3.1 Basic requirements for copper dissolved production
Electrolytic copper foil production, is the copper ions from the aqueous solution of copper sulfate through electrodeposition of copper deposition on the cathode, the formation of copper foil, in order to obtain the ideal electrolytic copper foil, the quality of the electrolyte is crucial. What kind of electrolyte is needed for the production of what kind of copper foil, and the electrolyte is the source of raw materials for the production of electrolytic copper foil. Therefore, the preparation of electrolyte is the first process of electrolytic copper foil production, and the first quality assurance of electrolytic copper foil.
3.1.1 Basic requirements for electrolyte
The electrolyte must be very clean, the electrolyte is the blood produced by the electrolytic copper foil, the electrolytic copper foil is a defect-free product, and it will get sick if it is not clean. For the production of electrolytic copper foil, the electrolyte is not too clean. The maximum allowable content of inorganic impurities in the electrolyte: zinc < 1.0 g/L, iron < 1.5 g/L, antimony < 0.15 g/L, lead < 0.1 g/L, nickel < 0.1 g/L, cadmium < 0.1 g/L, chromium < 0.3 g/L. The content of non-copper inorganic metal ions in the electrolyte must be within the allowable range, and the lower the better, and it is not possible at all. The lower the anion content of non-sulfate, the better, and it is not possible to have none at all. The organic content should be close to zero, except for the addition required by production. Suspended impurities such as mud are not allowed to exist, and the maximum diameter of the particles filtered by the electrolyte is less than 0.5 μm. The diameter of the added organic particles does not exceed 0.2 μm at most.
The stability of electrolyte composition is a necessary condition for the production of electrolytic copper foil, and it is best for each component to be in a basically unchanged state in the production process, and the fluctuation range should be small. Various elements should be non-toxic and environmentally friendly, less corrosive, convenient to purchase, and economically available. The selection of process parameters is environmentally friendly and economical, easy to apply, easy to manage, easy to control, and easy to adjust.
The cost of electrolyte is low, raw and auxiliary materials are easy to purchase, process, and the chemical composition meets the technical requirements of production and products. The electrolyte evaporation gas should be non-toxic, conducive to purification and treatment, no pollution to the environment, and harmless to people and animals.
3.1.2 Requirements for copper dissolving equipment
In order to achieve the normal production of high-quality electrolytic copper foil, the requirements for copper dissolution equipment that are important in the manufacture of electrolytic copper foil are as follows:
(1) Copper dissolving tank is the main equipment in copper dissolving equipment. Its structure is: hot water inlet and outlet pipe and column tube heat exchanger, air inlet pipe and annular air distributor, inlet pipe and distributor; acid gas discharge pipe, solution outflow sieve plate, copper dissolving tank lid (can be hoisted). The requirements for the copper dissolving tank should be strong and durable, not easy to deform; the copper dissolved tank should be acid corrosion resistant, have good heat resistance, heat conductivity. The surface of the copper dissolving tank should be insulated, which is very important for energy saving and consumption reduction.
(2) The temperature of the copper dissolved liquid in the copper dissolving tank should rise rapidly, the heat loss is small, and the energy consumption is saved.
(3) When using the copper dissolving tank to dissolve copper, it is required that the heat and oxygen (air) are evenly distributed, and the various parts of the copper dissolved tank can be stirred fiercely and evenly, and there is no dead angle.
(4) It is required that the pipeline is not easy to crystallize, and it is convenient to empty the liquid when the production is stopped, and it is easy to clean up. In order to prevent crystallization, the inlet liquid and air intake lines should be placed in the copper dissolving tank, so they should be welded to the inner wall of the copper dissolving tank.
(5) The operating system of the copper dissolving tank requires convenient feeding. The electrolyte should be circulated smoothly and uniformly, and the control of fast and slow is simple and convenient. It is best to have a large opening on the top of the copper dissolving tank, which facilitates the cleaning of the clay pot during the shutdown period.
(6) The copper dissolving tank should be tightly sealed, and the acid gas in the tank should not leak out; the dust outside the tank cannot enter; it is conducive to keeping the electrolyte clean and not susceptible to secondary pollution.
(7) All pipelines are easy to close and connect, not easy to damage, minimize joints and connection points, and prevent corrosion leakage.
(8) The exhaust air is unobstructed, and different flow rate sections are provided to cool the sulfuric acid in the exhaust gas back into the copper dissolving tank. The exhaust fan is set behind the acid mist purification tower and protects the fan.
3.3 The process flow of dissolved copper to make liquid
There are currently a variety of processes for copper dissolving liquids. According to its temperature division, there are high temperature dissolved copper (80 ° - 85 ° C); there is medium temperature soluble copper (70 ~ 75 ° C); there is low temperature dissolved copper (55 ~ 60 ° C); according to the solution leaching division, there are copper raw materials all immersed in the electrolyte, called soaking copper, there is a spray type copper dissolving on the copper raw material spray electrolyte, called spraying copper dissolving. Copper dissolving method should be based on regional climatic conditions, such as the northern winter temperature in minus 30 ° C, a bowl of boiling water spilled out, that is, become ice, this temperature is certainly not suitable for spray copper dissolving method. In my actual experience in production, I think that whether it is the south or the north, or the advantages of soaked copper dissolving, it is recommended that you use soaked copper dissolving.
Here are a few different copper dissolving processes:
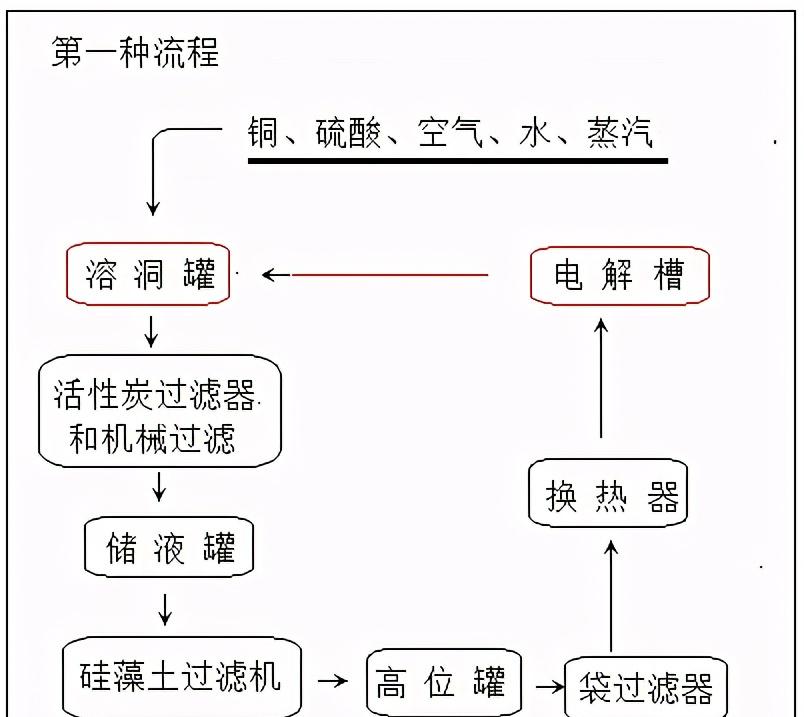
Figure 3-1 Copper dissolved liquid production process (1)
Figure 3-2 Copper dissolving process (2)
Figure 3-3 Copper dissolving process (3)
Fig. 3-4 Copper dissolving process (4)
The way copper is dissolved is different, but the mechanism is the same. The metal copper performs a series of multiphase reactions at a liquid temperature of 60 ° C in the copper dissolved tank under alternating contact with sulfuric acid and oxygen. Air is integrated into the electrolyte (exothermic reaction), oxygen and copper are oxidized (exothermic reaction), sulfuric acid is reacted with copper oxide (exothermic reaction), sulfuric acid is reacted with copper, and sulfuric acid reacts with air. The metal copper becomes ionic copper, which becomes an aqueous solution of copper sulfate. When the concentration of copper ions reaches 120-140g/L, self-overflow and outflow, through the natural filtration of granular activated carbon, remove the suspended impurities and part of the organic matter in the electrolyte, flow into the storage tank, and mix with the electrolyte flowing back from the electrolyzer to supplement the divalent copper ions reduced by the electrolyte after the electrolyte is deposited into copper foil. The electrolyte in the storage tank is continuously injected into the copper dissolving tank according to the required amount by the special circulation pump, and the electrolyte containing the high concentration of divalent copper ions in the copper dissolving tank continuously flows into the storage tank to supplement the reduced divalent copper ions in the electrolysis system. Achieve the balance between copper dissolved and electrolytic copper.
3.4 Air supply and exhaust system in the dissolved copper tank
Supplying air to the electrolyte in the copper dissolved tank has two main functions:
One is oxygen supply, which is an indispensable element for copper to dissolve into copper sulfate. If there is no oxygen metal copper will stop dissolving, in the production of electrolytic copper foil, even if there is a little oxygen brought into the electrolyte, copper dissolves very slowly. If there is a lack of oxygen when dissolving copper, the metal copper will dissolve into a valent copper ion, or atomic copper powder, which becomes an impurity in the production of electrolytic copper foil, which is very harmful.
The second is to stir the copper-soluble reaction in the copper dissolving tank, so that the reaction product quickly leaves the surface of the raw material, and the reactant is quickly transferred to the surface of the raw material and directly collides to react. To achieve the rapid progression of the reaction cycle, this is often not recognized, so the feeding into the copper dissolving tank is very casual, and the distribution of the wind is uniform or not.
The air supply of immersion copper can be directly supplied to the copper dissolving tank by blower, compression air compressor. The spray type copper dissolving fan uses an exhaust fan to make the copper dissolving tower negative pressure, and the air enters the copper dissolving tower by atmospheric pressure. The most ideal for soaking copper dissolving is to use an oil-free compression air compressor, which has the advantages of clean air, large air pressure and fierce agitation. The air supplied must be very clean, dust-free, water-free, oil-free, greasy-free, and free of impurities. Continuous air supply should be maintained to maintain sufficiently stable air volume, wind pressure and wind temperature. The copper dissolution speed is directly related to the air volume, wind pressure and wind temperature supplied. Air volume and wind pressure are the main methods to adjust the rate of copper dissolution. When the copper concentration in the electrolyte is high, the air supply can be reduced in an appropriate amount, and the copper concentration will slowly decrease. When the copper concentration in the electrolyte is low, the air volume can be increased in an appropriate amount, and the copper concentration will slowly rise.
The key to the reaction of copper dissolving is to supply wind, as long as the air volume and wind pressure are sufficient, the heat of copper dissolving will continue to generate a supply solution. Copper dissolving temperature is the catalyst for copper dissolving speed, and ensuring sufficient air supply capacity is the key to copper dissolving production. When installing the air supply pipe, pay attention to prevent the electrolyte from entering the air pipe when the wind is stopped, so as to avoid the supply air pipeline being blocked by copper sulfate crystals. If this happens, it is best to use steam to dissolve the crystallized copper sulfate, if you can't use steam, you can only cut the pipeline and replace it with a new one. The air supply line in the dissolved copper tank is generally made of 316L stainless steel, which is temperature-resistant and impact-resistant.
When the air passes through the raw material layer in the copper dissolving tank, the oxygen is exhausted, and the process of stirring the solution is completed, and some particles of acid and copper ions are adhered to the air bubble. When copper is dissolved, there will be a lot of air and water vapor to be discharged. These water vapors also carry some acid and copper ion particles, so these gases must be treated during the discharge process. The acid and copper are separated to ensure that the exhaust gas does not pollute the environment. Acid mist separators can be used in the north of the spiral plate type, when the weather is hot into the cold water, when the weather is cool into the natural cold air. The acid vapor is cooled into acid water and naturally flows back into the dissolved copper tank. This method can also be used in the south, and professional acid mist purification towers can also be used, equipped with acid-resistant exhaust fans (see Figures 3-5).
Figure 3-5 Copper-soluble air supply and exhaust system
Some fans use screw air compressors, and some use roots blowers. I think it is best to use an air compressor to dissolve copper, with large air volume, high wind pressure, strong mixing capacity, and a single dissolved copper tank can be filled with copper. So that the copper dissolving tank gives full play to the role of copper dissolving, heating and filtration, the copper dissolving capacity is large, and a single can can supply multiple foil machines. Roots blower air volume can be, the wind pressure is too low, the copper dissolving tank can not be charged more. The copper material in the copper dissolving tank is too much, the wind drum does not go in, and the stirring cannot be stirred, which seriously affects the copper dissolving speed.
Some of the exhaust fans are made of 316L materials, some are made of epoxy FIBERGLAS, some are made of PP or PVC and other materials, according to years of production experience, the exhaust fan is placed indoors, with the material can be, placed outdoors or with FRP is better, economical and practical, resistant to ultraviolet radiation.
3.5 Copper dissolved heating system
Copper dissolved liquid, whether it is high temperature copper dissolved or low temperature copper dissolved copper is generally provided with a heating system, the use of low temperature dissolved copper in the start of production or in the middle of the suspension of production and then start, the electrolyte must have a heating process, especially in the northern winter temperature in minus thirty degrees, the total system heat loss is extremely large, no heating can not guarantee production, the temperature of raw materials copper is in minus tens of degrees, put into the copper dissolved tank, the temperature in the tank will drop a lot, the copper dissolving speed will immediately drop. Therefore, the use of how high copper dissolved temperature should be adapted to local conditions, and the design of electrolytic copper foil also requires local meteorological data.
Copper dissolving production can normally be heated without heating, which is related to what geometric raw materials are used to dissolve copper, such as: the use of 1---3 mm thick copper wire, the use of honeycomb copper oxide blocks, flakes of small "copper flowers", can not be used for heating devices. The surface area of the raw material is very large, and the area of various reactions is very large, resulting in a very fast reaction speed of copper dissolving, and the temperature of the copper dissolved liquid rises rapidly. This is also the conservation of energy, if you spend money to deal with reasonable raw materials, there is no need for heating; if the raw materials are not processed, the rest of the money has to be boiled copper for heating.
Figure 3-6 copper dissolved heating system
Copper dissolving boilers are mainly used to heat dissolved copper, some use 95 degrees hot water, some use steam, as long as the desired copper dissolving speed can be achieved. The way of copper dissolving heating should also be determined according to the conditions of the region, if the local electricity price has an advantage in the available electric boiler, such as the local oil quantity oil price has an advantage in the available oil boiler, such as the local coal carbon has the advantage of using coal-fired boilers, such as the factory near the thermal power plant or geothermal resources and other heat sources, can be used, local materials.
3.6 Selection of copper dissolving process parameters
The selection of copper dissolving process parameters is a very critical issue, it is not only a guarantee of product quality, but also an economic and technical indicator, which is of great significance for saving energy, reducing consumption and maximizing the function of the equipment. Process parameters are directly related to production capacity and production equipment. The determination of process parameters depends on a variety of factors cooperating with each other, and the electrolytic cell (anode), cathode roller material, structure, polar distance, electrolytic current, electrolyte flow rate, electrolyte transition accuracy, additives, raw material geometry and size, cloth method, wind supply form capacity, copper dissolving temperature, etc. are closely related, mainly mutual cooperation. The end result is to ensure the production of the best copper foil and the best economic benefits for the enterprise.
3.7 Copper dissolving process parameter selection
Table 3-1 provides three commonly used copper dissolving process parameters for selection.
Table 3-1 Three commonly used copper dissolving process parameters
<col>
A
B
C
Copper dissolving tank import Cu++
g/l
100±2
90
100
Copper dissolved can outlet Cu++
125
130
The temperature of the liquid in the copper dissolved tank
℃
60
80
Wind pressure inside the copper dissolving tank
kg/cm2
1
≥1.2
≥1.5
The amount of solution cycle
m3/h·罐
50
20
15
Copper dissolving tank import H2SO4
90±2
105
Copper dissolving tank outlet H2SO4
70±2
65