金三銀四果然是招聘的好時節。剛發出招聘文章(投履歷點我點我)沒多久,我們就迎來了營運新同僚。
極其養生的新同僚在發現大家中午都沒午睡習慣後,「太卷了」就變成了她的口頭禅。
拜托,我司 10 點才上班,中午哪裡睡得着。
真要論「卷」,還得是各位老闆。
現在,各大科技公司老闆抛頭露面為自家産品站台已經不是什麼新鮮事。
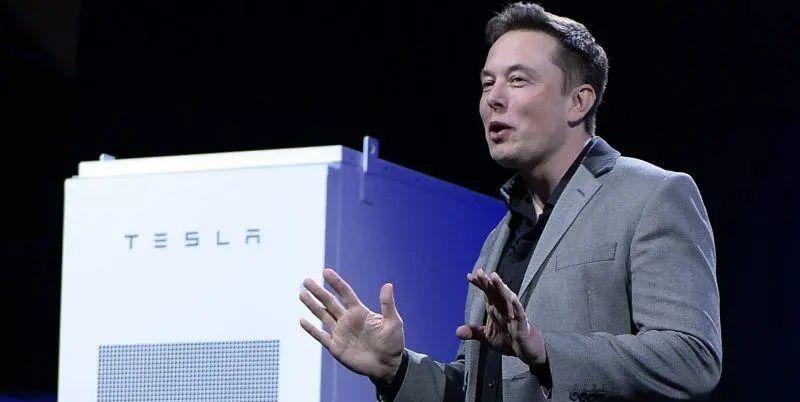
隻不過,最近 Lucid Motors CEO Peter Rawlinson 把這個标準又往上提了一大截。
作為曾經的特斯拉 Model S 首席工程師,Rawlinson 無疑是一位技術流的管理者。
他通過一場電池技術溝通會,充分向大家展示了,什麼叫「不懂技術的靈魂畫不是優秀 CEO」。
作為當下全球 EPA 續航最長的量産車,Lucid Air 的電池組有哪些小秘密?
高電壓 = 高效率
Lucid Air Grand Touring 搭載了 112 kWh 電池包,112 kWh 到底是多少能量?
Rawlinson 給我們舉了一個非常生動的例子。
「我們把一個 100 克的蘋果,從地上撿起,放到離地 1 米高的桌面上,這個過程消耗 1 焦耳的能量。而 112 kWh 電池包,換算過來大約有 4 億焦耳,可以讓我們做 4 億次撿蘋果的動作。」
那 112 kWh 這個參數是如何确定的?
Rawlinson 先講解了能量與功率之間的關系,并為我們介紹了一個非常清晰、易懂的計算過程。
大約在 10 年前,電動汽車每行駛 1 英裡約消耗 330 Wh 電量,随着技術的進步。到今天,電動汽車行駛 1 英裡消耗的電量已經下降到 250 Wh。
如果想要讓電動汽車擁有 400 英裡的續航,就需要 100 kWh 電池包。
我們繼續推算,Lucid Air 使用的 2170 電池,每粒電芯約有 17-18 Wh 的電量,組成 100 kWh 電池包就需要大約 6000 粒 2170 電芯。
這就是 Lucid Air 電池包,6600 個 2170 電芯的設計基礎。
但堆電池,大家都會,對于一輛全球 EPA 續航最長的電動汽車來說,當然還有一些不一樣的技巧。
比如,現階段電動汽車的電池包電壓一般都在 400V 左右,而 Lucid 使用了 924V 高電壓。
至于為什麼這麼做,Rawlinson 用幾個非常基礎的實體公式向我們闡述了選擇高壓電池背後的理論支援。
歐姆定律
電壓 U = 電流 I × 電阻 R ------------
電功率計算公式
功率 P = 電壓 U × 電流 I ------------
把公式 帶入到公式 ,可以得到
P = I^2 × R
這個也是系統電阻發熱量的計算公式。
而這個發熱量對我們是無用的,我們希望它越小越好。
根據 P = I^2 × R 可知,電流 I 越小,發熱量的功率 P 就越小。
問題來了,如何在保持系統功率總量不變的情況下,降低電流呢?
由 P = U × I 可知,當功率 P 保持不變,我們增大電壓 U,電流 I 就會減小。
以 Lucid Air 為例,Lucid 把電池包電壓提高到兩倍,電流就會變為原來的二分之一,發熱功率就會降低到原來的四分之一。
是以,高壓就意味着更高的驅動效率,這就是 Lucid 選擇高壓電池包的一大原因。
如何建構 924V 電壓
一粒 2170 電芯的滿電電壓是 4.2V,那麼 4.2V 如何升壓到 924V ?
首先,我們先介紹一個電池串并聯的知識點。電池串聯,能提高輸出電壓;電池并聯,能提高輸出電流。
Rawlinson 拿了 3 個不同長度、不同電壓等級的手電筒來打比方。
這些手電都使用 1.5V 的 1 号幹電池作為能源。把 3 個幹電池串聯塞進手電,就能得到一個 4.5V 電壓的手電;4 個幹電池串聯,就得到 6V;6 個幹電池串聯就得到 9V。
同理,4.2V 的 2170 電芯想升壓到 924V 電壓,就需要把 220 個 2170 電芯串聯起來。
但如果像手電這樣的方式串聯電池,220 個 2170 電芯首尾相接串聯在一起,長度差不多就有 15 米。這種長度放在轎車上顯然是不合适的。
實際上,Lucid 為了兼顧電壓等級和電流輸出能力,将 6600 粒 2170 電芯分為了 22 個組,每 300 粒電芯組成一個電池模組。
在一個電池模組中,又把 300 粒 2170 電芯平均分成了 10 組。每 30 粒電芯互相并聯,組成一個「Group」。
一個模組中的 10 個 Group 串聯,就得到了 42V 輸出電壓。
為了能讓 300 粒電芯以「豎直且平行」地擺放組成一個電池模組,Lucid 為此做出了兩點努力。
一是,讓 2170 電芯的正負極都處于電芯的同一端。
這個設計其實我們在之前解讀特斯拉專利的文章中也提到過,有興趣的小夥伴可以點選此處跳轉檢視。這樣做的好處也很明顯,所有電芯都隻需豎直向上擺放,通過正、負極母排連接配接器即可完成電芯之間的串并聯。
二是,電池連接配接技術。
在提到這些連接配接器時,Peter 提到一個很時髦的詞,「一體壓鑄」。沒錯,這些連接配接器正是由一體壓鑄技術制造出來的。
同時,Rawlinson 還非常詳細地介紹了為什麼選擇鋁作為連接配接器的材料。連接配接器最主要的功能就是導電,連接配接器的電阻越小,發熱越低,效率就越高。從這個角度出發,我們應該選擇電阻最低的金屬——銀。但銀的價格太貴,結合成本和導電率兩個因素,銅就成為了首選。但是銅又比較重。
綜合導電率、成本、重量三個因素,鋁就成為了連接配接器材料的最好選擇。
在把電芯焊接到母排連接配接器上時,Lucid 也有自己的小心思。
為了確定安全,業界通常的做法是,把電芯的正、負極分别都用保險絲焊接到母排連接配接器上。如果單個電芯發生短路的情況,保險絲會瞬間熔斷,将電芯從電池模組中斷開,進而確定電池模組的安全。
但 Lucid 發現,對單個電芯而言,用兩根保險絲其實完全沒有必要。其一,電池正、負兩極隻要有其中一端斷開,這個電芯就與電池模組的連接配接就斷開了;其二,保險絲相比較普通連接配接材料,保險絲的電阻更大,效率更低。
是以,Lucid 選擇在電芯的正極上使用保險絲焊接,在負極上用較粗的普通導體焊接。
講完了單個電池模組,再把 22 個電池模組串聯起來,就得到了 924V 輸出電壓。
至此,小結一下,Lucid 用 220 串聯,30 并聯的連接配接方法,将 6600 粒 2170 電芯組成了 112 kWh、924V 電池包。
不一樣的冷卻方案
Rawlinson 提到,業界常用的電池模組冷卻方案,都是在一粒粒電芯之間設定冷卻管路,但 Lucid 認為這種冷卻方式是極為低效的,原因有以下兩點。
1. 電芯熱量問題
電芯在工作時會向各個方向散發熱量,但在不同方向上,熱量的傳導效率是不一樣的。Lucid 發現,電芯熱量在縱向方向上的傳導效率遠大于橫向方向。
這樣的結果是,電芯工作散發的熱量會在電芯底部聚集。
2. 效率問題
布置在電芯之間的冷卻管路,其一,冷卻管路與電芯的接觸面積并不像理想狀态下的那麼大,實際上,它們之間的接觸面積并不連續,而是斷斷續續的。
其二,冷卻管路會擠占電池模組空間,最為直接的後果,就是在同樣體積的電池模組内,能容納的電芯數量會減少,進而降低電池模組的能量密度。
基于以上兩點,Lucid 采取了一種和特斯拉完全不同的冷卻方案。Lucid 取消了電芯間的冷卻管路,轉而在電池模組底部設定了一塊冷卻闆。
這樣設計的好處有以下三點。
1. 高效散熱
前面提到,電芯的熱量最終會在電芯底部積聚,直接從電芯底部帶走熱量,無疑是最高效的。其次,電芯底部是一個平面,散熱闆的接觸面也是一個平面,這樣一來,兩個平面之間可以輕易且緊密地接觸在一起,這進一步提升了散熱的效率。
2. 提高能量密度
電芯之間沒有了散熱管路阻隔,電芯和電芯之間可以以更緊密的距離進行排布。即,電池模組的能量密度将會更高。
3. 便于制造
冷卻闆是由兩片沖壓鋁材組合而成的。而沖壓是一種非常利于大規模量産的生産工藝。這就意味着,這種冷卻闆擁有較低的成本,較低的生産難度,更好的一緻性和可靠性。
因為 Peter Rawlinson 曾經是特斯拉 Model S 首席工程師,因為 Lucid Air 和特斯拉 Model S 在技術結構上有太多相似處,曾經有人告訴我,Lucid Air 隻不過是一輛換殼特斯拉 Model S。
但實際上,我們通過了解技術細節,Lucid 其實是擁有自我靈魂的。
單從電池包來說,我們就能感受到,Lucid 自上而下貫徹的節能高效的設計理念。
這可能也是 Lucid Air 能拿下 EPA 第一續航的奧秘之一吧。
Lucid Air 是輛好車,隻是,現在它挑戰特斯拉的最大阻礙就是産量不足問題。
根據先前 Lucid 釋出的 2021 年财報,受晶片等供應鍊問題影響,Lucid 2022 年産量預期下調 40%,2022 年全年産量也就隻夠滿足目前 Lucid 手裡預定訂單的一半。
這也就意味着,常老師心心念的 Lucid Air,今年應該是買不着了。
-END-
(請記得關注我們的視訊号,一大波新車官宣來咯)