Due to the simple structure of automotive bearings, the difference in appearance is often not obvious. However, a look at the technical characteristics of bearings from the 1980s to the present can be seen: the basic performance of bearings continues to evolve in anticipation of market demand. This article describes the latest developments in automotive bearing (deep groove ball bearings, tapered roller bearings) technology in terms of low fuel consumption (low torque).
1 History of automotive bearings
1.1 Deep groove ball bearings
To meet the market demand for highly efficient multistage automatic transmissions and stepless transmissions, the functionality of deep groove ball bearings, mainly used in transmissions, has been improved, including in applications with high speeds and low torques. In addition to the requirements of compactness, lightweight and long service life, the drive motor bearings of electric vehicles also face similar technical requirements.
The requirements for low torque and compact, lightweight designs are achieved through changes in materials, heat treatments, internal design parameters, and improvements such as seals, cages, and greases (Fig. 1).
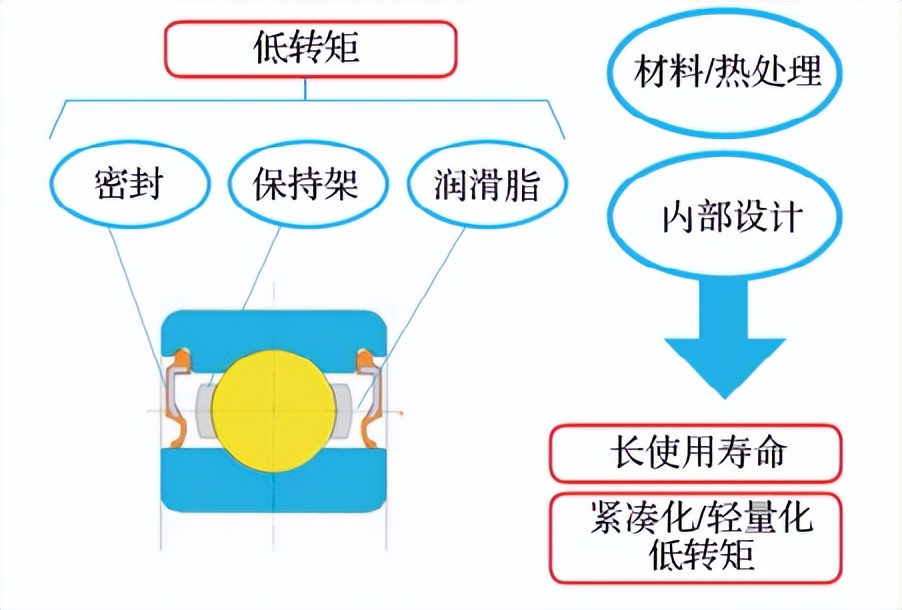
Fig. 1 Deep groove ball bearings and their characteristics
The structural and performance characteristics of the different types of deep groove ball bearings are shown in table 1. By comparing the torques, the technical history of deep groove ball bearings since the 1980s is shown in Figure 2.
Table 1 Characteristics of deep groove ball bearings
Figure 2 The development and change of deep groove ball bearings
Deep groove ball bearings for transmissions are usually open bearings without a shield or seal. However, contact seals (LU/LH seals) are currently used to prevent hard foreign matter from entering the lubricating oil and result in reduced bearing service life.
Due to the effect of the sliding characteristics of the seal, contact sealed bearings have a higher torque than open bearings. Therefore, open bearings are often used where low torque is a key requirement. Improvements in materials and heat treatment technology have resulted in longer service life of bearings under environmental conditions of foreign object intrusion.
The newly developed LE seal improves the sealing material and sealing lip structure, ensuring sealing performance while achieving low torque. These improvements make LE seals as low in torque under oil-lubricated conditions as non-contact seals.
1.2 Tapered roller bearings
Tapered roller bearings for transmissions or differentials have more design elements than deep groove ball bearings. Therefore, explore the various characteristics of these design parameters. In addition to the low torque, the material and heat treatment improvements also achieve a long service life (fig. 3).
Fig. 3 Tapered roller bearings and their characteristics
This section discusses the transition from internal design and material/heat treatment improvements to lower torques. In order to improve the internal design, the ST series was established to reduce the torque by improving the roller sliding characteristics. This is mainly achieved through the special shape and processing of the flange of the inner ring. In terms of material/heat treatment improvements, special heat treatment has been carried out with carburized steel as the base. Due to this special heat treatment technology, residual austenite on the raceway surface is increased, which helps to extend the service life. The calculation result of the compaction affecting torque is shown in Figure 4.
Fig. 4 The development of tapered roller bearings
With the improvement of the micro-curvature (convexity) of the inner/outer ring raceways and the combination of this technology with other material/heat treatment technologies for product development, the ECO-Top series was obtained. In addition, changing the steel cage design can significantly reduce the agitation resistance of the lubricating oil. In the latest series, automotive ULTAGE tapered roller bearings meet the needs of modern hybrid/electric vehicle (HEV/EV) lightweight and compact applications through improved convexity design and the establishment of batch machining technology. ULTAGE® is the NTN that combines "ultimate" and "stage" (a variety of uses for a range of bearings) to name bearings. In addition, ULTAGE® is also a general term for the new generation of bearings that NTN is known for its industry-leading performance.
In addition, based on globally available bearing steels, the long-life heat treatment "FA process" has been developed. Compared to the standard series, ULTAGE tapered roller bearings offer longer service life and significantly reduced torque (fig. 4). Improvements such as the optimization of the contact stress distribution mentioned later help to extend life.
2. Introduction of next-generation automotive bearings
Next, we will introduce the next generation of deep groove ball bearings for low fuel consumption vehicles and the newly developed tapered roller bearings.
2.1 Ultra-low friction sealed ball bearings
To prevent the harsh environment of hard foreign matter in the transmission lubricant from reducing bearing service life, contact seals are often used to improve the ability to resist foreign bodies, such as abrasive particles from gears. However, contact sealed bearings have a large torque due to the sliding resistance of the seal. LE Seal optimizes the seal shape and material to achieve low torque while maintaining contact sealing. This seal successfully reduces the torque and increases the limit line speed. LE seals achieve these effects by a wedge pressure effect of a curved (semi-cylindrical) microconvex surface (fig. 5) set in the sliding area of the sealing lip, which promotes the formation of a fluid lubricant film between the sealing lip and the sliding surface of the inner ring (Table 2, Figure 6).
Fig. 5 Characteristics of ultra-low friction sealed ball bearings
The features of the developed products are:
1) Compared with the contact seal, the torque is reduced by more than 80%;
2) Support high line speed ≥50 m/s;
3) Prevent the intrusion of harmful foreign bodies.
Table 2 Test conditions
Fig. 6 Bearing temperature vs. torque
2.2 ULTAGE tapered roller bearings for automobiles
Tapered roller bearings for transmission systems such as transmissions and differentials require small and light requirements, in addition to long service life and low torque.
Automotive ULTAGE tapered roller bearings with excellent load carrying capacity and speed performance and robust convexity optimization techniques are described below to maximize bearing rolling fatigue life (fig. 7).
Fig. 7 Structure of ULTAGE tapered roller bearings for automobiles
Compared to conventional products, the characteristics of the development product are:
1) Excellent load carrying capacity
• Basic dynamic load rating - 1.3 times;
2) Long service life (compared to basic rating life)
• Standard bearings (bearing steel, quenching treatment) - 2.5 times or more,
• High-functionality type (FA process) - more than 3.8 times;
3) Excellent speed performance
• Approximately 10% increase in permissible speed;
4) Allowable tilt angle (amount of skew)
• Permissible tilt angle - up to 4 times.
Contact stress in the rolling contact area of tapered roller bearings is minimized and a special convex shape is used on the roller to reduce excessive stress at the edge of the contact area (edge load). An example calculation of the contact stress distribution of the axial section of the raceway is shown in Figure 8. With the application of ULTAGE tapered roller bearings in automobiles, bearing service life is improved by using special convex shapes to suppress edge loads in the contact area and to balance the overall contact stress distribution.
In addition, due to the long service life effect of the contact stress uniform, bearings can be designed to be smaller and lighter at the same service life. Compared to standard bearings, the use of a compact, lightweight design reduces the bearing operating torque by 60% compared to standard bearings (fig 9).
Fig. 8 Raceway contact stress distribution
Fig. 9 Bearing torque ratio
In the temperature rise test, the temperature rise is 1/3 of that of the standard bearing, confirming its superior jamming resistance, as shown in fig. 10. As shown in Figure 7, the flange and roller end shapes have been optimized to achieve superior jam resistance.
Fig. 10 Jamming resistance test (temperature rise test)
3. Concluding remarks
The development history of automotive bearings is reviewed from the perspective of reducing torque. Just as we have been developing products that are ahead of market demand through various technology developments, we plan to respond to the more demanding and rapidly changing needs that are coming. We hope to continue to contribute to society in order to contribute to the development of the next generation of vehicles that are greener, more comfortable and more useful.