No matter in what industry, presumably everyone is most concerned about the efficiency of the problem, the introduction of 3D scanning technology, can be from the production cost effective control and production efficiency effective improvement two aspects, for the mold manufacturing industry to bring considerable improvement in economic benefits, today and we discuss the application space of 3D scanning equipment in the mold manufacturing industry.
The handheld 3D scanner, as a flexible and portable mobile measuring device, can work directly on different complex industrial sites, obtaining 3D data quickly, accurately and stably, and generating intuitive and visual inspection reports.
So, in what links can the use of 3D scanning equipment effectively improve the overall benefits? Next, let's take a look at the specific application of 3D scanners in mold manufacturing.
Mold blank processing allowance detection
Many molds are made of special alloy steel, which has a high cost of raw materials. In mold manufacturing, if the processing allowance of the blank is too much, it will cause waste of raw materials; conversely, if the processing allowance of the blank is insufficient, it will lead to the final mold quality being unqualified, and the whole set will be scrapped.
Therefore, if the processing allowance of the mold blank can be more accurately controlled before processing, it can be used with the least amount of materials to produce qualified products and effectively control the cost of mold manufacturing. Next, let's look at the use of 3D scanners for mold blank margin detection through specific cases, and in what ways can bring economic benefits to mold manufacturers. In this case, Sikan used the composite 3D scanner KSCAN-Magic to inspect the machining allowance of a large mold blank.
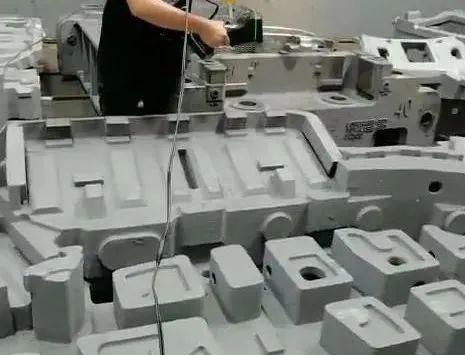
△ Direct hit scan scene
Advantages of the program
Flexible and portable, work anytime, anywhere
Compared with stationary measuring equipment, handheld 3D scanners are smart and portable, have low operating thresholds, low requirements on the working environment, and are less affected by the environment, so there is no need to reopen the measurement site, and the measurement work can be carried out anytime and anywhere, which can effectively reduce the cost of testing land and testing time.
Efficient and accurate, comprehensive data
KSCAN-Magic is equipped with 5 working modes, scanning surface width up to 1440 mm x 860 mm, quickly obtain the overall three-dimensional data of the mold blank, with fine scanning and deep hole scanning mode, can accurately obtain complex surfaces, deep holes and dead angle position of three-dimensional data, compared to the traditional detection method, the data is more complete and comprehensive, for the subsequent processing allowance determination to provide a reliable, comprehensive data basis, to avoid the waste of raw materials.
Photogrammetry, one machine for multiple uses
Handheld 3D scanners have cumulative errors, and photogrammetry systems can reduce cumulative errors. In general, the accuracy of parts with higher requirements, if the size of more than 1.5m has the accuracy requirements of the parts, it is recommended to use photogrammetry equipment to assist in the detection.
The mold blank is large in size, and Sikan's KSCAN-Magic has a built-in photogrammetry system that can complete the scanning task without the need for auxiliary equipment.
Visualize reports in real time
With professional scanning software, the 3D inspection results are intuitive in real time. The data obtained by the scan is compared with the CAD model to generate a chromatographic deviation map, the reading threshold is low, and the detection workers can analyze the subsequent processing allowance in a simple and timely manner.
In general, the total processing allowance is not removed at one time, but is gradually removed in each process. In the process of blank processing, it is common practice to use the part number mold to offset the maximum thickness and generate a machining program.
In many cases, the machining center's cutter head does not touch the part and runs empty. The three-dimensional data of mold blanks obtained by 3D scanners is more comprehensive and accurate, and can also reduce the phenomenon of empty running to a greater extent, optimize processing procedures, improve the production pass rate of molds, and shorten the manufacturing cycle of molds.
Pre-mold inspection
Mold quality directly determines the quality of the product, after the mold is subjected to a certain degree of wear, the product quality can not be guaranteed, so the mold repair work is very important.
Traditionally, manual experience has been used to determine the area of the mold, and the time to work on the mold often takes several weeks. This not only requires a lot of time and labor costs, but also some complex surface and corner data are easy to be missed. If the 3D scanner is used to scan and detect, the mold repair area can be determined more quickly and accurately, which can greatly shorten the mold repair cycle and improve work efficiency.
Sikan Technology once used tracking 3D scanner TrackScan-P42 to conduct post-processing inspection of a large hot forging mold, providing a comprehensive and reliable data basis for its subsequent mold repair work.
Extremely fast and efficient, all the way to the end
Because of its large size and heavy quality, it is not easy to move away from the work workshop for testing. In the traditional way, the method of meter measurement is used, and the size area of this hot forging mold is large, and the detection efficiency is low.
With a scan rate of up to 1,900,000 measurements/sec on the TrackScan-P42, the staff acquired full-size 3D data from the hot-forging mold in just 5 minutes. The overall mold repair working time has been shortened from a few weeks to less than 10 days, which has greatly improved the efficiency of mold repair.
No fear of details, super adaptable
This large hot forging mold has many cavity features, deep hole deep groove, 7 parallel blue laser fine scanning and single beam deep hole dead angle scanning mode, the deep pit details are also at a glance, and the three-dimensional data of the mold can be completely obtained.
TrackScan-P42 has super environmental adaptability, no fear of bright and black surfaces, can easily obtain the complete 3D data of the hot forging mold brightener surface.
No need to stick, smart tracking
The TrackScan-P42 tracking 3D scanner uses intelligent optical tracking technology to eliminate the need for adhesion, eliminating the need for adhesion time and damaging the inspection surface.
Visual reports, intuitive and clear
The operating threshold is low, and the final visual report is formed, which is highly readable. The resulting contrasting chromatogram enables precise identification of areas where trimming is required.
Other applications
Typically, the clamping analysis of a stamping die is time-consuming and laborious. At this time, if the 3D scanner is used to obtain the three-dimensional data of the upper and lower molds, it is flexible and efficient, and can simulate the mold-clamp analysis more efficiently, providing an accurate data basis for the modification scheme.
In addition, 3D scanning can also be used to digitally back up the mold, providing a data basis for subsequent mold repair, optimization and redesign.
All in all, the use of handheld 3D scanners can show the scanning results more accurately, efficiently and intuitively, effectively improve work efficiency, reduce time and labor costs in the stages of mold design, production, repair, etc., and bring considerable economic benefits to the production and manufacture of molds.