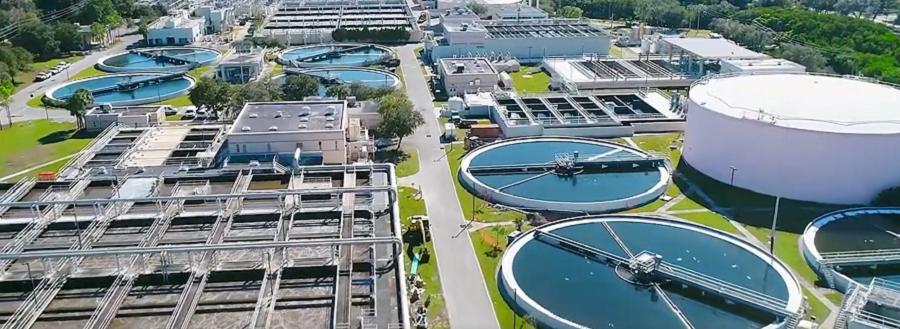
Core stuff (public number: aichip001)
Compile the | Sing
Edit | Panken
Core East and West August 31 news, China's Taiwan region this year can be described as an eventful autumn, the new crown pneumonia epidemic has not been solved, just survived a century of severe drought, and is facing flood disasters. Even Taiwan's largest wafer factory, the world's chip foundry brother, and the island's largest water and electricity company, TSMC, which has been hit by natural disasters, has not been affected by the crisis, and even the new plant built in Arizona, which has also suffered a severe drought, has not been affected by the current construction plan.
Behind this, TSMC's enterprise risk management measures have been honed for many years. According to the Austrian data company World Data Lab, 2.4 billion people already live in water-poor areas. The United Nations also noted that water scarcity will displace 700 million people by 2030. Globally, water shortage crises are frequently staged, and early warning and prevention of these sudden disasters have become a must for major semiconductor manufacturers.
Through a recent article published by Arthur Chuang, senior director of TSMC's facilities department, we distilled the key points of TSMC's treatment of water shortages and TSMC's green manufacturing measures to see how "cut" TSMC's water use is.
<h1 class="pgc-h-arrow-right" data-track="5" > First, fabs use more than 15,000 litres of water per day, and the task force addresses water supply risks</h1>
At a global core shortage, water is one of the basic elements of chip manufacturing. According to Water Technology, a U.S. water treatment equipment maker, a fab needs to consume 20 million gallons to 40 million gallons (about 75.7 million liters to 150 million liters) of water per day to clean silicon wafers and cool equipment. If water shortage occurs, it will seriously affect the production capacity of chip manufacturers.
Therefore, in order to avoid the risk of water shortage, TSMC has long established an enterprise risk management system that includes water supply risks.
TSMC also has a Climate-Related Financial Disclosure Task Force (TCFD) to identify climate-related risks. For different stages of water shortage, TSMC has set up different reaction procedures to deal with the shortage.
With the advancement of semiconductor technology, the materials and processes of chip manufacturing are more complex, and many chemicals are important raw materials for chip manufacturing, which greatly increases the requirements of fabs for water quality and quantity.
In such a situation, every drop of water is precious. Arthur Chuang said that regardless of the water saving effect, TSMC cannot ignore any opportunity to save water.
▲TSMC's daily water use and available water resources comparison (Source: EE Times)
<h1 class="pgc-h-arrow-right" data-track="12" > second, avoid the use of toxic solvents, 150 fireflies set up a fab</h1>
Arthur Chuang writes that water consumption is a separate issue of fab energy consumption. If green manufacturing is to be achieved, fabs need to adhere to high standards in energy management and wastewater discharge.
Specific to the fab interior, TSMC has established an energy management system within the entire fab, in which TSMC uses more efficient IE3 and IE4 motors and heat recovery equipment, which can accurately understand the energy consumption of each facility.
At the same time, TSMC began to reduce or avoid the use of toxic solvents in wafer production. According to Arthur Chuang, TSMC no longer uses NMP (N-methylpyrrolidone) solvents in wafer cleaning. The solvent is highly selective and stable, and is often used as a cleaning agent in high-precision electronics, circuit boards or lithium batteries, but it has certain toxicity to the human body and the environment.
To protect water sources, TSMC also has a wastewater discharge separation system that operates according to the characteristics and concentration of wastewater, and prohibits the use of any chemicals that cannot be naturally decomposed or removed from the water.
▲TSMC water treatment tank (Source: TSMC)
With such efforts, TSMC's environmental protection strategy has achieved certain results. TSMC Fab 15 is located at the foot of Dadu Mountain in Taichung and is more suitable for the natural environment. Fab 15 received its Platinum Certification from the AWS Standard for Sustainable Water Management in 2020, making TSMC the first semiconductor company in the world to receive AWS Platinum certification for two consecutive years.
Because the growth of fireflies has high environmental requirements, especially the cleanliness of water resources is quite important for their adults. In July 2020, the first aquatic yellow firefly was found at TSMC's Fab 15 plant, and as of the end of February 2021, more than 150 Lusheng window fireflies had been cultivated in Fab 15. The emergence of these small lives affirms TSMC's maintenance of the fab environment.
Fireflies in TSMC Fab 15 (Source: TSMC)
<h1 class="pgc-h-arrow-right" data-track="21" >3, the reclaimed water plant is running this year, and can recover 5,000 cubic meters per day</h1>
Water treatment and recycling is an important part of TSMC's water conservation, and 85%-90% of the water sources currently used by TSMC are reclaimed water.
Last year, TSMC's reclaimed water plant in Taiwan's Science Park in southern Taiwan started construction and is scheduled to be put into use this year to recycle factory wastewater and replenish urban water. The reclaimed water plant is the first private water plant in Taiwan. If the water plant is built, it can recover 5,000 cubic meters of water per day; by 2023, TSMC expects to recycle 20,000 cubic meters of water per day.
▲Schematic diagram of TSMC reclaimed water plant and Fab 6, Fab 14 and Fab 18 (Source: TSMC)
In Arizona, USA, TSMC has also worked closely with local municipalities and ecosystem partners to ensure the sustainable development of water resources.
In TSMC's promotional video, all of the fab's water flows through the pipeline without allowing it to evaporate. In the fab, TSMC installed nine recirculation systems and 13 types of water treatment equipment.
▲TSMC fab internal water resource pipelines (Source: TSMC)
As a result of these efforts, TSMC's industrial wastewater recovery rate is 85%, and the utilization rate per drop of water is more than 350%, which means that the average drop of water is used by TSMC 3.5 times.
Each year, TSMC outlines its implementation plan and results such as environmental protection in its corporate responsibility report. At the individual level, its employees need to set their own environmental protection and habitat restoration goals, and the completion of these goals will be directly linked to the performance evaluation and motivation of employees, so as to encourage TSMC employees to be environmentally friendly.
<h1 class="pgc-h-arrow-right" data-track="30" > Conclusion: Emergency measures are in place, wafer capacity may be avoided from drought impacts</h1>
As the world's largest wafer foundry, TSMC has a market share of more than 50%. However, under the wave of global core shortage, there was a drought in Taiwan. Zhang Zhongmou, the founder of TSMC, once said that one of the advantages of building a fab in the United States is that there is plenty of water and electricity. Now, Arizona's drought has once again drawn attention to water for fabs.
At present, TSMC has taken many preventive and emergency measures in the face of drought, including water trucks to transport water, etc., to ensure the normal operation of the production line. Perhaps people can put aside the worries about the impact of drought on TSMC production for a while.
Source: EE Times, TSMC official website