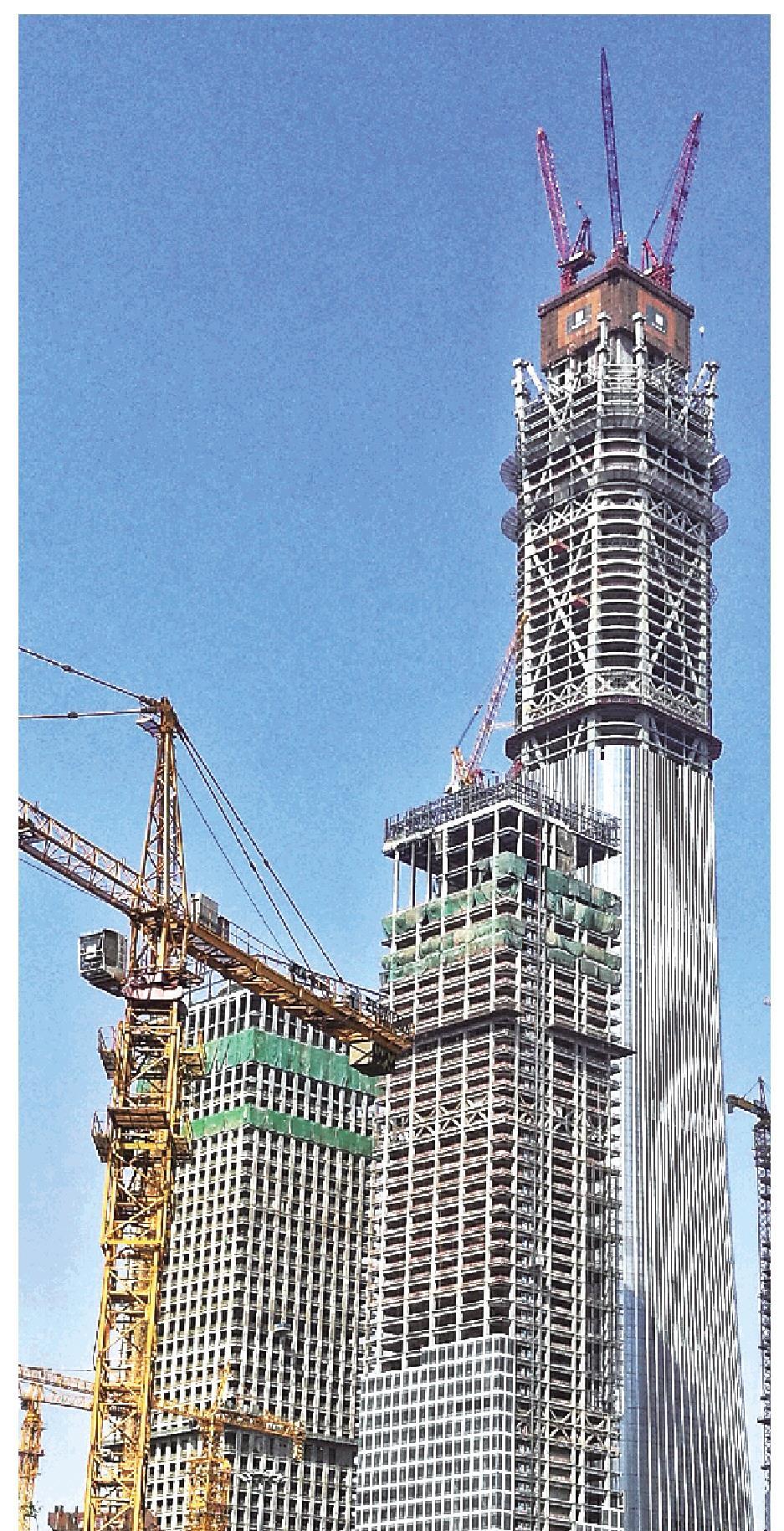
The aerial building machine is located at the top of the building, like a "big box". Xinhua News Agency issued a ← scan code for more wonderful
Among the top 10 high-rise buildings in the world, China accounts for 7. Zhang Kun, chief expert of China State Construction Group and chief engineer of China Construction Third Bureau, who has participated in the construction of eight super high-rise projects of more than 400 meters, told the scientific and technological forces behind China's construction with a number of cases at the third campus report meeting of "The Spirit of the Times Yao Xiangjiang" held on the afternoon of October 27.
Breakthrough height Aerial building machines are widely used in skyscraper construction
The tallest building in Beijing, "China Zun", has 108 floors above ground and 7 floors underground, with a total height of 528 meters, making it the 8th tallest in the world. The duration of the contract is 46 months. "Before that, no building over 400 meters had a shorter construction period than this, which prompted us to adopt many other new technologies to cope with the needs of the construction period."
When you look far away at the tall building under construction, you will find that there is a "big box" at the top, and as the construction progresses, this big box also rises and is always on top of the building. This is the weapon of rapid construction of skyscrapers - aerial building machines.
According to Zhang Kun, the "aerial building machine" is the integrated platform for intelligent construction equipment of super high-rise buildings, which is to integrate all kinds of equipment and facilities required in the construction of the project on the platform to create a "super high-rise construction factory" and provide a full range of services for formwork engineering, steel engineering, steel structure installation, fire protection, lighting, etc. "Just like the 'aerial building machine' used by China Zun Building during the construction process, it is a 7-story 'big box' with a height of tens of meters. Its own weight is more than 4,000 tons. ”
With the help of aerial building machines, the tower crane can be lifted synchronously with the platform as a whole, saving construction time, reducing safety risks and improving construction efficiency. "When you finish one floor, you ascend one floor." Such a huge system requires an intelligent monitoring system. "We have also developed a special control platform for this purpose, the software operation platform. Realize the integrated platform for all-round online monitoring. Through the operation status analysis and over-limit safety warning, the platform can be safely operated. According to him, under normal circumstances, as long as a button is pressed, the aerial building machine can raise the height of one floor after an hour.
Nowadays, this intelligent construction equipment integration platform for super high-rise buildings has been widely used in the construction of many skyscrapers. "We popularize this technology and apply it to ordinary houses, it makes our operation safer, more convenient construction, faster and better quality, and has been called 'residential building machine'."
Breakthrough difficulty Large-volume concrete construction Computer temperature measurement interval is as short as 1 second
Construction of the new CCTV building began in 2005, 16 years ago. Many people may not know that the adjustment of a plan at that time saved 100 million yuan in construction costs for the project.
"The CCTV new site building is a representative of the engineering difficulty I have experienced in the project." According to Zhang Kun, the structure of the CCTV building is very complicated. "The vertical part of it is actually tilted, and we call the twin towers tilting inward by 6 degrees." At the top of it, there is an L-shaped two-way cantilever, "Tower 1 cantilever extension 67.165m, Tower 2 cantilever extension 75.165m, only the total weight of the cantilever part is about 18,000 tons, equivalent to the total amount of engineering steel structures of general scale." "In addition, the project has a cantilever structure, which is 162.2 meters above the ground.
In the face of complex structural deformation control, in the early stage of engineering construction, the construction party proposed a more stable and traditional plan: "That is, to set up a very stable bracket to ensure that the structure is not deformed or less deformed." "But the shortcomings of this scheme are also more obvious, just to set up a bracket, the steel needed is more than 10,000 tons." According to the cost in 2005, the increase in construction costs was more than 100 million yuan, so this scheme is not very desirable. ”
As a result, a scheme with the help of more advanced technology, through more precise calculations and careful control, was finally implemented. "The principle of this scheme is very simple, there are only three or five steps to operate, and it feels really easy to do." But in fact, the project has a total of more than 50,000 components, which means that after the construction of the bottom layer is completed, there will be more than 50,000 loads on the top. How to deal with it? "We have summarized 6 major solutions, package curing process, iterative analysis, pre-conditioning processing, offset installation, monitoring and comparison and real-time adjustment. Even invited Tsinghua University, East China Design Institute and other universities to help. ”
"The construction of very large concrete is also a big test." According to Zhang Kun, only the bottom slab of the main building requires 120,000 cubic meters of concrete, which is equivalent to the total amount of a general project. "In large-volume concrete construction, if the hydration heat treatment is not good, it will produce a so-called temperature crack, and this crack will affect the safety of the building." In the early years, we still measured temperature by hand, and now we have developed a large-volume concrete computer temperature measurement system, the temperature measurement interval is as short as 1 second, the temperature measurement accuracy is 0.1 °C, and the temperature measurement error ≤ 0.2 °C. ”
Breakthrough speed unit integral transport field modular installation
In 2020, Wuhan Vulcan Mountain and Leishenshan Hospital were built when all the access to and from Wuhan was closed. "The amount of personnel, machinery and material resources required for hospital construction is large, and it is extremely difficult to raise resources under the extreme conditions of the superposition of the epidemic, the Spring Festival and the lockdown."
In order to improve the speed of construction, in terms of design, both hospitals used the "design and construction integration technology" to reverse design according to the materials that can be raised to meet the requirements of rapid construction.
In order to achieve rapid construction, during construction, both projects adopt modular units for the foundation, ward units, mechanical and electrical equipment, rain and sewage treatment, integrated bathrooms and medical functions, etc., and the overall transportation of the units and on-site modular installation.
It is worth mentioning that the two projects fully used BIM technology for construction simulation, simulated the site layout, and simulated the exhaust gas emissions in the hospital area, the airflow organization in the ward and the diffusion of pollutants. In addition, the resource management platform based on the Internet of Things assists vehicle scheduling through satellite positioning and organizes material entry in an orderly manner. In addition, through the real-time live broadcast of the central video, 200 million people watched, realizing the openness and transparency of the construction process.
Writer: Nandu reporter N video reporter Chen Canrong Wang Shiqi Yi Xiaoxia Huang Haishan Photo: Nandu reporter N video reporter Chen Canrong (except for the signature)