Wen | Hengyang Tobacco Company Logistics Distribution Center Li Lihua Qiu Ling Deng Anjian
Abstract: With the continuous growth of the sales volume of heterotyped cigarettes in tobacco commercial enterprises, it has brought great difficulties to the rational loading of distribution vehicles, resulting in a decline in the loading rate of distribution vehicles and an increase in operating costs. This paper analyzes the reasons for the decline in the vehicle loading rate of cigarette distribution, gives countermeasures to solve the loading rate of delivery vehicles, and verifies the effectiveness of the implementation of countermeasures through the practice of Hengyang Tobacco.
Keywords: delivery vehicle, loading rate, cage truck
I. Introduction
In recent years, with the changes in the development environment of the tobacco industry, the conditions for relying on quantitative expansion to support rapid development no longer exist, the traditional development mode is difficult to sustain, and the tobacco industry has entered a new stage of building a modern tobacco economic system and promoting high-quality development. In order to meet the needs of different consumer groups, the continuous increase of various types of cigarette varieties with different sizes and shapes has brought great inconvenience to the sorting and distribution of cigarettes, especially to the rational loading of distribution vehicles, which has brought great difficulties, reduced the loading rate of delivery vehicles, resulting in an increase in transportation costs and waste of distribution resources. Taking Hengyang Tobacco Logistics and Distribution Center as an example, this paper introduces the research strategy of improving the loading rate of special-shaped cigarettes in cigarette delivery vehicles.
Second, the causes of the decline in the loading rate of delivery vehicles
The main factors involved in the loading of cigarettes in delivery vehicles are: loading personnel, special-shaped cigarettes and standard cigarettes. Therefore, the decline in the loading rate of delivery vehicles is mainly caused by several factors such as loading personnel factors (loading order, reserved space, loading tightness), special-shaped smoke factors (proportion of special-shaped cigarettes and special-shaped cigarette packing), and standard cigarette factors (the number of single packs is not a multiple of 5).
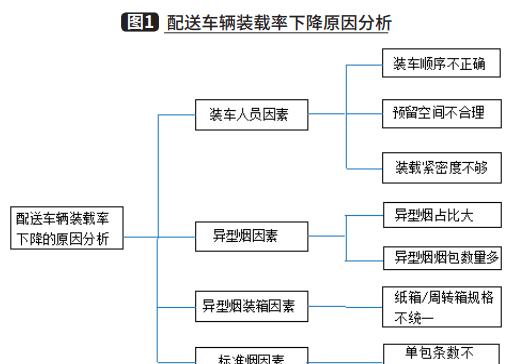
(1) Differences in cigarette loading order
The order in which standard cigarettes and special-shaped cigarettes are loaded directly affects the loading rate of vehicles. Years of practical experience show that the first installation of standard cigarettes and the subsequent installation of special-shaped cigarettes not only facilitate the delivery work of subsequent distributors, but also help to make full use of the loading space and improve the loading rate.
(2) The rationality of the reserved space
In the process of cigarette loading, whether the loading personnel can better grasp the reserved space, so as to meet the loading needs of the special-shaped cigarette box on the same day, and can load all the cigarettes that need to be distributed on the day, which directly affects the loading rate. If the reserved space is sufficient, the standard cigarette and the special-shaped smoke are matched as a whole, and there will be no situation that the special-shaped cigarette box or turnover box cannot be filled due to insufficient reserved space.
(3) The tightness of the cigarette loading
Whether the cigarette packs are stacked tightly and whether the effective space in the compartment is maximized under the premise of ensuring that the cigarettes are not crushed and squeezed out, has a greater impact on the cigarette loading rate.
(4) The proportion of special-shaped cigarettes in total sales
Due to its different shapes and wide ranges, special-shaped cigarettes have always been the focus and difficulty of loading vehicles. Practical experience and data show that the more special-shaped smoke, the more difficult it is to load, and the greater the impact on the loading rate of the vehicle.
(5) The influence of the number of special-shaped cigarette packs
In the case of a certain total amount of special-shaped cigarettes, if the average household order volume decreases, it means that the number of special-shaped cigarettes per pack decreases, and the total number of cigarette packs increases, thereby reducing the loading rate of delivery vehicles.
(6) The influence of special-shaped cigarette packaging specifications
In order to effectively ensure that the special-shaped smoke is not crushed and does not collapse in the carriage, Hengyang Tobacco currently adopts the special-shaped smoke packing method. After the special-shaped smoke wrap is packed, it is loaded into an empty carton or tote. However, due to the different shapes of special-shaped cigarettes and the instability of orders from each customer, when packing, only suitable cigarette boxes and tote boxes can be selected for loading based on experience.
(7) The number of standard cigarette packets
The tightness and regularity of a single pack of cigarettes also affects the loading rate of delivery vehicles. In the fully automated cigarette sorting line, the ideal state of the wrapping machine is that the number of cigarettes in the whole pack is a multiple of 5, so that the packaged cigarettes are both regular and compact, and it is not easy to appear irregular in shape and loose packaging. In practice, when customers order cigarettes, it is difficult to control the number of standard cigarettes ordered at multiples of 5 for various reasons, so that there will be random tail number cigarette packs such as 1-5, which wastes limited loading space.
In view of the factors of loading personnel and standard cigarette factors, Hengyang Tobacco has achieved good results after a certain degree of optimization. However, through long-term practice, it has been found that the crux of the decline in the loading rate of delivery vehicles is mainly that the sales volume of special-shaped cigarettes has increased more, accounting for more and more proportion of total cigarette sales, resulting in a decline in the loading capacity of bicycles and increasing the number of delivery vehicles.
Third, the impact of special-shaped smoke on the loading rate of distribution vehicles
In practice, the number of delivery vehicles is closely related to the proportion of special-shaped cigarettes. Special-shaped cigarettes have different shapes, and most of them are high-grade cigarettes, so when loading special-shaped cigarettes, they cannot be placed directly in the compartment like standard cigarette packs, but are installed in empty cartons or turnover boxes, on the one hand, they can protect cigarettes from crushing damage, on the other hand, it is convenient for cigarette packs to stack, easy to load, and it is not easy to collapse during the vehicle. However, the loading of special-shaped cigarettes through cartons or turnover boxes occupies the standard cigarette loading space, resulting in a significant decrease in the loading rate of vehicles. Hengyang Tobacco has observed after many experiments that when the total amount of cigarette distribution is close to the maximum loading capacity of the delivery vehicle, the proportion of heterogeneous cigarettes directly affects the number of delivery vehicles, and the proportion of heterogeneous cigarettes is close to or more than 8%, that is, it needs to be out of the car twice, resulting in an increase in distribution costs.
Fourth, the strategy of improving the loading rate of cigarette delivery vehicles
In actual work, in view of the problems of different specifications of special-shaped cigarette cartons or turnover boxes and low utilization rate of packing space, Hengyang Tobacco has shown through long-term experiments that the use of cage trucks to replace cartons and tote boxes to load special-shaped cigarettes can improve the loading rate of cigarette distribution vehicles by more than 10%.
1. Design and material selection of cage trucks
(1) The shape of the cage car
According to the daily loading habits, the space structure of the rear of the distribution car and the space requirements of the special-shaped smoke loading, the rectangular structure is the most appropriate, and the part close to the inside of the car is designed with a certain slope, so as to close to the inner wall of the carriage and maximize the use of internal space.
(2) The size of the cage car
For widely used IVECO distribution vehicles, the cage is available in 2 model sizes to make the most of limited space. One is 650 mm×350 mm×1500 mm, the other is 1050 mm×350 mm×1500 mm.
(3) The material of the cage car
Considering the frequency, durability and convenience of the use of cage trucks, the materials used must be lightweight, high strength, and good economy, and finally determine the use of high-strength aluminum alloy materials.
(4) The structure of the cage car
The cage car as a whole is divided into 3 independent areas, with a movable door on the outside and movable brake wheels on the bottom.
2. Loading of special-shaped smoke
Similar to standard cigarettes, the sorting order of special-shaped cigarettes follows the principle of first to be divided, that is, the distribution order is sorted first by the last customer and stacked on the lowest level when loading.
The interior of the cage car is divided into three areas, with 5 or more special-shaped cigarette packs (cigarette packs that need to be stacked) in the two areas on the left, and 4 or less cigarette packs (cigarettes placed side by side) in the right area.
When loading, the cigarette packs are stacked one by one in the sorting order from bottom to top, and after one area is full, the second area is stacked.
3. The load capacity of a single cage truck
According to the test calculation, when the three storage areas of the cage truck are all filled, the full load of the small cage car is about 450, and the full load of the large cage car is about 600.
4. Cage truck loading
After sorting, cage trucks filled with special-shaped cigarettes are placed in the staging area and then pushed by the loader to the side of the delivery vehicle.
Because the bottom surface of the delivery car is higher than the loading and unloading platform and has a certain spacing, the cage car cannot be pushed directly into the delivery car car. At this time, manual assistance is required to load the car, first to raise the front of the cage car, and then to raise the rear after the front part enters the carriage, until the entire cage car is pushed into the predetermined position of the carriage.
5. Fixing of cage trucks
The four self-locking wheels in the lower part of the cage truck are used for preliminary fixation, and the locking pedal is pressed after the cage truck is loaded into the delivery truck to prevent the wheels from rolling.
In advance, a welded with hole fixing block is added to the body wall of the car, and after the fixing piece on the cage car is aligned with it, it is fixed with a latch to ensure that the cage car does not move or rotate sideways.
6. Problems in the trial process
(1) Internal structure problems
The original design of the cage car sub-area to place special-shaped cigarettes, although it can better distinguish between large packs of cigarettes and small packs of cigarettes, easy to deliver the work, but the loading of the car is not very convenient, encounter the packaging defects of the special-shaped cigarette pack, the loading will be more difficult, but also affect the loading efficiency.
(2) External structure problems
The single-door mode is not easy to load and unload, the cigarette pack is easy to collapse when it is stacked high, and it is inconvenient to find cigarettes for specific customers when shipping; at the same time, the spacing of the side partitions is too small, which increases the weight of the car body.
(3) Wheel self-locking problem
The wheel diameter of the trial cage truck is 25 mm, which is not wear resistant and has poor self-locking. During the driving process of the vehicle, when the body shakes greatly, the self-locking blade will automatically bounce up, and the cage wheel cannot be locked.
(4) Cage car material problem
The selection of 0.5 mm thick alloy aluminum, although it reduces the weight of the cage car, but because the profile is too thin, the load-bearing capacity is poor, and over time, some positions will produce deformation and poor durability.
(5) Cage truck fixation problem
The use of latch fixing method, although the operation is simple, easy to load / unload the cage car, but also to prevent the cage car lateral displacement and rotation, but because there is a certain gap between the latch and the mating hole, resulting in vehicle bumps, the latch is easy to fall off from the mating hole, resulting in cage car fixation failure.
7. Improvement of cage cart
(1) Improvement of cage car materials
The material still chooses alloy aluminum, which has the characteristics of rust resistance, durability and light weight, and the thickness is increased from 0.5 mm to 0.8 mm, which can fully meet the stiffness of special-shaped smoke loading.
(2) Improvement of the internal structure of the cage car
Cancel the area partition, broaden the utilization rate of the internal space, facilitate the simultaneous loading of multiple cigarette packs, improve the loading efficiency, and also prevent the extrusion deformation when loading the special-shaped smoke.
(3) Improvement of the external structure of the cage car
From a single-layer door structure to a double-layer door structure, it is easy to load and ship. The spacing between the partition columns on the sides has been increased from the original 50 mm to 100 mm, effectively reducing the use of materials and the weight of the cage car.
(4) Improvement of cage wheels
The wheel diameter was increased from 25 mm to 40 mm, while the thickness of the self-locking plate was increased to improve cage locking performance.
(5) Improvement of cage car fixing method
The original straight hole latch fixing method is changed to a bolted connection, and the thickness of the joint parts is increased to prevent the cage car fixing sheet from being torn and damaged; at the same time, the position of the cage car fixing piece is adjusted to the bottom of the body wall fixing block, and the body wall fix block is used to further limit the amplitude of the cage car up and down, thereby ensuring the stability of the cage car.
8. Analysis of the effect of cage truck implementation
From September to October 2021, all 7 distribution vehicle groups at this level of Hengyang Tobacco Logistics Center adopted the cage truck loading heterogeneous smoke scheme, compared with the data of 3-8 months before the cage truck loading, the results showed that the loading rate of heterogeneous cigarettes in each vehicle group was improved to a certain extent, and the implementation effect was obvious.
5. Conclusion
The use of cage trucks to load special-shaped cigarettes improves the loading rate of cigarette distribution vehicles, reduces the number of delivery vehicles, and reduces the cost of cigarette distribution; at the same time, reduces the use of cartons or turnover boxes, in line with the development requirements of "green logistics" in the tobacco industry; can also effectively improve work efficiency, reduce the operation time of distribution vehicles, and achieve significant economic and social benefits.
END
Strategic cooperation