Introduction: There is no inventory in March, and the data is wrong for one year
1. Inventory procedure
Inventory purpose: to explore the company's assets and operations, to provide reference data for performance appraisal.
Counting time: Small markets are counted once a month, and large markets are counted quarterly.
Inventory format: sudden disk, root disk, draw plate, unified inventory, and outgoing audit inventory.
1. Preparation before inventory
1) The front desk staff sorts out the counter goods, and fills in the relevant vouchers for the short, crippled and damaged goods before the inventory. Submit for approval and do accounting processing. Inventory shall not use IOUs or white stripes to replace the red-letter accounting.
2) The warehouse should promptly clean up and count the goods borrowed before the inventory, the advertising display goods, the return to the factory to repair the goods should be recovered in time, and the out-of-stock bills at the counter and the commodity department should be written off and recorded in time.
3) For the goods on the shelves, organize them before inventory, and clean up the loose warehouse goods to prepare for centralized inventory.
4) The storeroom commodity custodian should be cleaned up and checked before the inventory, so that the three positions of the account card are unified.
5) Before the inventory, each department should clean up the accounts in time, and pay attention to the consistency of the rented accounts, account tickets and account certificates during the inventory.
6) Bulk commodities can be pre-counted, sporadic commodities can be bundled with points, and goods that must be measured or weighed can be counted in advance, and the original number can be checked during the formal inventory, and the inventory form can be filled out after verification. Before the warehouse inventory, the consignment goods should be filled in separately into the inventory table.
7) Before the inventory, the goods should be reconciled with the cashier to ensure that the counter inventory is accurate.
8) Before the inventory, the relevant departments should reasonably arrange the shift to ensure the smooth progress of the inventory.
9) When taking stock, an inventory of two people filled in the form by one person should be taken, and the inventory should be carried out in the order of goods from left to right, and the inventory should be accurate.
10) The inventory of each department should be consistent with the actual accounts, the amount of the long and short amount should be filled in the inventory result report form according to the facts, and the sales volume and the amount of errors and the reasons for the errors should be merged from the previous period to the current period, and the names of the personnel who signed the inventory should be signed and reported to the competent department step by step.
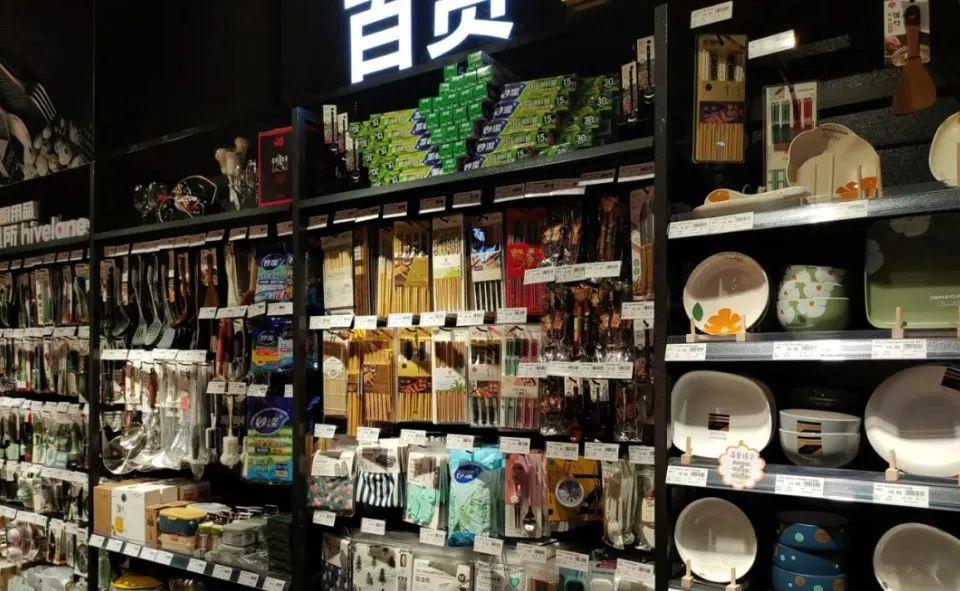
2. Inventory of the front cabinet group of the commodity department
1) Prepare for inventory
2) The Financial Information Department prints the inventory form and distributes it to each commodity department.
3) Double inventory in the commodity department.
3. Generate an inventory report form
Accurately reflect the business conditions and commodity management and loss status, find out the bottom of the family, fill in the gaps, and strengthen management.
Second, the inventory preparation stage
1. For the long, short and damaged goods that have occurred before the inventory, the relevant vouchers should be filled in in separately in accordance with the provisions and reported for approval and relevant accounting treatment, and the white bar and IOU should not be used to replace the inventory of the goods or the red character offset during the inventory.
2. The goods lent before the inventory should be cleared and checked out in time, carefully counted, displayed goods, repaired goods in a timely manner, and the customer has paid but the goods for pick-up are not included in the inventory.
3. The goods inside the counter, on the shelves, warehouses, high-rises and other goods should be sorted out before inventory, and the loose warehouse goods under the shelves should be cleared to prepare for centralized inventory.
4. Before the inventory, each department should clean up the accounts in a timely manner, and make sure that the accounts are consistent and the accounts are consistent.
5. When taking stock, one person takes one person to count the points, one person to review and fill in the form, layer by layer from left to right, from top to bottom, according to the order of goods, verification, mutual review or interspersed review, to prevent wrong disks, missing disks. The completion of the inventory form must be signed by both persons.
6. Clean up and find negative inventory goods, and the negative inventory goods are adjusted before the inventory, which shall not affect the inventory work.
Third, the inventory method
1. The entire supermarket disk point department sub-shelves (counter), plus high-rise, loose warehouse, etc. for inventory, the computer room generates the department inventory table, each department first provides the goods provided by the "Pre-Order Table", the product name is inventoried, and the bar code, price, the initial order by the staff of the commodity department, and then the sampling team draws the plate, after the end of the sampling verification, the commodity department completes the transfer to the "Inventory Table" work.
2. The department stores' self-operated goods are distributed according to the commodity storage area and sorted and inventoried.
The details are as follows:
1. Supermarkets uniquely code the goods of the entire supermarket according to the area code, number and department, and form a unique regional control number, which is marked on the "Pre-plate Table". Area control number = area code + number + department number.
Area Code: A sequence number arranged in the order of shelves or heads. The details are as follows: 01, shelf 02, counter 03, pile head 04, bulk warehouse 05, plus high-rise.
Numbering: The positions divided within the area are uniformly coded in order, which is convenient for the first order personnel to find.
Department number: and the department number in the computer system (Note: it is used when the inventory department archives and the product is transcribed, and the inventory can verify whether the goods on the pre-order table are the same department. )
2. The entire supermarket is sorted out by region and department, and the requirements are sorted out:
1) Unified goods are only allowed to be placed in the same position in the same control area.
2) All jointly operated goods in supermarkets cannot be mixed with self-operated or consignment goods, and inventory products should be separated from unallocated goods.
3) Scattered warehouse area: all commodities are classified by department, and all commodities are neatly stacked. Inventory items should be separated from uncounted items.
4) Add a high layer: sort out the goods in the pile area and keep them neatly stacked. And all the unpackaged goods in the pile head area are displayed on the shelves.
5) Pile head area: Sort out the goods in the pile head area and keep them neatly stacked. And all empty boxes used to stack goods in the head area are changed to solid boxes.
6) End head and normal shelf area: The goods are placed regularly and the product name is turned outward.
3. Inventory sequence: starting from the control number, generally from left to right from top to bottom, or starting with the inventory according to the commodity number indicated in the inventory table.
4, scattered warehouse, plus high-rise daytime first disk, end shelf and pile head, normal shelf inventory at night.
5. After the completion of the loose warehouse and the high-rise disk, the seal should be affixed, and no one shall release or pick up the goods like them during the inventory.
Fourth, the process description
1. The computer room generates a two-way inventory table.
2. The commodity department receives the inventory table, and disperses the warehouse, adds high-rise and shelves for preliminary order and summary.
3. After the various departments are summarized, they will be verified and signed on the inventory form.
4. Draw the plate by the lottery personnel and sign to confirm.
5. According to the verified inventory table, enter the microcomputer to generate a profit and loss statement.
6. The commodity department looks for the reason according to the income statement.
7. After confirming the amount of profit and loss, it is transferred to finance without accounting treatment.
5. Inventory requirements
1. The inventory personnel need to be serious, careful and patient to ensure accuracy.
2. Count of points, fill in the form accurately, font specification, handwriting neat.
3. The unit of measurement must be correct, clear and clear.
4. The inventory needs to be reviewed by two people to eliminate wrong disks, missing disks and duplicate disks.
5. The proportion of drawn plates shall not be lower than the prescribed proportion. The prescribed proportions are shown in the table below:
The proportion of product classification draws
Valuable goods (unit value of more than 500 yuan) 100%
Department Store: 100% of clothing, shoes and hats
80% of high-end cosmetics, alcohol, and other high-value goods (unit value of 100 yuan or more)
Other products (self-operated small products) 80%
6. Provisions on the handling of inventory errors
All personnel related to the inventory work will be fined according to the regulations and notified of criticism within the company due to sloppy work, illegal operation and other reasons.
Number of mistakes Fine Amount (RMB) Remarks:
3 times a click (including 2 times) 50 to find out the cause of the mistake, investigate the relevant responsible person
4 times - 6 times (including) 80 to find out the cause of the mistake, investigate the relevant responsible persons
7 times - 10 times (including) 100 to find out the cause of the mistake, and investigate the relevant responsible persons
11 times (including) more than 150 to find out the cause of the mistake, investigate the relevant responsible persons
Handling procedures: the inventory entry team summarizes the list of persons who have made a mistake in the inventory and transfers it to the Supervision Department; The Ministry of Supervision shall issue a notice of fines according to the penalty standard; The fine is paid in three copies, one copy by the Supervision Department, one copy by the Finance Department, and one copy by the Fined Person.
7. Take stock of the loss and bear it
Losses that exceed the proportion of profit and loss of the inventory shall be handled in accordance with the relevant regulations of the company.
8. Personnel arrangements
The selection personnel are deployed by the human resources department.
9. Explanation of important matters
1. Inventory day, night ** point closed, drawers gather at ** place.
2. Each commodity department takes a manual pre-order table, the first plate, the first market is handed over to the relevant drawing personnel to draw the plate, after the completion of the sampling, the commodity department personnel to the machine to do the meter reading work, all the inventory tables can also be sent to the financial bill office before the **.
3. During the inventory, the Department of Safety and Security is responsible for safety; The Supervision Department and the Administrative Management Department are responsible for taking stock of the personnel's meals; The Network Technology Department is responsible for technical support.
Attached note: The inventory work should be institutionalized and proceduralized, and the competent leader should take the lead, and the specific planning of the property management center of the Ministry of Finance should be implemented. Warehouses, buyers, front desk, store salesmen specific implementation, participate in the inventory. First of all, according to the prescribed time, do a good job of preparation before the inventory, inventory and registration in accordance with the prescribed order when the inventory is good, and fill in the "Commodity Inventory Schedule". After the signing of the manager of each department, it is submitted to the head of the property management center of the finance department for review, and the inspection is carried out in the form of review, sampling, etc., and the problem is found to be returned to the report. No problems should be reported to the manager of the finance department for signature review, and after signing and approval, report to the company's supervisor manager for approval. After approval, transfer to the financial non-accounting center for account adjustment and reconciliation; The transfer property management center conducts inventory analysis, clarifies the responsibility for disk loss, and puts forward suggestions for improvement.