058
3.8.3 Thin-walled injection cycle analysis 058
3.8.4 Double pump injection cycle analysis 059
3.8.5 Injection Cycle Case Study 060
3.9 Injection Molding Process Parameters - Curve Case Study 060
Chapter 4 Tryout 064
4.1 Mold trial process 064
4.1.1 Preparation before the mold 064
4.1.2 Upper mold operation 069
4.1.3 Down mold operation 071
4.2 Quick mold change 072
4.2.1Preparation before mold change 072
4.2.2 Mold change process and method 073
4.3 Elements of the mold trial process 078
4.3.1 DOE Mold Trial Verification Method 078
4.3.2 Determination of the optimal temperature 079
4.3.3 Determination of optimal injection pressure 082
4.3.4 Determination of optimal packing pressure and time 083
4.3.5 Determination of the optimal cooldown time 084
4.3.6 Determination of the optimal injection speed 085
4.3.7 Determination of the optimal clamping force 086
4.4 Collection and summary of mold trial records 087
4.5 Technical requirements for tryout 091
4.5.1 Purpose of tryout 091
4.5.2 Condition 091 that the test mold engineer should have
Chapter 5: Conversion of Tryout Parameters Between Different Injection Molding Machines 092
5.1 Overview 092
5.2 Conversion theory background of different injection molding machines 093
5.3 Copy of clamping force and temperature 096
5.4 Replication of cooling and packing time 097
5.5 Back pressure and speed copy 097
Replication of 5.6V-P location 098
5.7 Copy of fill speed 098
5.8 Replication of the injection position 098
Chapter 6 Common Defects and Improvements in Injection Molded Products101
6.1 Insufficient filling (lack of material, short shot) 101
6.2 Product weight instability 102
6.3 Deformation 103
6.4 Product inner hole eccentricity 105
6.5 Discoloration, yellowing 106
6.6 Gas pattern 107
6.7 The thimble position is uneven 107
6.8 Burn 108
6.9 Black dot, black line 109
6.10 Gate residue 110
6.11 Pull White 111
6.12 Water Ripple 112
6.13 Scratches 113
6.14 Chromatic aberration 113
6.15 Poor surface gloss 114
6.16 Jet 115
6.17 Product collapse 116
6.18 Poor size 117
6.19 Material flower (silver grain) 118
6.20 Bubble 119
6.21 Flying Edge (Cape) 121
6.22 Shrinkage 122
6.23 Weld wire 123
Chapter 7 Auxiliary Equipment for Injection Molding Machines 125
7.1 Dryer 125
7.2 Dehumidification dryer 126
7.3 Mixer 128
7.4 Mold temperature control machine 129
7.5 Manipulator 132
7.6 Centralized feeding system 133
7.7 Plastic crusher 135
7.8 Mold waterway cleaning machine 136
Chapter 8 Mold Failure Analysis and Preventive Measures138
8.1 Thimble burn (broken) 138
8.2 Oblique top burn (broken) 138
8.3 Slider burns 139
8.4 Guide column/guide sleeve wear (broken) 139
8.5 Molding pin break 140
8.6 Muscles/Osteotrophic 140
8.7 Mainstream road adhesive die 141
8.8 Mold temperature is not good 141
8.9 Mold parting surface crushing 142
8.10 Mirror mold "flower" 142
8.11 Product side strain (drag) 143
8.12 Mold rust 143
8.13 Mold produces flashing edge (cape) 144
8.14 The mold waterway is not accessible 144
8.15 Exhaust chute anomaly 145
8.16 Mold can not open mold 145
8.17 Mold misalignment 146
8.18 Mold crack 146
Chapter 9 Injection Molding Machine Maintenance and Maintenance and Mould Maintenance147
9.1 Injection molding machine maintenance and maintenance147
9.1.1 Maintenance of the hydraulic system147
9.1.2 Maintenance of the electrical part148
9.1.3 Maintenance of mechanical parts148
9.1.4 Daily spot inspection and maintenance 150
9.1.5 Monthly maintenance153
9.1.6 Annual maintenance153
9.1.7 Injection molding machine common failure analysis 154
9.2 Mold maintenance 155
9.2.1 The importance of mold maintenance155
9.2.2 Mold maintenance specification 159
9.2.3 Mold in the machine maintenance operation method 160
9.2.4 Three-stage maintenance of the mold 162
9.2.5 Mold appearance maintenance points 167
9.2.6 Design and establishment of mold archives170
Chapter 10 Injection Molding Shop Management 171
10.1 Management of the ingredient room171
10.1.1 Management of raw materials172
10.1.2 Management of toner173
10.2 Management of the crushing room173
10.2.1Management of feed174
10.2.2 Control measures for the return of injection molding machines174
10.3 On-site management of injection molding workshops174
10.3.1 Team leader on-site management 175
10.3.2Management of tools, excipients178
10.3.3Management of upper and lower module tools178
10.3.4 Quantitative management of injection molding production178
10.3.5Programming and documentation management of injection molding production179
10.3.6 Injection molding department management personnel inspection work content 179
10.4Use and management of injection molds180
10.5 Injection molding workshop safety production management 180
10.6 Injection molding production cost management183
10.7The main reference table 188 related to production in the injection molding sector
Chapter 11 Injection Quality Management196
11.1 Basic knowledge of product quality196
11.1.1 Definition of product quality196
11.1.2Product standards and requirements197
11.2 Plastic product appearance testing 197
11.2.1 Plastic product appearance grade division 197
11.2.2 Measurement conditions and environmental requirements198
11.2.3 Plastic product testing standard 198
11.2.4 The main detection tool for plastic products 200
11.3 Test Project 201
11.3.1 Adhesion Test 201
11.3.2 RCA paper tape wear test 202
11.3.3 Alcohol friction test 202
11.3.4 Rubber friction test 203
11.3.5 Pencil hardness test 203
11.3.6 Cryogenic storage 203
11.3.7 High temperature storage 204
11.3.8 Salt spray test 204
11.3.9 Impact resistance test 204
11.4Process inspection management204
11.4.1Product inspection control205
11.4.2The main work content and precautions of process inspection205
11.5 Shipment inspection management 206
11.5.1 The main work content of shipment inspection 206
11.5.2Precautions for shipment inspection work206
Chapter 12 Plastic Products Quotation 207
12.1 Quotation of plastic products 207
12.1.1 Calculation of the weight of plastic products208
12.1.2 Unit price estimate of the price of various raw materials 208
12.1.3Exigentation of material costs209
12.1.4Exignment of costs during the injection molding process209
12.1.5 Estimation of the reprocessing price210
12.1.6 Estimation of the packaging price of the product211
12.1.7 Product quotation case study 211
12.2 Relationship between product, mold and molding212
12.2.1 Relationship between plastic product design and injection molding213
12.2.2The relationship between mold design and injection molding production214
12.2.3 Injection molding process and mold design218
Reference 220