Table information content source: Tsinghua University "Product Modeling Design", Beijing Institute of Technology "Product Modeling Materials and Processes"
Table 1 Plastic properties — recommended types table
Table 2 Properties and uses of commonly used thermoplastics
Table 3 Properties and uses of commonly used thermoset plastics
Table 4 Combustion characteristics of plastics
Table 5 Density, hue, heat resistance temperature and formability of plastics
Table 6 Recommended values for the release slope of commonly used plastics
Table 7 Shrinkage rate of commonly used plastics
Table 8 Plastic process method selection reference
Table 9 Design guidelines for plastic processing process products
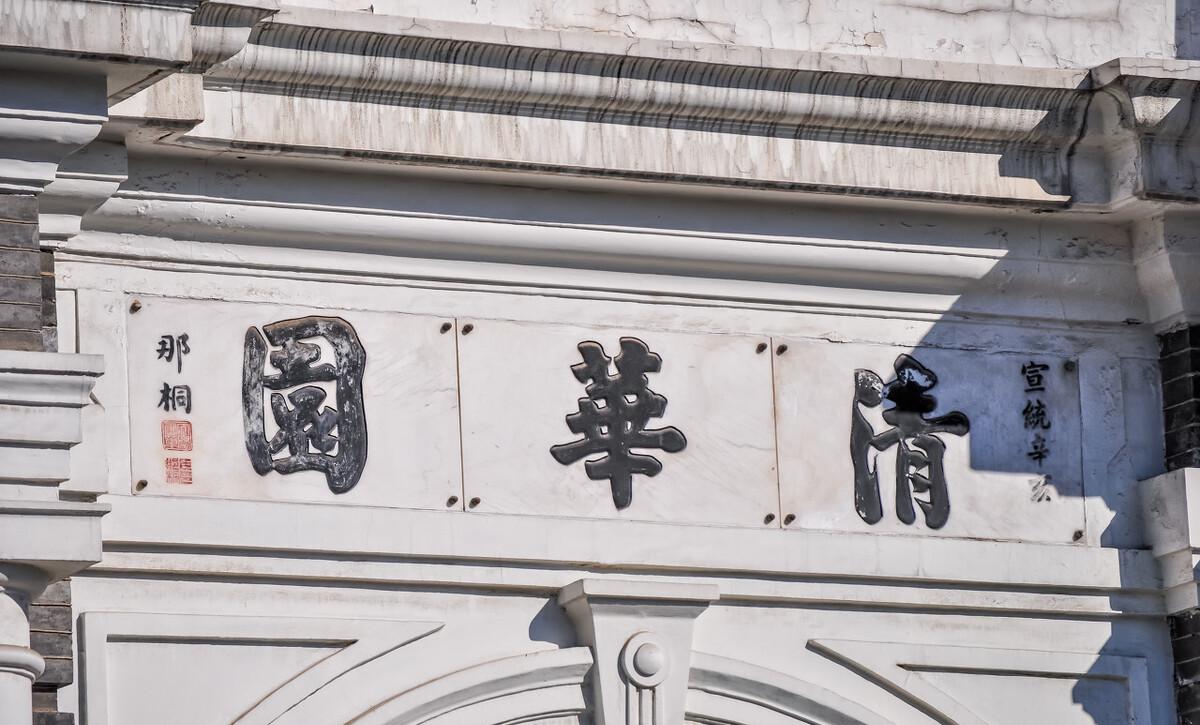
<h1 class="pgc-h-center-line" > Table 1 Plastic properties - Recommended table of types</h1>
<col>
performance
Recommended opinions
High abrasion resistance
nylon
Low cost-to-quality ratio
Urea formaldehyde, phenolic, polystyrene, polyethylene, polypropylene, PVC
compressive strength
Polyteraphthalamide, glass fiber reinforced phenolic, epoxy, melamine, nylon, glass fiber reinforced thermoplastic polyester, polyimide
Low cost-to-volume ratio
PE、PP、脲醛、酚醛、PS、PVC
High dielectric constant
Phenolic, PVC, fluoroplastics, melamine, allyl plastics, nylon, polybenzamide, epoxy
High dielectric strength
PVC, fluoroplastics, PP, polyphenylene ethers, phenolics, thermoplastic polyesters, glass fiber reinforced nylon, polyolefins, PE
High loss factor
PVC, fluoroplastics, phenolic, thermoplastic polyester, nylon, epoxy, allyl terephthalate, polyurethane
Good bearing deformation resistance
Thermoset laminates
High modulus of elasticity
Melamine, urea, phenolic
Low modulus of elasticity
PE, PC, fluoroplastics
High resistance
PS, fluoroplastics, PP
High elongation at break
PE, PP, silicones, ethyl hexenoate
Low elongation at break
PES, glass fiber reinforced PC, glass fiber reinforced PP, thermoplastic polyester, polyetherimide, vinyl ester, polyetheretherketone, epoxy, polyimide
Bending modulus (rigidity)
PPS, epoxy, glass fiber reinforced phenolic, glass fiber reinforced nylon, polyimide, diallyl terephthalate, polyterephthalamide, thermoplastic polyester
Bending yield strength
Glass fiber reinforced polyurethane, epoxy, carbon fiber reinforced nylon, glass fiber reinforced PPS, polyterephthalamide, PEEK, carbon fiber reinforced PC, etc
Low coefficient of friction
Fluoroplastics, nylon, polyoxymethylene
High hardness
Melamine, glass fiber or cellulose reinforced phenolic, polyimide, epoxy
High impact strength
Phenolic, epoxy, PC, ABS
High moisture resistance
PE, PP, Fluoroplastics, PPS, Polyolefins, Thermoplastic Polyesters, Polyphenylene Ethers, PS, PC (Glass Fiber or Carbon Fiber Reinforced PC)
Softening
PE, silicones, PVC, thermoplastic elastomers, polyurethanes, ethyl acetate
High tensile strength at break
Epoxy, glass fiber or carbon fiber reinforced nylon, polyurethane, glass fiber reinforced thermoplastic polyester, polytermethyleneamide, PEEK, carbon fiber reinforced PC, PEI, PES
High tensile yield strength
Glass fiber or carbon fiber reinforced nylon, polyurethane, glass fiber reinforced thermoplastic polyester, PEEK, PEI, polyterephthalamide, glass fiber or carbon fiber reinforced PPS
Low thermal conductivity
PP, PVC, ABS, PPO, polybutene, acrylic, PC, thermoplastic polyester, nylon
Low coefficient of expansion
Carbon fiber or glass fiber reinforced PC, glass fiber reinforced phenolic, carbon fiber or glass fiber reinforced nylon, glass fiber reinforced thermoplastic polyester, glass fiber or carbon fiber reinforced PPS, PEI, PEEK, polystabenamide, allyl plastic, melamine
Permanent high transparency
Acrylic, PC
Lightweight
PP, PE, polybutene, ethyl acetate acetate, ethyl methacrylate
The degree of whiteness is maintained to a high degree
Melamine, urea
<h1 class="pgc-h-center-line" > Table 2 Properties and uses of commonly used thermoplastics</h1>
name
(Code)
Main performance characteristics
Examples of uses
polyvinyl chloride
(PVC)
Rigid PVC has high strength, excellent insulation, good chemical stability, and strong resistance to acids and alkalis. It can be used at -15 °C ~ +60 °C, has good thermoforming properties, and has a small density
As a corrosion-resistant structural material, it is used in the chemical industry, such as oil pipelines, containers, centrifugal pumps, valve fittings
Soft PVC is not as strong as hard, but the elongation is larger, has good electrical insulation, and can be used at -15 °C ~ +60 °C
Insulated foreskins for wires and cables, agricultural films, industrial packaging. However, because it is toxic, it is not suitable for food packaging
Foam pvc is lightweight, heat insulation, sound insulation, vibration resistant
Foam polyvinyl chloride liner, packaging materials
polyethylene
(EP)
Low-pressure polyethylene is hard in texture, has good wear resistance, corrosion resistance and electrical insulation performance, and poor heat resistance, becomes soft in boiling water; high-pressure polyethylene is a lighter kind of polyethylene, its chemical stability is high, there is good high-frequency insulation, softness, impact resistance and transparency; ultra-high molecular weight polyethylene impact strength is high, fatigue resistance, wear resistance, cold compression casting molding
Low-pressure polyethylene is used to manufacture plastic plates, plastic ropes, gears, bearings, etc. with small loads; high-pressure polyethylene is the most suitable for blow molding film, hoses, plastic bottles and other products used in food and pharmaceutical packaging, ultra-high molecular weight polyethylene can be used as friction reduction, wear reduction parts and transmission parts, but also as wire and cable foreskin
polypropylene
(PP)
The density is small, and it is one of the lighter plastics commonly used. Strength, hardness, stiffness and heat resistance are better than low-pressure polyethylene, can be used for a long time at 100 ~ 120 °C, almost no water absorption, and has good chemical stability, excellent high-frequency insulation, and is not affected by temperature. However, the low temperature is brittle, not wear-resistant, and easy to age
Make general mechanical parts, such as gears, pipes, joints, etc.; make corrosion-resistant parts, such as pump impellers, chemical pipes, containers, insulators; make televisions, radios, fans, motors, etc
Polyamide (commonly known as nylon) (PA)
Tasteless, non-toxic; has high strength and good toughness; has a certain degree of heat resistance, can be used at 100 ° C. Excellent wear resistance and self-lubrication, small friction factor, good sound attenuation and oil resistance, water, oil and general solvent resistance; good corrosion resistance; antibacterial mold; good molding. However, the creep is larger, the thermal conductivity is poor, the water absorption is high, and the molding shrinkage rate is larger
Commonly used are nylon 6, nylon 66, nylon 610, nylon 1010 and so on. It is used to manufacture certain bearing and transmission parts that require wear resistance and corrosion resistance, such as bearings, gears, pulleys, screws, nuts and some small parts; it can also be used as a high-pressure oil-resistant sealing ring, and an anti-corrosion and wear-resistant coating on the metal surface
Polymethyl methacrylate (commonly known as plexiglass)
(PMMA)
Good transparency, can pass more than 99% of the sun' light; good colorability, has a certain intensity, resistance to ultraviolet rays and atmospheric aging, very corrosion resistant, excellent electrical insulation properties, can be used at -60 ~ +100 °C. However, the texture is brittle, soluble in organic solvents, the surface hardness is not high, and it is easy to scratch
Production aviation. Transparent parts in the instrumentation, automotive and radio industries, such as aircraft windows, lampshades, televisions. Radar screens, oil labels, oil cups, equipment signage, instrument parts, etc
Styrene-dibutene-acrylonitrile copolymer
(ABS)
Performance can be adjusted by varying the content of the three monomers. It has high impact toughness and high strength, excellent oil resistance, water resistance and chemical stability, high electrical insulation and cold resistance, high dimensional stability and certain wear resistance. The surface can be plated with metal, which is easy to process and form, but it is easy to lift the layer for long-term use
Manufacture of telephones, amplifiers, televisions, instruments, motor shells, gears, pump impellers, bearings, handles, pipes, tank linings, dashboards, car bodies, car armrests, etc
Polyoxymethylene
(POM)
Excellent comprehensive mechanical properties, good wear resistance, small water absorption, high dimensional stability, good coloring, good friction reduction and anti-aging, excellent electrical insulation and chemical stability, can be used in the range of -40 ~ +100 °C. However, heating is easy to decompose, and the molding shrinkage rate is large
Manufacture of anti-friction, wear-resistant transmission parts, such as bearings, rollers, gears, electrical insulation, corrosion-resistant parts and chemical containers
Polytetrafluoroethylene (also known as plastic king)
(F-4)
It can resist the corrosion of almost all chemicals; good aging resistance and electrical insulation, no water absorption; excellent resistance to high and low temperatures, which can be used for a long time at -195~250 °C; the friction factor is very small, and it has self-lubrication. However, it cannot be thermoforming, only sintering molding, decomposing harmful gases at high temperatures, and the price is higher
Make corrosion-resistant parts, anti-friction wear parts, seals, insulation parts, such as high-frequency cables, capacitor coil racks, chemical reactors, pipelines, etc
Polysulfone
(PSF)
Bisphenol A type: excellent heat resistance, cold resistance, weather resistance, creep resistance and dimensional stability, high strength, excellent electrical insulation, high chemical stability, can be used at -100 ~ +150 °C for a long time. However, the UV resistance is poor and the molding temperature is high
Manufacture high-strength, heat-resistant parts, anti-friction wear parts, transmission parts, such as precision gears, cams, vacuum pump blades, instrument housings and covers, heat-resistant or insulated instrument parts, automotive skid plates, dashboards, liners and gaskets, computer parts, electroplated metal made of integrated electronic printed circuit boards
Non-bisphenol A type: heat resistance, cold resistance, can work for a long time at -240 ~ +260 °C, high hardness, self-extinguishing, aging resistance, radiation resistance, mechanical properties and electrical insulation are good, high chemical stability. However, it is not resistant to polar solvents
Chlorinated polyethers (or polychlorinated ethers)
Extremely high chemical corrosion resistance, easy to process, can be used for a long time at 120 ° C, good mechanical properties and electrical insulation, low water absorption, dimensional stability. However, the low temperature resistance is poor
Friction reduction, wear-resistant transmission parts, precision mechanical parts, linings and coatings of chemical equipment made in corrosive media
polycarbonate
(PC)
Transparency up to 86% ~ 92%, use stability -100 ~ +130 °C, good toughness, impact resistance, high hardness, creep resistance, heat resistance, cold resistance, fatigue resistance, good water absorption. There is a tendency to stress cracking
Aircraft seat window covers, protective helmets, bulletproof glass and parts for mechatronics and instruments
Polyurethane plastic
(PUR)
Superior wear resistance, good toughness, high carrying capacity, hard and not brittle at low temperatures, ozone resistance, weather resistance, resistance to many chemicals and oils, radiation resistance, flammability. Soft foam has excellent high and low temperature insulation performance
It is used to make seals, transmission belts, thermal insulation, sound insulation and vibration-proof materials, gears, electrical insulation, solid tires, wire and cable sheaths, automotive parts
Phenolic plastic (commonly known as bakelite) (PF)
High strength, hardness and heat resistance, working temperature can generally be above 100 °C, under water lubrication conditions with a very small friction factor, excellent electrical insulation, good corrosion resistance (in addition to strong alkali), mold resistance, good dimensional stability. However, the texture is brittle, the lightfastness is poor, the color is dark, the molding processability is poor, and it can only be molded
Manufacture of general mechanical parts, water lubrication bearings, electrical insulation, chemical-resistant structural materials and lining materials, such as instrument housing, electrical insulation plate, insulating gear, fairing, acid-resistant pump, brake flat pads, etc
Epoxy plastic
(EP)
High strength, better toughness, excellent point insulation, waterproof, moisture-proof, mildew-proof, heat-resistant, cold-resistant, can be used for a long time in the range of -80 ~ +200 °C, good chemical stability, small shrinkage after curing and molding, strong adhesion to many materials
Plastic molds, precision gauges, mechanical instrument structural parts, electrical and electronic components and coil perfusion, coating and encapsulation, and repair of mechanical parts
Silicone plastic
It has high heat resistance and can be used for a long time at 180~200 °C. Excellent electrical insulation, good insulation for high voltage arc, high frequency, good moisture resistance, chemical resistance, radiation resistance, ozone resistance, but also low temperature resistance. But the price is more expensive
It is used for high-frequency insulation, motor and electrical insulation in humid tropical areas, perfusion and fixing of electrical and electronic components and coils, heat-resistant parts, etc
Poly-py-carboxybenzoate plastic
It is a new type of heat-resistant thermoset plastic. Can be used for a long time at 315 °C, short-term use temperature range of 371 ~ 427 °C, the thermal conductivity is extremely high, 3 to 5 times higher than the general plastic, has good wear resistance and self-lubrication, excellent electrical insulation, wear resistance and self-extinguishing
Abrasion-resistant, corrosion-resistant and dimensionally stable self-lubricating bearings, high-pressure seals, automotive engine parts, electronic and electrical components, and special-purpose fibers and films
<h1 class="pgc-h-center-line" > Table 3 Properties and uses of commonly used thermosets</h1>
characteristic
use
Phenolic
Electrical insulation, strength, heat resistance, acid resistance is good
Electrical communications, mechanical parts, coatings, adhesives
Urea formaldehyde
Colorless, easy to color, phenolic (water-resistant, heat-resistant), inexpensive
Hoods, buttons, utensils, wood glue, paint
melamine
Like urea-formaldehyde tree ester, it has great hardness and good water resistance
Decorative panels, utensils, electrical parts, paper fiber processing, coatings
furan
Good resistance to pharmaceuticals
Corrosion resistant material
Alkyd resin
Good adhesive, flexible and weather-resistant
paints
Unsaturated polyester
It can be molded at low pressure and reinforced with glass fiber
GFRP encapsulation
Diallyl phthalate
Can be low voltage molding, electrical insulation, dimensional stability, good heat resistance, high price
Electrical insulation materials, decorative panels
Epoxy
Good cementation with metals and inorganic substances, good electrical insulation and drug resistance
Adhesives, coatings, electrical insulation materials, FRP
Silicone
Electrically insulated, heat-resistant, water-repellent
Electrical insulation materials, lubricating oils, adhesive coatings
polyurethane
Strong elasticity, wear resistance, aging resistance (water resistance, alkali, hot water weak), good oil resistance
Foam damping materials, insulation materials, coatings, glues, artificial leather
< h1 class= "pgc-h-center-line" > the combustion characteristics of plastics in Table 4</h1>
Plastic name
Difficult to burn
Whether it is self-extinguishing after leaving the fire
Flame state
Plastic changes state
smell
Polymethyl methacrylate (PMMA)
easy
Continue to burn
Light blue, white at the top
Melt, lather
Strong smell of flowers and fruits, smell of rotten vegetables
( PVC)
difficult
Extinguish from the fire
Yellow, green at the bottom, white smoke
soften
Irritating acidity
Polyvinylidene chloride ( PVDC)
Hard
Yellow, green at the end
Special odor
polystyrene
( PS)
Orange-yellow, thick black smoke carbon bundle
Softens, lathers
Special, styrene monomer taste
Styrene acrylonitrile copolymer (SAN)
Yellow, thick black smoke
Softens, foams, is more scorching than polystyrene
Special, phenylacrylonitrile flavor
Acrylic-butadiene-styrene copolymer (ABS)
Yellow, black smoke
Soften, scorch
Special, styrene monomer smell rubber odor
(EP)
The upper end is yellow, the lower end is blue
Melt dripping
The smell of paraffin burning
( PP)
Oily taste
polyamide
(Nylon)
( PA)
Burn slowly
Slowly extinguish
Blue, yellow at the top
Melt dripping, foaming
Special, wool and nail burnt smell
( POM)
Strongly irritating formaldehyde smell, fishy smell
( PC)
Yellow, black smoke carbon bundle
Melt, foam
Special smell, smell of flowers and fruits
Polyether chloride ( CPS)
extinguish
Splash, yellow on the top, blue on the bottom, thick black smoke
Melt, do not grow
special
Polyphenylene ether
( PPO)
Thick black smoke
smelt
Flowers and fruits stink
( PSU)
Slightly rubbery flaming smell
Polytrifluorovinyl chloride (PCTFE)
Non-combustible
-
polytetrafluoroethylene
Cellulose acetate ( CA)
Dark yellow with a small amount of black smoke
Vinegar sour taste
Cellulose acetate butyrate (CAB)
Dingy taste
Cellulose propionate acetate (CAP)
Melt drips and burns
Propionic acid taste
Nitrocellulose ( CN)
Yellow
Fast and safe
Ethyl cellulose ( EC)
Yellow, blue at the top
Polyvinyl acetate (PVAC)
Dark yellow, black smoke
Polyvinyl butyl chloride ( PVB)
Black smoke
Phenolic resin
( PF)
Self-extinguishing
Yellow sparks
Cracking, color deepening
Strong formaldehyde smell
(wood flour)
Swelling, cracking
Wood and phenol flavor
Acidic resin
in Burki
Yellow, a small amount of black smoke
Cloth and phenol flavor
(Paper-based)
Yellow, a small amount of black smoke
Paper and phenol flavor
Urea formaldehyde resin
( UF)
Yellow, light blue at the top
Swelling, cracking, turning white at the site of combustion
Special odor, formaldehyde smell
Melamine resin
Pale yellow
Swelling, cracking, whitening
Polyester resin
burn
Slightly swollen and sometimes cracked
Styrene odor
Vinyl chloride-vinyl acetate copolymer (VC/VAC)
Dark yellow
<h1 class = "pgc-h-center-line" > Table 5 Density, Hue, Heat Resistance Temperature and Formability of Plastics</h1>
plastics
Density g/cm3
Hue
Heat resistant temperature /°C
Formability
quality
High density
0.94~0.97
Transparent ~ Opaque coloring range is wide
121
excellent
Low density
0.91~0.93
Translucent to opaque coloring range is wide
82~100
Non-padding
0.90~0.091
121~160
Impact resistant type
0.90~0.91
93~160
Vinyl chloride resin
Hard
1.35~1.45
Transparent to opaque (suitable) luminous 80% to 88%) coloring range is wide
66~79
Good ~ excellent
Soft
1.16~1.35
Transparent to opaque (80% to 88% of the light permeability) has a wide range of coloring
good
General (GP)
1.04~1.09
Transparent (82% to 92% transmittance) has a wide range of coloring
66~77
Impact Resistant (HI)
0.98~1.10
60~79
AS resin
1.075~1.10
Transparent (80% to 88% transmittance) has a wide range of coloring
60~96
ABS resin
Heat-resistant type
1.06~1.08
89~110
General impact resistant type
1.05~1.07
71~93
acrylic resin
Formed products
1.17~1.20
Transparent (light transmittance of more than 92%)~Opaque coloring range is wide
60~93
20% to 40% glass fiber filling
1.17~1.52
149~210
Nylon 6
1.12~1.14
79~121
No padding
1.2
Polyacetal
Homopolymers and copolymers
1.41~1.43
Translucent cream coloring ranges widely
85~104
Saturated polyester
No fillers
1.31~1.38
50~121
Fiberglass filling
1.48~1.67
Opacity shading is wide-ranging
121~260
Fluororesin
Polytrifluorovinyl chloride
2.1~2.2
Transparent to translucent coloring range is wide
177~199
Can be ~ good
Vinyl acetate copolymer
0.92~0.95
transparent
—
Cellulose resin
cellulose acetate
1.22~1.34
60~104
Artificial resin
Cellulose acetate butyrate
1.15~1.22
Wood flour and cotton block filling
1.32~1.45
Opaque, generally black, brown and other dark colors
177~182
Asbestos filled
1.45~1.9
177~260
Urea-formaldehyde resin
a- Cellulose filling
1.47~1.52
Transparent ~ opaque shading range wide range of vivid colors
77
Melamine resin
99
Unsaturated polyester resin
To form, cut the rough spinning
1.35~2.3
149~177
Mixed glass fibers
1.8~2.3
Weaving
1.50~2.1
For hard injection molding
1.10~1.46
epoxy resin
1.60~2.0
Translucency ~ Opaque shading range limit
149~260
1.68~2.0
<316
Injectable liquid carbamate
1.05~2.5
Transparent ~ Opaque shading range limit
88~121
<h1 class="pgc-h-center-line" > the recommended values of mold release slope of commonly used plastics in Table 6</h1>
Types of plastics
Release slope
Thermoset plastic compression molding
1°~1°30′
Thermosetting plastic injection molding
20′~1°
Polyethylene, polypropylene, soft PVC
30′~1°
ABS, modified polystyrene, nylon, polyoxymethylene, chlorinated polyether, polyphenylene ether
40′~1°30′
Polycarbonate, polysulfone, hard PVC
50′~1°30′
Transparent polystyrene, modified plexiglass
<h1 class= "pgc-h-center-line" > the shrinkage rate of commonly used plastics in Table 7</h1>
Shrinkage/%
High pressure polyethylene
1.5~3.5
Low pressure polyethylene
1.5~3.0
1.0~3.0
Glass fiber reinforced polyethylene
0.4~0.8
Rigid PVC
0.2~0.4
Soft PVC
General purpose polystyrene
0.2~0.8
Heat-resistant polystyrene
0.7~1.5
Nylon 66
1.0~2.5
Nylon 610
Nylon 1010
0.5~4
30% glass fiber filled nylon 6
0.35~0.45
0.5~0.7
2.0~3.5
Glass fiber reinforced polysulfone
0.4~0.7
Impact resistant ABS plastic
Heat-resistant ABS plastic
0.4~0.5
30% glass fiber reinforced ABS plastic
0.1~0.15
Wood flour filled with phenolic plastic
0.5~0.9
Asbestos filled phenolic plastic
0.2~0.7
Glass fiber reinforced phenolic plastic
0.05~0.2
<h1 class="pgc-h-center-line" > the reference for plastic process method selection</h1>
<h1 class="pgc-h-center-line" > Table 8 Plastic Process Method Selection Reference</h1>
Note: Estimation of product cost: raw material cost× factor = product cost. The coefficient is usually 1.5 to 10
Process name
illustrate
Main advantages
limit
Cost factor
Blow molding
The heated thermoplastic extrusion tube is placed between the two halves of the open mold, and gas pressure is applied so that it expands against the closed mold side wall, opens the mold, and ejects the product
It can reduce the cost of tooling molds, improve production efficiency, and mold hollow, complex shape products
Wall thickness and tolerances are difficult to control
1.5~5
2~3
Thermoforming
(Blister molding)
The heated softened thermoplastic plate is placed on the male or negative mold, and the air between the plate and the mold is discharged, so that the plate is attached to the outer surface of the mold. Its molding methods mainly include vacuum method, rapid recovery method, occlusion auxiliary method and cover molding method
Tooling mold cost is low, can produce large thin-walled products, batch small products production economy is good
Produce products with simple shapes, small material selection and extremely high scrap rates
2~10
3~5
Injection molding
The thermoplastic or thermosetting molding compound is heated and plasticized in a barrel that can control the temperature, and under pressure, it enters the gate, runner through the nozzle, and then enters the mold cavity, and after rapid curing, the mold is opened and the product is ejected. In the improved process, no runner molding, the runner is part of the cavity
The production efficiency is extremely high, the unit price of each product is low, the surface quality is good, the dimensional accuracy is high, and the products with large structures and complex shapes can be produced
Tooling mold cost is high, not suitable for small batch production
Calendering
The dough-type thermoplastic is melted into a plate of uniform thickness by series heating or cooling roller rolling. Can also be used to laminate plastic overlays onto the back of other materials (e.g. artificial leather)
Costs can be reduced, and there is no stress in the mold of the sheet material. That is: in an isotropic state
Do not form very thin films
1.5~3
2~2.5
Pouring forming
Liquid plastics (usually thermosets other than acrylics) are poured into the mold, cured and molded (without pressure), and released from the mold after molding. Thermoplastics are deposited in the form of a solution or hot melt to a support surface with a high degree of polishing to make a thermoplastic film.
Can reduce the cost of molds, can produce thick section of large products, product surface quality is good, suitable for mass production
Limited to molding products with a simple shape, in addition to forming the casting film, mass production is very uneconomical, and the vast majority of thermoplastics are not suitable for this production process
Compression molding
Usually after pre-molding with thermoplastic resin or partially polymerized thermoset resin, the material is placed into a heated cavity, molded, and heated and pressurized, so that the material flows and fills the cavity, heating it to fully polymerize, open the mold, and remove the product. This process can sometimes be used to mold thermoplastic products, such as vinyl plastic record player discs
Less waste, low cost, can prepare large products
It is not suitable for the manufacture of extremely complex products, including those with grooves, side cores, small holes and fine inserts. It is difficult to produce products with extremely small tolerances
Cold working molding
The same as compression molding, is also the material into the combination mold, the difference is only pressurized, not heated, the product is cured in the oven. Some thermoplastic sheets or blanks can be stamped with metal. Using this process method, ethylene short gun housings can be prepared
Can be molded large products, simple process, low cost, high production efficiency
It is limited to the processing of products with relatively simple shapes, and only a few plastics are suitable for this process
Extrusion molding
The thermoplastic or thermoset molding compound is loaded into the hopper and then into the barrel, where it is heated, plasticized, and pushed forward by screw placement and through a nozzle with the desired cross-sectional configuration
The mold cost is low, a variety of armed plastic materials can be molded, the production efficiency is high, and the coating or housing sleeve is applied to the core material (such as metal wire).
The production of parts with uniform cross-sections is limited
2~5
3~4
Long fiber winding molding
The roving long fibers (fiberglass) are first impregnated with resin and mechanically wound onto a mandrel similar in shape to the desired part. Wound in one amount, place the mandrel and the product in an oven to cure /then remove the mandrel from the mandrel hole at one end of the part
In the direction of the required strength, the high-strength fibers are precisely oriented, and the resin distribution in the final product is very uniform in addition to the strength/mass ratio
The shape of the sinusoidal curvature is limited, and both the opening and the hole will reduce the strength of the product
5~10
6~8
Lamination molding (high pressure)
Reinforcing materials such as reinforcing cloth, paper, foil, etc. are pre-impregnated or sprayed with thermoplastic or thermosetting resins, and molded into sheets, rods, pipes or other simple shape profiles at a pressure of 1000lbf/in2
The final product has excellent dimensional stability, mass production, and very good economy
Tooling molds are expensive and limited to the production of products with simple shapes and sections
Double mold molding
This is a commonly used compression molding method, which uses two metal molds with a compact installable compressible area in the mold to seal the molding compound and trim the reinforcement. The reinforcing material is usually made of fiber felt or preformed blank, which is placed in the mold, molded, heated, and pressurized (pressure is 150 to 400lbf/in2). After the product is formed, open the mold and remove the product
High production efficiency, good product quality, good repeatability
Molds and equipment are heavily invested, and products often require post-sequential surface treatment, such as sandblasting
Rotational molding
A predetermined amount of thermoplastic or thermoset resin powder or solution is poured into the mold, mold closed, heated, rotated on a two-plane axis until the contents are attached to the inner wall of the mold, the mold is opened, and the product is removed
Low processing cost, can produce large-scale air core products, molded products for isotropic structure
Limited to the production of individual core products, generally speaking, its production efficiency is low
Hollow casting molding
The thermoplastic powder or solution is poured into the mold, the mold is closed, heated to a predetermined time, it can achieve partially cured materials adhered to the mold wall, and then open the mold, the non-polymerized material is poured out, and the semi-melted products are removed from the mold and polymerized and cured in the oven
The mold cost is very low, and the economy is good for small batch production
Restrict the production of long-space core products, the production efficiency is very low, and the selection of raw materials for processing is restricted
1.5~4
Transfer molding
The thermoset molding compound is fed from the hopper into the transfer box, heated and plasticized, and then, the plunger is used to feed into the cavity through the closed mold gate and runner, cured and formed, and then the mold is opened and the product is ejected
Product size accuracy is good, production efficiency is high, can produce complex shape of the product
The mold cost is high, the raw material waste at the gate and the flow place is serious, and the size of the product is more restrictive
Hand paste molding
(FRP)
Several layers of reinforcing material (commonly used glass cloth) and thermosetting resin are placed on the mold, and rolled with a roller so that it attaches to the outer surface of the mold, and then placed in the oven for pressure-free curing. The improved form of the process is jet molding, in which the resin system is sprayed to the surface of the mold with a spray gun at the same time as the shortened fibers, and compacted with rollers, and the hand paste is usually pressurized and cured in a vacuum bag, pressure bag, or high-pressure tank
Low processing cost, can produce large parts, suitable for the production of small batches of products
Mass production costs do not decrease, and the uniformity of resin distribution is difficult to control, and it is limited to the production of products with simple shapes
<h1 class="pgc-h-center-line" > Table 9 Design guidelines for plastic processing process methods</h1>
Design rules
Blow molding
Pour molding
Compression molding
Primary shape characteristics
Hollow housing
Simple form factor
Molding on a flat surface
Unchanged cross-sectional profile material
Unlimited
Finite size factor(1)
M
ME
Minimum Inner Diameter/in
0.125
0.01~0.125
Bottom cut
be
not
Slope (Min) (°)
0~1
>1
not applicable
<1
Minimum thickness /in
0.01
0.001
0.015
Maximum thickness /in
>0.25
not
0.5
6
1
Inserts
available
Assemble cores
Yes
No
Mold the inner hole
Set up a boss
Stiffeners
In-mold design and design number
Overall dimensional tolerances/(in/in)
±0.01
±0.001
±0.005
Surface Treatment(2)
1~2
2
Set the thread
Reinforced plastic molding
Rotational molding
(Blister)
Transfer molding
Double mold molding
Long fibre winding
Rotate the surface structure
MS
WE
0.25
0.06
0.03
0.02
0.002
3
±0.02
4~5
5
1~3
concentrate:
(1) Finite size factor: M represents the material; ME represents the molding equipment; MS represents the molding size; WE represents the winding equipment.
(2) Surface treatment: the range is set to 1 to 5 levels, 1 means very smooth; 5 means rough. #
#Designer ##Design##Craft##Discipline##大学 #