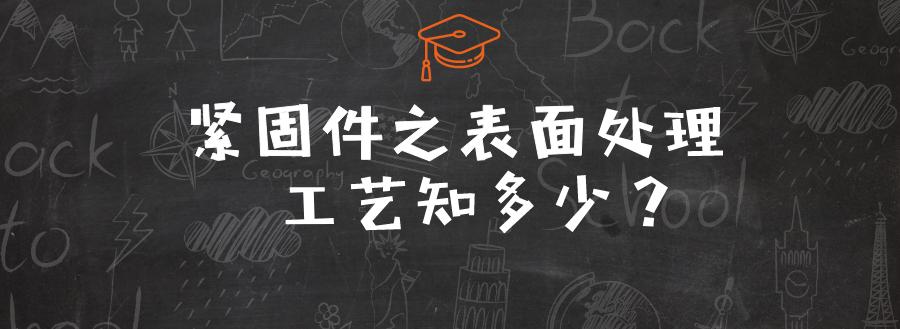
In order to look more beautiful and beautiful, screw fasteners will be treated in many ways. Many screw fasteners are extremely environmentally friendly and polluting, so in recent years, more and more companies have used stainless steel to manufacture screws.
Today we will talk about several surface treatment methods commonly used in the screw fastener industry.
The surface treatment of fasteners is the process of forming a covering layer on the surface of the workpiece by a certain method, the purpose of which is to give the workpiece surface aesthetic and anti-corrosion effect, and its treatment method can be attributed to the following:
1. Plating
The part receiving the plating is immersed in an aqueous solution containing the metal compound to be deposited, and an electric current is passed through the plating solution, so that the electroplated metal precipitates and deposits on the part. General electroplating has galvanizing, copper, nickel, chromium, copper-nickel alloys, etc., and sometimes boiled black (blue), phosphating, etc. are also included.
2. Hot-dip galvanizing
This is done by submerging the carbon steel parts in a plating tank with dissolved zinc at a temperature of approximately 510 °C. The result is that the iron-zinc alloy on the surface of the steel part gradually becomes passivated zinc on the outer surface of the product. Hot-dip aluminum plating is a similar process.
3. Mechanical plating
Particles coated with metal are used to impact the surface of the product and the coating is cold welded to the surface of the product.
Generally, the screws are mostly electroplating, but the outdoor hexagonal wooden screws used in electricity, highways and other outdoors are mostly hot-dip galvanized; the cost of electroplating is generally 0.6-0.8 yuan per kilogram, and the hot-dip galvanizing is generally 1.5-2 yuan / kg, which is higher.
The following is a small compilation of the more commonly used fastener surface treatment methods:
Galvanized
Electroplating is the process of using electrolysis to form a uniform, dense, well-bonded metal or alloy deposition layer on the surface of the product. Compared with other metals, zinc is a relatively inexpensive and easy to coat a metal, especially to prevent atmospheric corrosion, the bottom value of anti-corrosion plating, is widely used to protect steel parts, and used for decoration.
Galvanized fastener torque - the preload consistency is poor, and unstable, and is generally not used for the connection of important parts. In order to improve the torque-preload consistency, the torque-preload consistency can also be improved and improved by coating the lubricating substance after plating.
According to the different plating solutions, electrogalvanizing is mainly divided into four categories: cyanide galvanizing, chloride galvanizing, zincate galvanizing, sulfate galvanizing.
Process
Hydrogen embrittlement
During the production process of fasteners, especially during pickling before plating and subsequent plating, hydrogen atoms are absorbed on the surface, and then the deposited metal coating also captures hydrogen atoms. When the fasteners are tightened, the hydrogen atoms are transferred toward the stress concentration part, causing the pressure to increase to exceed the strength of the matrix metal, resulting in a tiny surface rupture. The active hydrogen atoms then quickly seeped into the newly formed crack, and this "pressure-rupture-infiltration" cycle continued until the fastener ruptured. The above usually occurs within a few hours of the first stress.
Hydrogen removal process
Except for hydrogen heating is generally between 190-230 ° C, the time is 4-24 hours, and preferably 1 hour after plating and before chromate treatment.
Phosphating
Phosphorization (phosphorization) is a chemical and electrochemical reaction to form a phosphate chemical conversion film process, the formation of phosphate conversion film is called phosphating film, the thickness of the film is generally 10-15 microns, friction coefficient of about 0.05.
The high-strength bolt adopts phosphating, which can also avoid the problem of hydrogen embrittlement, so the bolts above 10.9 level in the industrial field generally use phosphating surface treatment.
The purpose of phosphating is mainly to provide protection for the matrix metal and prevent the metal from being corroded to a certain extent; it is used to base before painting to improve the adhesion and anti-corrosion ability of the paint film layer; and to reduce friction and lubrication in the metal cold processing process.
Phosphating process categories:
According to the different performance can be divided into: rust removal phosphating process, wear-resistant film lubrication phosphating process, paint pre-paint phosphating process.
According to the phosphating membrane system, it is divided into: zinc system, zinc calcium system, zinc manganese system, iron system, amorphous phase iron system.
According to the different treatment temperatures, it is divided into: room temperature phosphating (no heating), low temperature phosphating (25-45 °C), medium temperature phosphating (60-70 °C), high temperature phosphating (> 80 °C)
Dacro
Dacromet is a transliteration and abbreviation of DACROMET, abbreviated as Dacromet, Dacro, Dak Rust, and Dikron. Domestic named zinc chromium coating, is a new type of anti-corrosion coating with zinc powder, aluminum powder, chromic acid and deionized water as the main components.
Dacro has a high degree of corrosion resistance, in China is in the germination stage of cleaner production process and a high-tech, known as the international surface treatment industry with epoch-making new technology. This process can replace steel galvanizing, cadmium, zinc-based alloys, hot-dip galvanizing, hot-spray galvanizing, mechanical galvanizing.
merit:
Dacro is a new type of surface treatment technology, compared to the traditional electroplating process, dacro is a "green plating". Its advantages are as follows:
1) Super corrosion resistance
2) No hydrogen embrittlement
3) High heat resistance
4) Good adhesion and recoating performance
5) Good permeability
6) No pollution and pollution
flaw:
1) Dacromet contains chromium ions.
2) Dacro's sintering temperature is high, the time is long, and the energy consumption is large.
3) Dacro's surface hardness is not high, wear resistance is not good, and Dacromet coated products are not suitable for contact and connection with copper, magnesium, nickel and stainless steel parts, because they will produce contact corrosion, affecting the surface quality and anti-corrosion performance of products.
4) The surface color of dacro coating is single, only silver white and silver gray, which is not suitable for the personalized needs of automobile development.
5) The conductivity of the dacro coating is not too good, so it should not be used for parts of the conductive connection, such as the grounding bolt of the electrical appliance.
There is no hydrogen embrittlement problem, and the torque-preload consistency is very good. Regardless of the valence chromium and environmental issues, it is actually the most suitable for high-strength fasteners with high corrosion protection requirements.
Black/blue
Blackening is a common means of chemical surface treatment, the principle is to make the metal surface produce a layer of oxide film with a thickness of 0.6 ~ 0.8 microns (ferric oxide) to isolate the air and achieve the purpose of anti-rust. When the appearance requirements are not high, it can be blackened, and the surface of steel parts is blackened, and it is also called blue.
The commonly used methods of blackning treatment are traditional alkaline heating blackening and late room temperature blackning. However, the effect of the room temperature blackning process for low-carbon steel is not very good.
Alkaline blackness is subdivided, and there is a difference between one blackening and two blackenings. The main components of the blackening liquid are sodium hydroxide and sodium nitrite. The temperature required for blackening is larger, and a good surface can be obtained between about 135-155 ° C, but the time required is only a little short.