Eddy-current displacement sensors use the induced eddy current principle to effectively measure changes in displacement or distance within a certain range. When the metal object under test is close to the probe, depending on the displacement or distance, the eddy-current displacement sensor outputs different voltages, so as to calculate the amount of displacement change.
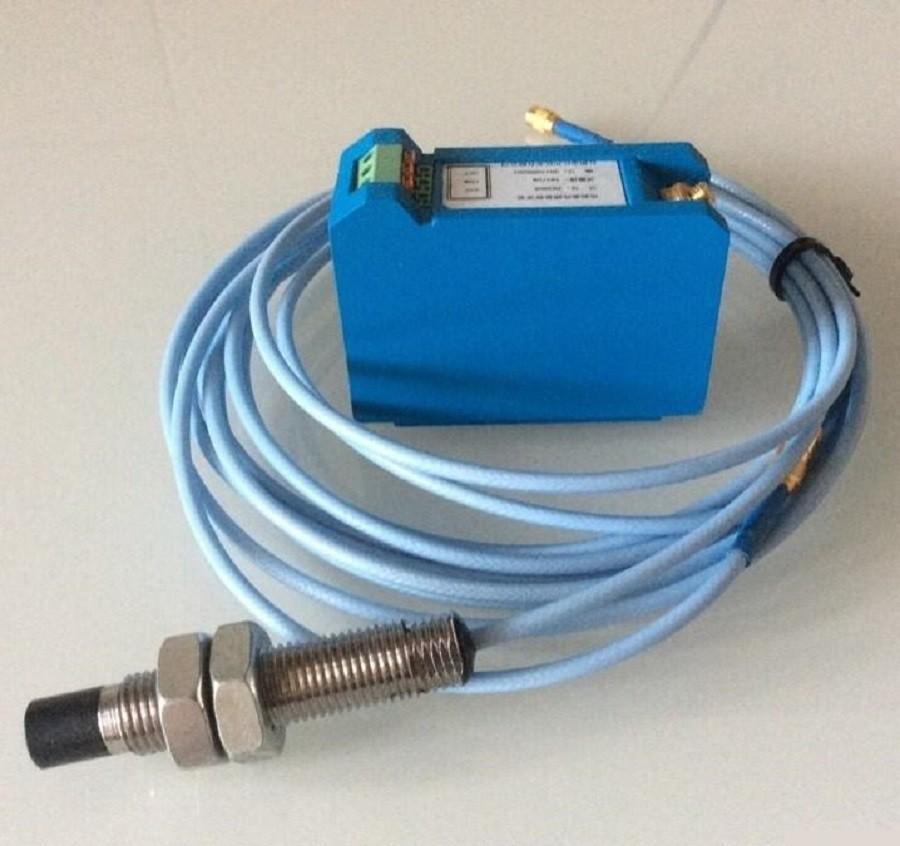
Eddy current displacement sensor
The eddy current displacement sensor is mainly composed of three parts: probe, pre-mount, and connection cable. The probe has a built-in coil and is used similarly to a proximity switch. The front end usually uses a box seal design, the front end circuit mainly includes an oscillation circuit, a voltage detection circuit, and an amplifier, and the front of the voltage-type eddy-current displacement sensor generally leads to 5 terminal blocks, namely the power supply positive +12VDC (or +24 V DC), the power supply negative, the output positive OUT+, the output negative OUT-, the ground GND. Connect the probe and the front booster to each end of the cable.
The working mechanism of the eddy-current displacement sensor is as follows: the oscillation circuit inside the preamplifier generates a high-frequency oscillation current, and the high-frequency oscillation current enters the built-in coil of the probe through the connecting cable, and the probe thus generates a high-frequency changing magnetic field. When the metal object is close to the probe, the metal object generates eddy currents. Eddy current regenerates the eddy current magnetic field, and the direction of the magnetic field line is opposite to the probe coil, which changes the impedance of the probe and causes the oscillation voltage amplitude of the oscillation circuit to change. The fluctuating oscillation voltage is amplified by the voltage detection circuit and filtered to form the output voltage. It can be seen that the output voltage change caused by the displacement change is the working mechanism of the eddy current displacement sensor.
The eddy current effect is related to a number of parameters, such as the conductivity of the metal object, permeability, probe coil diameter, distance between the probe and the metal object, oscillation frequency, etc. In eddy-current displacement sensors, probe diameter has an important effect on the measuring range and resolution. Table 1 takes the parameters of the Gack JK type eddy-current displacement sensor as an example, and lists the range, resolution, and linearity error of different probe diameters. As can be seen from the data in Table 1, the larger the probe diameter, the larger the span, but the lower the resolution, the greater the linearity error.