Rotary compressor structure:
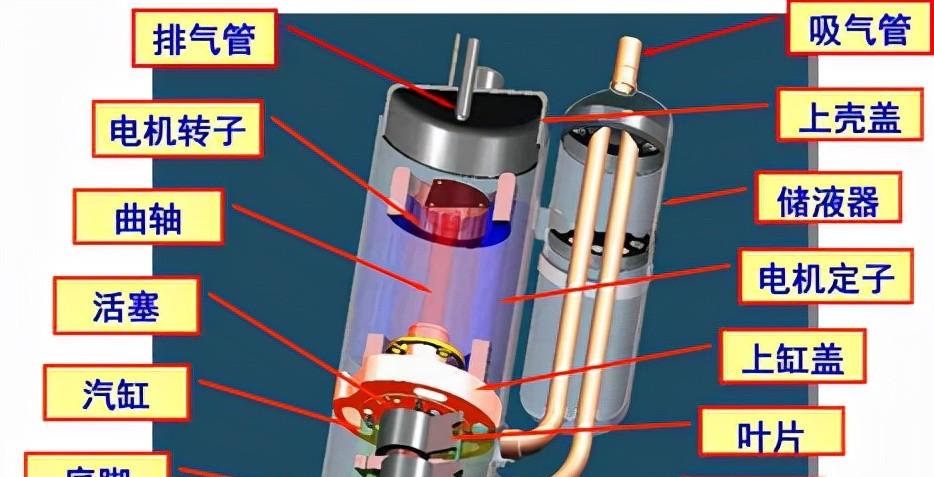
1. Why compressor opening time limit
Why should the compressor run continuously for at least 5 minutes, and stop for at least 3 minutes after shutdown before starting again?
When the compressor is not running for a long time, the refrigerant and refrigeration oil will be layered at the bottom of the compressor, and when the compressor is started, the refrigerant instead of the refrigeration oil is sucked into the pump body, and the parts cannot be fully lubricated. After the compressor runs for a period of time, the temperature rises, the refrigerant and the freezer oil are fully soluble, and the oil can smoothly enter the pump body to form an oil film protection.
After the compressor is powered on and started, the oil may be discharged into the system in large quantities, and after a period of operation, the oil entering the system returns to the compressor to establish the oil balance. If the compressor is stopped soon after starting, a large amount of refrigeration oil will remain in the system, frequently, the oil is continuously discharged and can not return to the compressor in time, which may lead to serious lack of oil in the compressor.
Shut down for at least 3 minutes before starting again to eliminate the pressure difference between compressor feed/exhaust. Because in the case of a large pressure difference, the starting torque of the motor will increase, causing the current to rise to a certain extent, the protector will operate, and the compressor will not be able to continue to run.
2. R410A/R22 lubricating oil can be mixed
1) The base oil is different
Lubricating oil from the lubrication characteristics, thermal - chemical stability, water decomposition stability, acidification stability electrical characteristics, refrigerant solubility, moisture absorption, compatibility with the material and other aspects of the evaluation, POE oil (R410a) and mineral oil (R22) two base oil differences, especially the difference in hygroscopicity is obvious, if THE POE oil is used for R22 refrigerant and the system does not add dryer according to the system requirements of R410a, it will cause capillary clogging and poor motor insulation performance.
2) The focus of additives is different
Depending on the refrigerant, the emphasis and value of the additive in the lubricating oil also vary. In general, R22 mineral oil focuses on the addition of antioxidants and defoamers, while POE oil focuses on antioxidants and acid traps. When the two are mixed, the service life of the compressor is reduced.
Note: In the process of compressor production, some processes require the addition of a certain amount of lubricating oil (such as pump body assembly), generally added is mineral oil (can not be a strong absorbent POE/ PVE, etc.), so the design should be mixed with oil test.
3. Confirm the position of the air conditioner fluoride filling
Looking at the figure above, refrigerant can generally be added in three places: the condenser, the reservoir side of the compressor and the evaporator (the throttle device cannot be filled due to its own structural limitations).
Liquid dosing at the reservoir, when the system starts, the liquid refrigerant will continuously impact the cylinder, so that the compressor produces a hydraulic shock, the damage to the compressor is extremely fatal, while the liquid refrigerant directly into the compressor, may adhere to the terminals, causing instantaneous insulation, poor pressure resistance; the same reason, in the evaporator side of the dosing will also occur.
For the condenser, because of its relatively large volume, it can store a sufficient amount of refrigerant, and there will be no adverse consequences when starting, and the filling speed is fast and safe; so the method of filling the condenser is generally used.
4. Maximum allowable charge
When the compressor is in use, the amount of refrigerant sealed should be controlled within the allowable range, if the amount of refrigerant is too much, the following defects may be produced:
5. The condensation temperature is lower than the bottom of the compressor 6
In continuous operation, ΔT should be above 6; ΔT should be above 0 during intermittent operation, and the significance of controlling ΔT:
Compared with the condensation temperature (equivalent to the saturation temperature of the housing pressure), when the bottom temperature of the compressor is low, the refrigerant will continue to condense in the compressor, at which time the oil is diluted by the refrigerant, resulting in severe wear of the sliding parts due to insufficient strength of the oil film. The provision of ΔT is to ensure that the refrigerant does not condense in the compressor and prevent the occurrence of the above defects.
Common causes of low ΔT:
Excessive amount of refrigerant sealing; inappropriate capillary; excessive cooling of the compressor;
Intermittent operation of frequent, short-term operations.
6. Motor winding temperature
The conditions of use should be below 127 at maximum load.
Determination method: Within 3 seconds after the compressor stops, the main winding resistance is determined by the Wheatstone bridge or the digital ohmmeter, and then calculated according to the following formula: winding temperature t = [R2 (T1 + 234.5) / R1] -234.5
R2: Determination of resistance; R1: Winding resistance in cold state; T1: cold motor temperature.
If the winding temperature exceeds the conditions of use, it may produce undesirable conditions:
Accelerated aging of winding enameled wires (motor burnout);
The aging rate of insulation materials is accelerated (the insulation life is halved for every 10 increases in temperature);
Deterioration of the oil due to overheating (decrease in lubricating properties);
7. Built-in overload protector-UP3
UP3 contacts are normally closed during normal work, when the internal temperature of the UP3-perceived compressor rises, the "bimetallic sheet" action drives the contact pole to jump away from the normally closed contact, cut off the current loop, and protect the compressor. Since the UP3 is connected to the C-end of the press sealed binding post, the main and secondary coils can be protected at the same time.
The bimetallic sheet is temperature triggered for protective action. The trigger temperature source comes from two parts: the electric heating heat as the current passes, and the temperature perceived by the up3's metal casing.
8. Thermal switch and thermistor for frequency conversion
Both the thermal switch and the thermistor are independent of the compressor wiring and are not directly connected in series in the compressor circuit.
The thermal switch controls the on-off of the compressor control circuit by feeling the temperature of the compressor housing cover.
Thermistors are negative temperature characteristics of the element that has a feedback signal output to the microprocessor. A set of temperature and resistance tables are pre-entered in the microprocessor. Each time a resistance value is measured, the corresponding temperature can be reflected in the microcomputer. Finally achieve the role of temperature control.
9. After fluoride filling, first run and then check the electrical performance
After the liquid refrigerant is sealed, the liquid refrigerant may condense on the terminal blocks, and the insulation impedance of the liquid refrigerant is much smaller than that of the gaseous refrigerant, and the insulation level of the whole machine will drop instantaneously. After operation, the liquid refrigerant evaporates and the insulation returns to normal.
10. Why should the system specify the vacuum level
The degree of vacuum directly affects the moisture content in the system, and the lower the vacuum, the less water vapor remains in the system.
1) Ice plugging of capillaries and expansion valves during heating;
2) The acidic environment caused by moisture will aggravate the deterioration of oil and the burning of the motor; it will erode parts and components, which will have a fatal impact on the compressor.
3) It will produce the phenomenon of "copper plating", which will affect the mating gap and sealing effect of the parts; the serious electroplated copper phenomenon will directly lead to the blockage of the mating parts.
4) The refrigerant will decompose;
5) The air is an uncoagulated gas, resulting in high system pressure and unstable working conditions.
System water: there is water in the air conditioning system, and the mechanical part of the compressor will have a "copper plating" phenomenon, which will produce the following chemical reactions in theory:
1) Freon (CHCLF2) refrigerant does not react directly with water, but when in contact with metals, it slowly reacts with water, causing hydrolysis to form acid (HCL).
2) At high temperatures, HCL reacts with metals in the refrigeration system (such as copper in copper tubes) to form CuCL2. CuCL2 then reacts with Fe in the mechanical part of the compressor, causing cu to be displaced and attached to the mechanical parts of the compressor. In addition, for every 10 times increase in temperature, the reaction rate is increased by 2 times.
2HCL+Cu+(O)→CuCL2+H2O
Fe+CuC2 H2O FeCl2+Cu
The reasons for the failure of the vacuum degree are:
There is no vacuum extraction from both sides of high and low pressure;
Insufficient suction time; leakage of the system;
Vacuum levels exceeding the specified level may also result in undesirable conditions:
Ice plugging of capillaries and expansion valves during heating;
The resulting acid substances will erode the motor and blade springs, etc.;
The oxidation of refrigeration oil is intensified; the refrigerant will decompose;
The air is an uncoagulated gas, resulting in high system pressure and unstable working conditions;
The exhaust temperature rises.
11. Precautions when the system is in a vacuum state
In a vacuum state, it is strictly forbidden for the compressor to operate or apply electrical impulses.
Because in the vacuum state, electrons are easily freed out, so discharge is generated. With media (such as refrigerant and air) between charged bodies, electrons are not easily free.
12. How to judge whether the oil surface and oil amount are appropriate
There are two main types of confirmations:
1) Sight microscopic observation, observe whether the oil in the compressor is abnormally transferred to the system under each working condition (including special working conditions), and whether the oil surface at a special time point is reduced.
2) Intercept the mixture of oil + refrigerant during the test, and the dilution rate of the test oil does not exceed the allowable value.
Through the above measures, we can basically determine whether the return oil and refrigerant charge of a system are suitable for compressor reliability. The compressor and the air conditioning system have a match, and a simple test cannot completely assess all the problems that may occur in long-term operation.
13. Confirm the wiring method
Compressors may not be able to play a protective role in the case of miswired, resulting in compressor burnout.
It is recommended to use double-station wiring confirmation. This minimizes human error.
There is only one correct way to wiring the compressor: C-M-S, while the other five wiring methods are wrong.
Improper operation can cause damage to the compressor, resulting in unnecessary losses.
In general, wiring errors can cause the secondary coil to burn out.
It is recommended to run after fluoride filling and then check the electrical performance.
After the liquid refrigerant is sealed, there will be an instantaneous decrease in insulation level, because the liquid refrigerant may condense on the terminal blocks, and because the insulation impedance of the liquid refrigerant is much smaller than that of the gaseous refrigerant, the insulation of the whole machine will decrease. After operation, the liquid refrigerant evaporates and the insulation returns to normal.
14. Insufficient oil return of the system
Effect of refrigeration oil:
Lubrication, effectively prevent the wear of mechanical parts.
Oil seal action, maintain high and low pressure difference.
Take away the heat generated by friction in time.
Part of the refrigeration oil in the compressor is discharged into the system with the refrigerant. The discharged oil is dissolved in the liquid refrigerant in the condenser; when it enters the evaporator, it gradually separates from the refrigerant and returns to the compressor with the gas. However, if the refrigeration oil cannot be returned smoothly after discharge, the system oil return is insufficient, resulting in:
Poor oil return may occur: poor lubrication leads to wear and jamming of moving parts; compressor capacity is reduced; overheating.
The main causes of poor oil reflux are:
Too much refrigerant, the amount of oil discharged increases; the piping is not suitable (the piping is too long, the pipe diameter is large);
Operate under extremely low temperature conditions, short interval between intermittent operations, small amount of refrigerant circulation, low pressure;
The capillary is not suitable.
Precautions for compressor use:
1. The compressor is wired by mistake
There is only one correct way to wiring the compressor, everything else is wrong. Due to miswiring, the thermal protector may lose its protective function, resulting in the compressor burning, generally causing the secondary coil to burn out.
For three-phase compressors, there should be a phase sequence protection device; it is recommended to use two-station wiring confirmation, which can minimize human error.
2. Foreign objects enter the air conditioning system
System residue sources may include:
1) Fine copper chips are produced when the copper pipe is cut.
2) Processing oil, impurities and other foreign matter in the process of system manufacturing
3) The compressor is exposed to the air for a long time, and dust and water vapor enter.
4) When welding, the internal surface of the pipeline will produce an oxide film, so it should be filled with nitrogen to protect it when welding
Effect of residues on the system:
1) It will aggravate the wear of the friction surface of the moving parts and block the pump oil channel;
2) When the compressor contains moisture, fiber, dust and other tiny inclusions, it may be adsorbed on the motor windings and terminal posts, reducing the insulation performance of the whole machine.
3) Processing oil will also react with refrigerant or refrigeration oil, resulting in sludge, coke, attached to the exhaust valve plate, suction filter, capillary, causing blockage.
3. System water inlet
The moisture content in the air conditioner system should be controlled below 75ppm (Shanghai Hitachi recommended value).
Ways of water entry:
Air conditioners enter water during the manufacturing process; refrigerants contain more moisture;
Leakage of the system caused by the intrusion of moisture; the compressor is improperly sealed and placed open;
The vacuum level of the system does not meet the standard; the installation is incomplete.
4. Abnormal sound
There are many causes of abnormal tones, which should be treated differently.
5. Overload operation
Compressors have the maximum operating conditions, if exceeded the allowable range, the following consequences will occur:
1) Due to the excessively high exhaust temperature, the surface of the exhaust valve plate is carbonized with refrigerated oil.
2) Due to the excessive pressure difference between the high and low pressure of the pump body, the vane groove is worn.
3) Reduced service life.
6. Refrigerant leakage
The air conditioning system has reduced refrigerant due to leakage. Such a long-term operation, so that the heat generated by the motor can not be brought out by the refrigerant; the exhaust temperature will also increase accordingly, when the temperature is too high, R22 begins to thermally decompose, generating acid and water. It will also free the carbon in the refrigerated oil, forming carbon deposits; refrigerant leakage can also lead to poor oil return
7. Abnormal power receiving
In the market return machine, there are many motor main coils or sub-coils uniformly overheating, and the difference between the turn short circuit and the motor itself is obvious.
Uniform overheating of the motor is generally caused by the external large current impact or long-term overheating. Such as abnormal voltage, low temperature and low voltage start-up, etc. #转子 #