introduction
Looking back at the development process of the anti-corrosion system of the main cable of the suspension bridge in China, it can be roughly divided into three stages:
(1) Before 2000, the design and construction of China's suspension bridge is still in the exploratory stage, the main cable anti-corrosion mainly refers to the way commonly used in Europe and the United States, that is, before the main cable is entangled, the main cable wire is filled with red dandelion or zinc putty, the putty mainly plays a role in passivating or cathodic protection of the main cable wire, and then the surface of the main cable is wrapped to constrain the main cable and provide a relatively flat surface for painting, and finally the sealing and bridge landscape needs to be painted on the surface of the wire.
(2) Around 2000, the domestic research institute proposed a patented main cable sealant coating system (hereinafter referred to as the sealant system), the system to non-vulcanization corrosion resistance sealing paste + winding wire + vulcanizing sealant + topcoat as the main supporting program, after the successful application of Shantou Bay Bridge, Xiling Yangtze River Bridge and other projects, in 2007 rose to the Ministry of Communications recommended standard "suspension bridge main cable system anti-corrosion coating technical conditions" standard number: JT/T 694-2007, in the next ten years, The main cable anti-corrosion system occupies the absolute position of China's main cable anti-corrosion system.
(3) In 2015, with the completion and opening of the Guizhou Qingshuihe Bridge, the first project in China to use the domestic wrapping belt sealing system (later known as the wrapping belt system), which opened up a new situation in the application of the domestic main cable wrapping belt, the current main cable wrapping tape anti-corrosion system scheme has blossomed everywhere, and the sealing agent anti-corrosion scheme accounts for half of the country, and it is expected that these two anti-corrosion schemes will coexist in the future for a long time.
This paper focuses on analyzing and comparing the advantages and disadvantages of the two schemes, and puts forward a little suggestion for the maintenance of the main cable system of the built suspension bridge.
1. Sealant system
First of all, to introduce the sealant system, the typical structural form of the winding section of the main cable sealant coating system is shown in Figure 1 below:
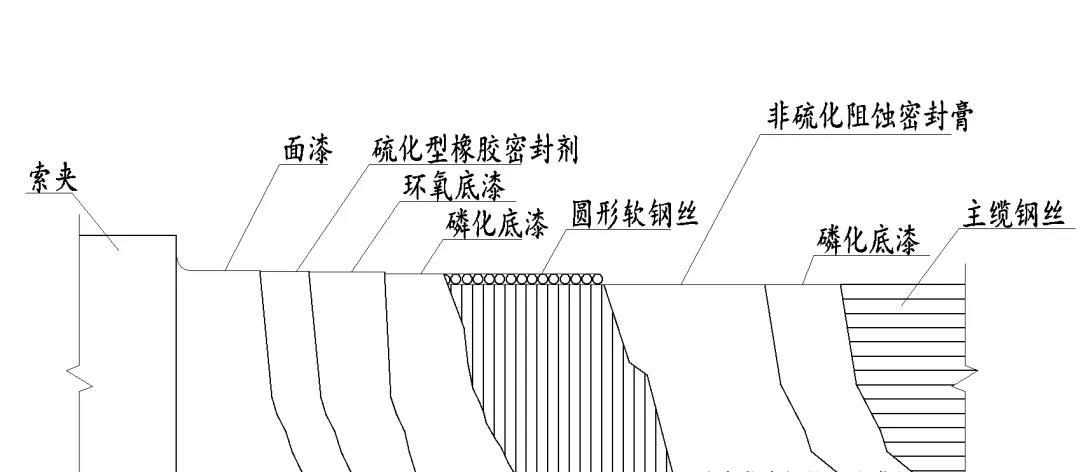
Sealant system main cable protection structure diagram
(1) First of all, the main cable high strength galvanized steel wire for primer coating, the role of the primer in addition to blocking water vapor and oxygen, protecting the galvanized steel wire from corrosion, but also can improve the adhesion between the non-vulcanization corrosion resistance sealing paste and the steel wire, the coating pulling force should be ≥ 1.2Mpa;
(2) Scratch 2000-3500μm non-vulcanization corrosion resistance sealing paste, fill the gap between the high-strength steel wires of the main cable, the main component of the non-vulcanization corrosion resistance sealing paste is polyisobutene, the polyisobutene molecular chain is saturated, with good oxygen stability, and the water vapor transmittance is low, it can maintain good fluidity and sealing effect for a long time, the steel wire has better infiltration, the sealing paste also adds desiccant components, and the water vapor sealed inside the main cable can continue to absorb the water vapor sealed inside the main cable after the main cable is formed, reducing the relative humidity of the air inside the main cable;
(3) Tightly wound round steel wire, non-vulcanization corrosion resistance sealing paste will overflow from the inside to fill the wire gap;
Schematic diagram of applying scratch sealant
(4) Remove the excess sealing paste on the surface of the tangle, and then apply the primer, and the coating pulling force should be ≥ 1.2Mpa;
(5) The vulcanized sealant with a total thickness of 1500-2500 μm is scraped and applied multiple times, and the adhesion of the vulcanized sealant and the primer needs to be greater than 4KN/m.
(6) Apply the topcoat in multiple channels.
Sealant system main cable protection case
1.1, the advantages of sealing colloids
Sealant systems have many advantages such as:
1, non-vulcanization corrosion sealing paste gas tightness is good, can provide better protection for the main cable steel wire, Yichang Bridge, Egongyan Bridge and other bridges in the cable inspection found that the outermost layer of the main cable galvanized layer is intact, no serious rust was found, confirming its anti-corrosion effect is remarkable.
2. The selected vulcanized sealant has good elasticity, can adapt to the deformation of the main cable winding wire, excellent aging resistance, and ensures the longevity of the anti-corrosion system of the main cable;
3. The sealant adopts the scraping process, the construction surface has no directionality restrictions, and the construction organization is relatively simple;
4. The maintenance work of the local damaged parts of the main cable in the later stage only needs to remove the original coating and re-scrape it, which is very convenient for construction;
5, the surface of the sealant is well coated, according to the needs of the landscape of its various colors of topcoat coating, later maintenance of re-brush topcoat is also relatively easy.
1.2, the problems of the sealant system
There are also advantages and disadvantages to everything, and there are also many defects in the sealant system, such as:
1, non-vulcanization corrosion sealing paste only scraped on the surface of the main cable steel wire internal steel wire can not be touched, so can not provide protection for the inner layer of the main cable steel wire, from the Yichang Bridge wedge inspection results, the main cable internal steel wire found a large number of secondary corrosion, local 4 corrosion situation, indicating that the protection of the non-vulcanization corrosion sealing paste on the inner layer of steel wire is almost zero;
2, polysulfide sealant for two-component products, high viscosity of the base paste and curing agent between the ratio and mixing uniformity directly affect the performance of the cured sealant, when the ratio is unreasonable or uneven mixing, the strength of the sealant will decrease, after curing a large number of bubbles appear inside the sealant, and even the occurrence of brittle cracking and other undesirable problems, in addition, there may be compatibility problems between the old and new interfaces when the sealant is repaired.
3. Artificial scraping also has its drawbacks, that is, the scraping thickness and uniformity of the main cable surface sealant are difficult to control, and it is easy to appear locally too thin, and the sealing effect is greatly reduced;
4, the main cable of the winding section is not added to the glass fiber cloth, after the sealant is cured, the tear strength is too low, the notch sensitivity is high, one end is damaged, if the sealing agent and the steel wire adhesion is not good, it is easy to have continuous cracking.
The main cable coating of the sealant system falls off
5, in the main cable dehumidification system has become the main cable anti-corrosion standard today, non-vulcanization corrosion sealing paste is not conducive to dry air diffusion to the main cable surface steel wire and winding wire surrounding environment, and the anti-tear poor sealant system is difficult to meet the main cable dehumidification system 3000Pa pressure requirements, the country has found that a number of suspension bridge main cable sealant coatings can not withstand the main cable dehumidification system air pressure caused by the sealing gel bulge or cracking off the situation.
1.3. There is a problem solution for the sealant system
In view of the above problems, Guangzhou Cable New Material Technology Co., Ltd. and other professional companies are in the study of JT/T 694-2007 standard on the basis of improvement and innovation attempts, domestic individual projects have also been used by enterprises with one-component moisture curing type silane-terminated polyether materials to replace two-component polysulfide sealants, to solve the problem of inaccurate mixing ratio of sealants, poor uniformity, and silane-modified polyether material mechanical properties and adhesion to the substrate is also better than polysulfide sealants, However, the curing of wet solid materials requires the absorption of moisture in the air for curing reaction, and when the coating is too thick, the sealant takes a long time to dry thoroughly, and the applicability of the silanyl-terminated polyether material is slightly worse than that of the polysulfide sealant.
Application examples of silane-terminated polyether sealants
The Humen Bridge in 2012 main cable painting overhaul program and Chongqing Inch Beach Bridge main cable coating scheme have adopted the design of adding a glass fiber cloth (that is, two glue clips and one cloth) in the middle of the two layers of polysulfide sealant of the main cable of the whole bridge, although the construction difficulty has increased, but greatly enhanced the tear resistance and pressure resistance of the sealant coating to meet the pressure resistance requirements of the main cable dehumidification system, in the long run, whether there is a risk of delamination between the polysulfide sealant and the fiberglass cloth still needs time to verify.
Full-bridge main cable sealant coating adds fiberglass cloth application cases
2. Main cable wrapping system
Next talk about the main cable wrapping system, the main cable wrapping belt is a kind of modified chlorosulfonated polyethylene material made of two rubber clips a cloth rubber laminated products, the thickness of about 1.2±0.1mm, the color can be customized as needed, the earliest by the United States Brown company in the early 1990s invented, has been successfully applied to the world's major landmark bridges, such as the Danish big and small Belt Bridge, the United States Manhattan Bridge, the United Kingdom Fox Highway Bridge, China Longjiang Bridge, China Several Rivers Yangtze River Bridge, China Dongting Lake Bridge, etc., China began localization research in 2014, and the localization of the wrapping belt products began to be applied on the Qingshuihe Bridge in 2015, followed by the main cable anti-corrosion schemes of Zhuzhou Fengxi Bridge, Zhaoqing Xijiang Special Bridge, Wuhan Yangsigang Bridge, Chongqing Egongyan Double Line Bridge, Jin'an Jinshajiang Bridge, Taoyuan Bridge and Lianzhen Railway Wufengshan Public Railway Dual-use Bridge, and the main cable anti-corrosion schemes currently under construction such as Wujiagang Bridge, Baiyang Bridge, Qipanzhou Yangtze River Bridge, Yichang Yangtze River Bridge and other projects have been designed as anti-corrosion of the wrapping belt.
Schematic diagram of the winding belt structure
Circular wire wrapping tape system main cable protection structure diagram
The results of the main cable opening inspection of the old suspension bridge project at home and abroad show that there is a large amount of corrosion and even wire fracture in the main cable of the early construction. The strength loss of the main cable of the Fuchs Highway Bridge in the United Kingdom is 10% of the height, and the broken wire is still continuing to occur, and after the anti-corrosion transformation of the main cable of the Foss Bridge has increased the dehumidification system of the main cable, with the use of the dehumidification system, when the acoustic emission is monitored non-destructively, it is found that the internal humidity level of the main cable is negatively correlated with the frequency of the main cable broken wire (that is, as the internal humidity of the main cable decreases, the frequency of wire breaking inside the main cable also drops significantly), based on the above research basis, At present, the mainstream view in the industry is that the main cable seal alone can not play a good anti-corrosion protection function on the main cable, a more effective way should be to inject dry air into the main cable, reduce the relative humidity of the main cable wire environment to 40% or less to achieve effective anti-corrosion protection, considering that dry air can be easier to reach the main cable wire and winding surface, the wrapping tape scheme has simplified the design of the anti-corrosion structure of the main cable. Removing the multi-layer primer coating of the main cable high-strength galvanized steel wire and the surface of the winding wire in the sealant system and the non-vulcanization corrosion resistance sealing paste layer inside the winding wire, the anti-corrosion structure of the winding belt is shown in the diagram.
S-type wire wrapping system main cable protection structure diagram
1. The main cable steel wire is wound after the end of the tight cable, and the steel wire can be a round steel wire or an S-shaped steel wire according to actual needs;
2. Use the winding machine to wrap the wrapping belt in the two cables of the main cable according to the stacking ratio of about 52%, and ensure that the surface of the main cable is covered with no less than 2 layers, and the total thickness is not less than 2.2mm.
3. Use an inflatable expansion electric blanket to heat the wrapped wrapping tape, so that the winding tape layer and the layer form an effective hot melt bond.
4, the wrapping belt needs to be embedded in the two sides of the cable ring gap, the gap between the cable ring seam is first compacted with rubber strips, and then the sealant is used for secondary sealing, if necessary, wedge rubber strips can also be installed to improve the reliability of the seal.
Wrap-in tape wrap test
Wrap-in lap effect
Wrap with heated welding
2.1, the advantages of the wrapping belt system
The advantages of the wrapping belt system are:
1. The wrapping belt has a polyester mesh cloth reinforcement layer inside, the tensile strength of the material is far greater than the strength of the sealant, and the tearing strength of the wrapping belt is also much higher than that of the sealant system, and the compressive strength meets the dehumidification requirements of the main cable;
2. The wrapping belt is pre-made into a standard product of about 1.2mm thickness in the factory, and the wrapping is installed through semi-automatic equipment, which is more accurate to control the thickness of the anti-corrosion layer;
3. The wrapping system simplifies the architecture and greatly improves the construction efficiency.
4. The wrapping belt system is mainly for the requirements of no adhesion between its own hot melt bonding and winding wire, and the self-contained system forms a tubular closed air supply channel, which is more conducive to the diffusion of dry air in the dehumidification system and exerts the effect of the dehumidification system.
Schematic diagram of the arrangement of the wrapping tape heating blanket
2.2, the problems of the wrapping belt system
At the same time, the wrapping belt system itself also has some defects that need to be solved, such as:
1, wrapping tape products for vulcanized or semi-vulcanized rubber products, heating bonding by heating blankets, on-site application found that due to the heat dissipation of the steel wire is too fast, the heating blanket pressure is uneven or the surface of the wrapping belt is uneven (the place where the three layers overlap is higher, the place where the two layers overlap is lower) and other reasons, often there is a problem of poor hot melt bonding effect, mainly manifested as the three layers overlapping the place where the bonding is better, the position of the two layers overlapping is poorly bonded or no bonding, which leads to poor integrity of the wrapping belt system, and the sealing is greatly discounted The heating blanket is heated intermittently in sections, which can easily lead to the heating blanket moving forward for too much distance at one time, causing some areas to leak heating, which can easily lead to poor sealing of the main cable;
The blue box part is an area where the heating blanket cannot be heated
Due to the defect in the structure of the inflatable electric heating blanket, there is a non-heating area of about 50mm on both sides of the edge of the heating blanket, which can easily lead to the heating of the wrapping belt near the seam of the cable clamp and the poor sealing.
2, there are certain problems in the storage stability of the wrapping belt, the wrapping belt needs to be used as soon as possible after the production, if the storage is improper (such as storage under high temperature and high humidity conditions) may be due to the precipitation of small molecule additives on the surface of the wrapping belt or the occurrence of self-vulcanization phenomenon and affect the bonding effect of the wrapping belt.
3, wrapping tape and roll between the continuous connection using the way of lap, here will be because of the thickness difference to form a triangular channel, because of the existence of height difference, hot melt sealing is very difficult, such as improper handling will produce air leakage, affecting the sealing effect.
Winding with a leak channel at the joint position
4. The sealing tape is sealed with sealant at the position of the cable clamp ring seam, the adhesive of the sealant and the wrapping belt is insufficient, the ring seam sealing link is relatively weak, and there is a risk of air leakage.
5, the repair of the wrapping belt needs to be hot melted, in the field environment of the main cable at high altitude, if there is no power supply conditions, the repair of its damaged parts is more difficult than the repair of the sealant system.
6, the wrapping belt for rubber products, the surface finish is not as good as paint, in the outdoor use of easy to accumulate ash to cause dirt, affecting the appearance, and the spiral structure produced by the construction of the wrapping belt makes the later stage of its re-coating caused certain obstacles, in addition, the wrapping belt as a rubber product, there are also easy to fade, frost spray and other problems affecting the appearance.
The main cable is wrapped with dirty surfaces
7, wrapping belt simplifies the anti-corrosion system of the main cable, high hopes for the role of the dehumidification system, and once the dehumidification system effect is not good or unstable, it is tantamount to putting the main cable in a dangerous situation, when the anti-corrosion effect may be worse than the sealant anti-corrosion system.
8. The adhesion of the anti-slip coating on the top of the main cable is not good, and the anti-slip sand is easy to fall off.
The main cable is wrapped with frost spray and fading
2.2, wrapping belt system problem solution
Most of the problems existing in the above-mentioned wrapping belt can be continuously improved by the R&D and production organization of the wrapping belt, and at the same time, the construction team needs to improve the more refined construction process. In view of the inconvenience of heating the main cable wrapping belt, the domestic Guangzhou Cable New Material Technology Co., Ltd. and other units have begun the research and development of self-adhesive cold winding tape, which will greatly improve the construction efficiency, especially the construction difficulty of the maintenance of the main cable of the old bridge. In addition, the Guangzhou Cable New Materials team is trying to reduce the problem of dirt on the main cable by spraying hydrophobic materials on the surface of the wrapping tape.
Main cable crawl repair platform for the Forth Road Bridge in the United Kingdom
The main cable of the British Severn Bridge lifts and repairs the hanging basket
epilogue
In summary, the current two mainstream main cable anti-corrosion systems in China currently have their own advantages and disadvantages, in order to ensure that the suspension bridge main cable life can meet the design requirements, we also need to continuously improve it and promote the continuous improvement of technology.
About the author
Zhou Bo, cable protection professional
Graduated from Sun Yat-sen University (Polymer Materials and Engineering) in 2008
For more than ten years, he has focused on the research and development of materials and construction technologies for bridge cable protection
Engaged in the new construction of beam cable protection system and the inspection and maintenance during the operation period.
Led the localization research of anti-corrosion wrapping tape anti-corrosion technology of the main cable of the suspension bridge
Compared with similar domestic products, the products developed have the characteristics of high color fastness and good sealing;
Developed a special fluorinated film protection tape that can replace the anti-corrosion of the cable-stayed cable of imported DuPont company
Familiar with the AMERICAN NCHRP-534 guide and the corrosion mechanism of steel wire of the main cable of the suspension bridge;
Participated in the inspection and maintenance of dozens of long-span cable bridge protection systems