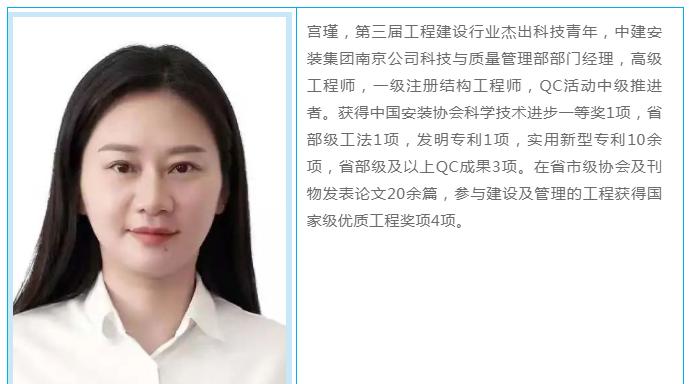
【Editor's Note】With the rapid development of the mainland's transportation industry, the scale of highway construction has been expanding, and as an important highway project, the construction task of bridges has become more arduous. The traditional construction of urban bridges mostly uses cast-in-place concrete, which has problems such as long construction period, large occupation of site, and difficulty in safety control. In this issue, "Jie Qing is coming" invited Gong Jin, the third outstanding scientific and technological youth in the engineering construction industry and the manager of the department of science and technology and quality management of China State Construction Installation Group Nanjing Company, to share with us the key technologies of G312NJ-SG5 prefabricated concrete bridge industrialization intelligent manufacturing and installation.
Hello Palace! The G312NJ-SG5 main line viaduct adopts the technology of full prefabricated assembly, and is the first prefabricated prefabricated bridge for highway engineering in Jiangsu Province. Please briefly introduce the basic situation of the project.
G312NJ-SG5 lot project is located in Nanjing 312 National Highway Nanjing Bypass Expressway to Xianyin North Section, located in Nanjing City, the traffic flow is large, the surrounding residential, office and other buildings are more dense.
The construction grade of the project is a First Class Highway. With a total length of 4.97km and a 6-lane standard, the main line viaduct is the first prefabricated bridge for highway engineering in Jiangsu Province, and it is also the widest (53m) bridge deck and the heaviest (342t) prefabricated component of a single urban bridge in China.
G312NJ-SG5 lot project is built in a fully assembled way on the ground, what are the key technologies used in the production, processing and installation of prefabricated components? Please elaborate.
G312NJ-SG5 project components are batch processed in the prefabricated plant, the degree of industrialization is high, the quality of component processing is easy to control, on-site installation avoids the use of a large number of frames, alleviating huge traffic pressure, reducing on-site noise, dust and other pollution. The key technologies are mainly reflected in the following three aspects.
1. The production of components is fully prefabricated
First of all, to create a 150,000 square meters of intelligent prefabricated base, a total of 4 production lines, for prefabricated prefabricated bridge engineering construction projects for steel processing, concrete production, component prefabrication and storage, from raw materials to finished products are perfectly produced here. Secondly, BIM technology is used to simulate the construction of prefabricated fields for elements of plane, space, and function.
2. Accurate and efficient component processing
BIM technology assists production simulation, builds physical models, and optimizes processes.
The number of steel reinforcement processing in this project is huge, and the main rib of the pier column adopts φ40 steel reinforcement, and the processing accuracy is extremely difficult to control. The prefabricated field reinforcement processing adopts imported MEP equipment, fully automatic unloading, processing, and the size is accurate to the millimeter level.
The prefabricated yard is set up with a modular strapping tire frame of steel reinforcement, and 6 workers can complete the standardized production of a 7.4t box girder steel cage in only 5 hours, and the pass rate of the steel reinforcement protection layer is more than 95%.
The fully automated hydraulic steel formwork automatically completes the overall demolding through the vertical and transverse hydraulic systems, and can be automatically moved along the rail to the next pedestal, without the need for manual and large gantry crane auxiliary disassembly, reducing labor and equipment investment by 50%.
In the process of construction and use, in addition to bearing the load of the vehicle, the bridge must also withstand adverse conditions such as meteorological conditions, chemical corrosion, man-made damage, geological disasters, etc., and the complex environment puts forward high requirements for the durability of the bridge concrete and the appearance of clear water concrete on the surface.
This project adopts technologies such as fly ash and admixtures to improve the durability of concrete, and after the cementing system is incorporated with fly ash, the water consumption of concrete is slightly reduced, and the working performance is better. At the same time, the idea of "external disease and internal treatment" is adopted, and the durability and appearance effect of the concrete of the project are ensured by incorporating functional admixtures, large-scale customized steel formwork, and strict control of the mold removal time.
3. High precision and fast installation
Due to the tight construction period on site, it is necessary to meet the opening of the "July 1st" gift in 2021, and the project uses BIM technology to simulate the construction in advance, optimize the construction process, and match the construction plan with the site.
Due to the extremely high installation accuracy requirements of this project, the reservation and embedding of prefabricated components need to be controlled within ±2mm, due to the large weight of prefabricated components, the installation time of prefabricated components that are inverted according to the construction period is short, and how to complete the project task with quality and quantity under the condition of ensuring the construction period has become a major problem to be solved first.
The project team developed a set of stereotyped positioning tooling equipment, which can accurately control the positioning of grouting sleeves and anchored bellows and the precision of rebar embedding in the processing stage, and the installation efficiency is increased by about 30%.
The length of the anchored bellows of the prefabricated cover beam section of the main line of this project is 165 cm, and the construction height of the cover beam is 190 cm. Through the PROJECT DEPARTMENT QC team to carry out BIM demonstration and on-site cover beam grouting operations, it was found that such anchored bellows had the phenomenon of grout plugging in the subsequent assembly of grouting, and the quality of the node connection was precisely the top priority of engineering quality control. In order to solve this problem, after communicating with the design, the anchored bellows are optimized, the length of the anchored bellows is adjusted partially (except for the back wall position), and the upper anchored bellows protrude from the concrete surface to realize the direct grouting of the anchored bellows, and the grouting hole of the anchored bellows in the back wall part is adjusted to the bottom of the cover beam, which not only solves the problem of the slurry plugging pipe, but also effectively ensures the quality of the bellows grout.
What achievements have been made in the construction technology of the G312NJ-SG5 lot project?
Based on the project, he published more than 10 papers, declared 3 invention patents, 10 utility model patents, and won the third prize of the excellent construction plan of the construction industry in Jiangsu Province, forming the "Application Guide for High-performance Concrete Anti-cracking Complete Sets of Key Technologies for Prefabricated Components", "Application Guide for Material Performance Improvement of Prefabricated Bridge Connection Parts", "Guidelines for The Standardization of Construction Safety of Prefabricated Concrete Bridges "Two Districts and Three Factories" (the review has been completed); Special quality inspection and evaluation standards for prefabricated concrete bridges (trial draft) (review completed).
The complete set of results evaluation of the joint declaration was appraised as an international leader by the China Highway Association.
The project was included in the "Jiangsu Traffic Quality Project Model 2020 Highlights Research Task" by the Jiangsu Provincial Department of Communications, the special guidance fund subsidy project of the Nanjing Construction Industry Modernization Promotion Leading Group, and the "Top Ten Projects" of jiangsu Trunk Highway Project in 2020; it won the provincial standardization demonstration site. Won the 2019 and 2020 Jiangsu Provincial Highway and Water Transport Project Safe Construction Site Construction Provincial "Demonstration Site", and won the 2020 Jiangsu Province Construction Standardization Three-star Site.