1、
The top floor of the stairwell is equipped with a 0.15M high platform measure at the base of the horizontal railing. Figure 1:
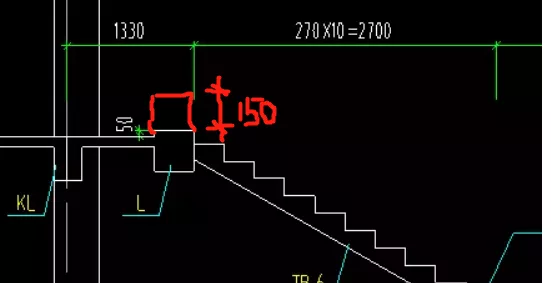
Such as the staircase design drawing of an office building, the structural drawing is not designed on the 0.15M high platform, generally in the preparation of the list of quotations will not consider this platform, the platform is conventional concrete pouring, so experienced budgeters must calculate the amount of concrete engineering and formwork here.
2、
According to the "Interim Regulations on Fire Prevention of External Insulation Systems and Exterior Walls of Civil Buildings", the height of the building is less than 24M, and a horizontal fireproof isolation belt should be set up for every three layers of insulation materials. If a mall has only four storeys, the cornice height is 21.6 meters. Then it is necessary to set up a construction fireproof isolation belt at the location of the three floors. The drawings have only simple instructions, as shown in Figure 2:
The drawing only explains the practice of the roof external wall fire barrier, so the budgeter must be familiar with this mandatory specification, and must increase the group price of the external wall fire barrier. The circumference of the outer wall of a large shopping mall is about 600 meters, just imagine that the fireproof isolation belt needs to increase the area of 300 square meters, which is also a key group price cost, if calculated according to 56 yuan / square, it will miss the project cost of 16800 yuan.
3、
Concrete structural columns should be added to the walls at the upper and lower ends of the stairwell. Figure 3:
That is to say, the masonry wall of the staircase must be built concrete construction columns, some drawing design institutes will design, some drawing design institutes will not design on the drawing plan, the cost of the need to calculate the group price of concrete structural columns in accordance with mandatory specifications. The reinforcement of the structural column can refer to the normal general practice of reinforcement, when a project is high-rise, the engineering volume of the structural column is also a lot of cost, which directly affects the analysis of the cost.
4、
Basement waterproofing should adopt the overall waterproofing method of forming the periphery, when the design water level is lower than the basement floor 0.3M-0.5M, and the soil and backfill soil within the base area cannot form the upper layer of water stagnation, the moisture-proof method is adopted, otherwise, the basement must be waterproof. Figure 4:
That is to say, the side of the basic component must be plastered with waterproof mortar moisture-proof layer, especially in the bidding budget, that is, the drawing does not indicate whether it is waterproof mortar, and the group price should also be calculated according to the normal moisture-proof. The above figure only indicates the location of the wall, but the moisture-proof layer of the plus or minus 0.00 lower component is not explained, this is the construction of the mandatory specification, and the acceptance standard needs to be moisture-proof, so the cost of the cost factor should take into account this content. If the project is a large supermarket, the foundation components and foundation pits below are relatively many, and the amount of waterproof mortar plastering on the side will also increase relatively, which directly affects the accounting and profit of construction costs.
5、
Strictly control the thickness of the cast-in-place plate and the thickness of the steel reinforcement protective layer in the cast-in-place plate, and the steel bar stool rib with a spacing of not more than 500mm should be provided under the negative bending moment rib and the steel mesh piece, so as to ensure that the steel bar is not displaced when pouring concrete. Figure 5:
In the case that the drawings do not explain, the general stool ribs are not marked on the drawings, and the budget is only calculated according to the normal plate ribs. For example, the quota of Shandong Province is stated:
First of all, one per square meter here is not enough for the actual mandatory specification requirements, the mandatory specification requires the spacing to be set no more than 500mm, the amount of instructions is not designed in the case of one per square meter, the mandatory specification and the quota description compared, the amount of engineering is far from enough. If the amount of cast-in-place board in the project is relatively large, the reinforcement will be much worse, especially the contract with a fixed total price quoted in the list, so the coster must be familiar with the mandatory specifications of the location, combined with the quota description, and the project quantity can be quoted only if it is calculated in place.
6、
Roof exhaust system specifications, in order to prevent leakage of the roof due to water accumulation, bubbles, flow cracking and other phenomena, in the slope layer or insulation layer to set up exhaust holes, exhaust ducts, convenient construction, correct arrangement, height unity and other advantages, the original exhaust holes basically use steel pipes, plastic pipes. General spacing of 6 meters, plum-shaped settings, every 36 square meters should be set up an exhaust hole. In the drainage hole base layer to increase the waterproof additional layer, because the membrane waterproof layer is attached to the exhaust pipe, affecting the aesthetics, generally set a 300mm high, 110UPVC pipe on the outside, so that the exhaust pipe 75 pipe diameter and 110 UPVC pipe diameter between the waterproof paste embedded tightly, after filling than the 110 PVC pipe 10mm lower. This look must also be done for construction, with the amount of work needing to be calculated for exhaust holes and jackets, and the amount of work for the waterproof accessory layer must also be increased. If you do not understand the practice of mandatory specification of roof exhaust holes, you cannot calculate the quantity and price of these quantities, which is also a hidden quantity cost of the construction unit cost.
The six mandatory specifications of the above examples are not required to be mentioned in the design instructions on the design drawings, but the actual construction must be carried out these procedures, and a qualified cost personnel must be clear about the depth and extensibility of these procedures on the project cost, and must be in place and calculated, that is, even if it is to audit, it is necessary to leave a first-hand image data or a written visa to supplement these construction procedures, and the ultimate purpose is to calculate the amount and price of the project that is not missed. These cost traps will always find information with the rigor of construction!